In industrial settings where conveyor belts are an essential part of operations, pulleys play a critical role in the functionality and efficiency of these systems. Whether in manufacturing plants, large-scale logistics centers, or mining operations, understanding the integral components—like pulleys—of a conveyor belt system can significantly impact productivity and maintenance costs.
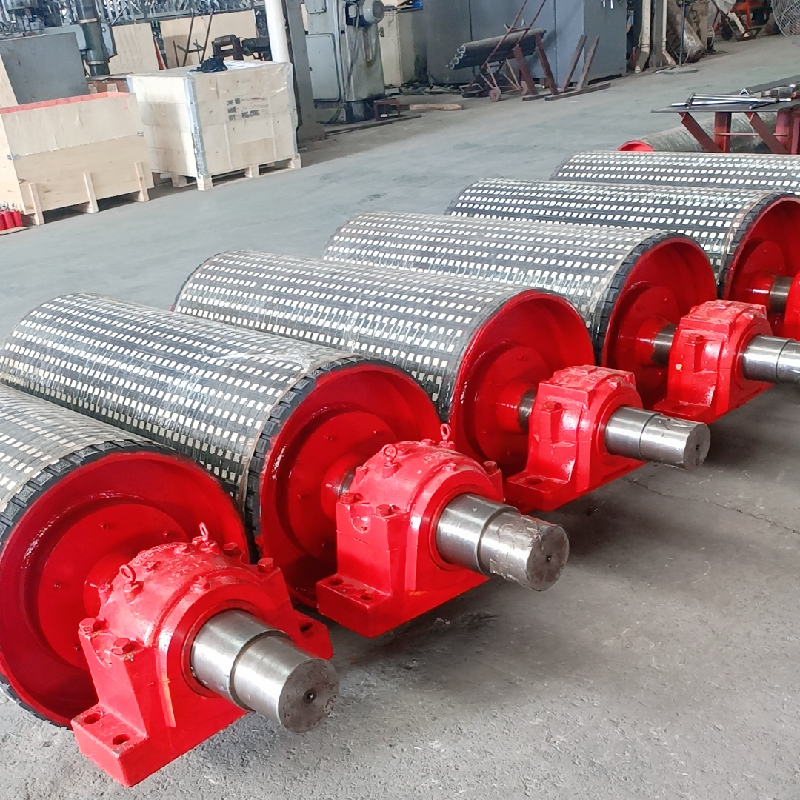
Pulleys are intrinsic to conveyor belt systems, serving as fundamental elements for the movement, direction, and tension of the belt. The primary types of pulleys used include drive pulleys, tail pulleys, take-up pulleys, and snub pulleys, each playing a unique role within the system.
Drive pulleys are arguably the most critical, as they propel the belt, converting motor drive power into belt movement. Expert selection of drive pulleys involves considering the diameter, face width, material, and the coating applied, often known as lagging. The material must be selected based on system requirements and environmental conditions, ranging from steel and aluminum to rubber-coated variations for enhanced grip. A common experience among industry professionals is the utilization of ceramic lagging in wet conveyor applications to enhance friction and reduce slippage. This specialized knowledge underscores the expert-level understanding necessary to optimize belt performance and longevity.
