In the realm of conveyor belt systems, herringbone rubber lagging stands out as a critical innovation that enhances functionality and efficiency. This article delves into the essentials of herringbone rubber lagging, highlighting its benefits, applications, and why it should be your go-to solution for conveyor belt issues.
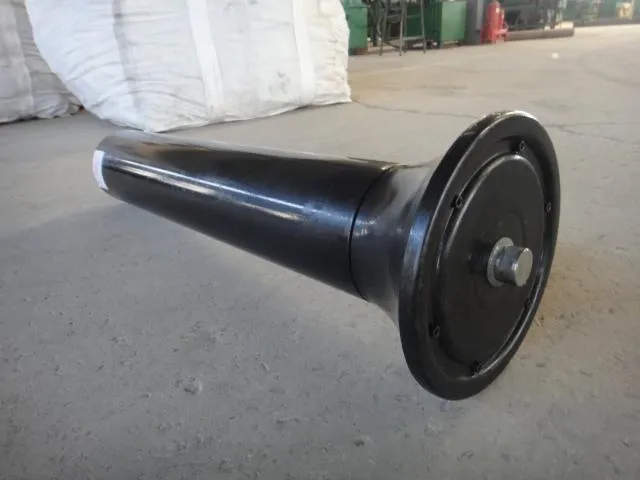
Herringbone rubber lagging—a staple in modern conveyor belt systems—features a distinctive pattern, akin to the bones of a herring fish, designed to optimize grip and performance. This pattern is not just a stylistic choice; it plays a pivotal role in improving traction between the belt and the pulley, minimizing slippage and maximizing productivity.
The benefits of herringbone rubber lagging are manifold. Firstly, its design enhances friction significantly, which is crucial in environments where materials might otherwise cause slippage due to moisture or dust. This ensures a steadier, more reliable belt movement, reducing downtime and maintenance costs. The increased friction also translates to better power transmission efficiency, which can lead to energy savings and improved overall operational cost-efficiency for businesses.
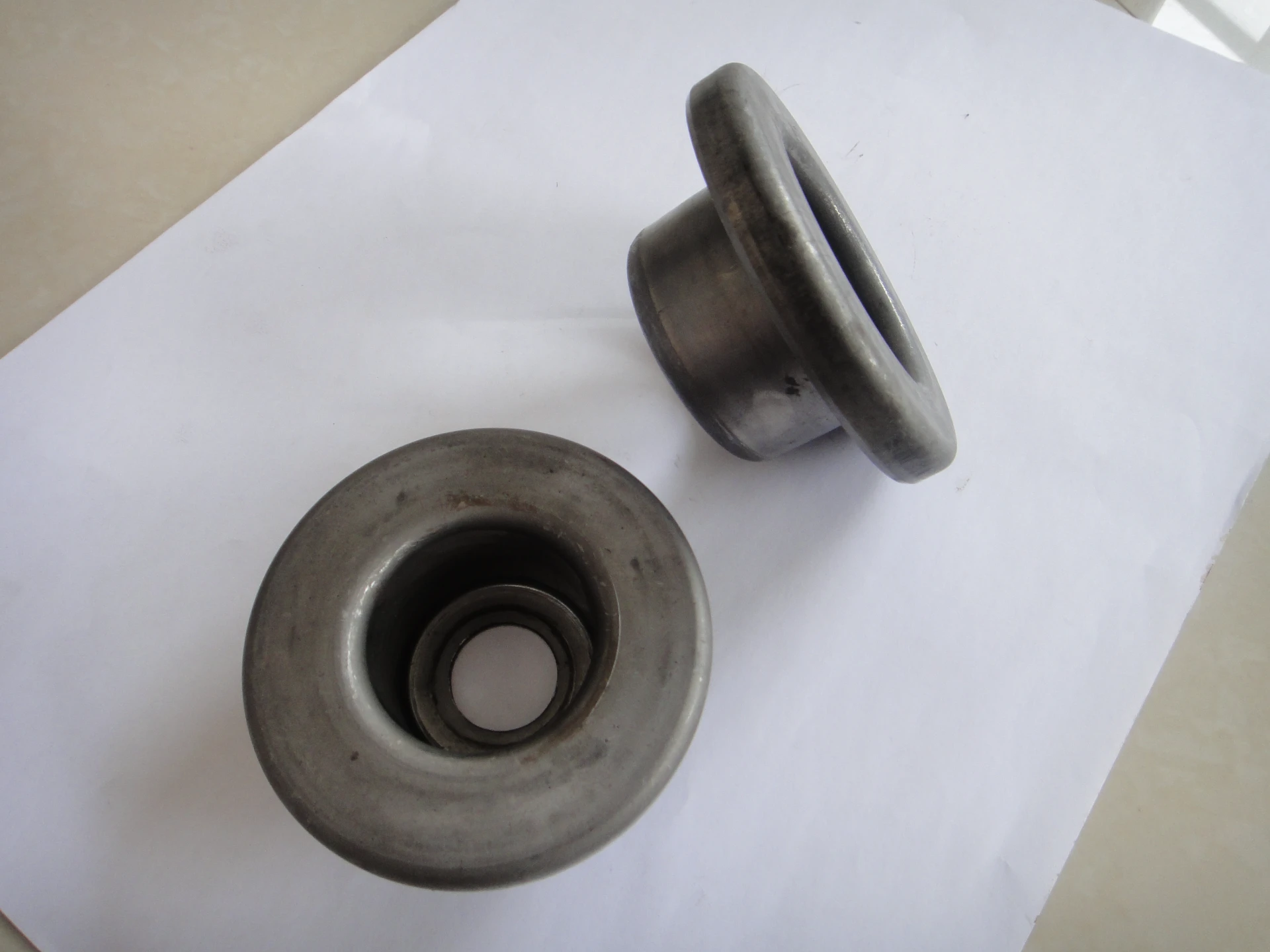
From an application standpoint, herringbone rubber lagging is versatile. It is extensively used across various industries, including mining, manufacturing, and food processing. In mining, where conditions can be harsh and materials can be abrasive, herringbone patterns provide the durability needed to withstand these challenges. Within manufacturing, they ensure precision and speed, critical factors in maintaining competitive edges. In the food industry, hygiene and safety are paramount, and herringbone designs ensure easy cleaning and minimal contamination risk.
Expert insights highlight that selecting the right type of lagging is crucial for maximizing the life and performance of a conveyor system.
Herringbone rubber lagging, with its durability and specific pattern, often leads these choices. Its capability to handle both high tension environments and rapid operational speeds makes it suitable for both small-scale operations and large enterprises looking to scale efficiency.
herringbone rubber lagging
Trustworthiness and reliability are core to its widespread adoption. Companies report back on its long-term efficiency and the tangible reductions in maintenance interventions. By preventing belt misalignment and uneven wear, herringbone rubber lagging not only helps in maintaining operational consistency but also extends the lifespan of the conveyor system, offering tremendous ROI for industrial players.
The authoritativeness of herringbone rubber lagging in conveyor systems is further validated by industry endorsements and certifications. Many manufacturers align with international safety and production standards, ensuring that their lagging solutions meet rigorous quality checks. This provides peace of mind to companies transitioning or upgrading their conveyor units to include herringbone lagging solutions.
For those seeking a product that combines performance with cost-effectiveness, herringbone rubber lagging emerges as a prefered choice. Leveraging both the expertise of its design and the endorsements it has garnered, industries can achieve an enhanced level of operational competence. Its installation might require initial capital, but the optimization it provides in belt operations is unmatched, making it a strategic investment for long-term gains.
In conclusion, investing in herringbone rubber lagging is not merely a purchase but a strategic move to bolster operational efficiency in demanding environments. Its construction, durability, and practical benefits position it as a leader in the conveyor belt ecosystem. Whether you're tackling issues of slippage, wear, or inefficiency, the specialized design of herringbone rubber lagging is a testament to innovation in motion technology. Witness the transformation it brings to your conveyor systems, making them more robust, reliable, and ready for the future's challenges.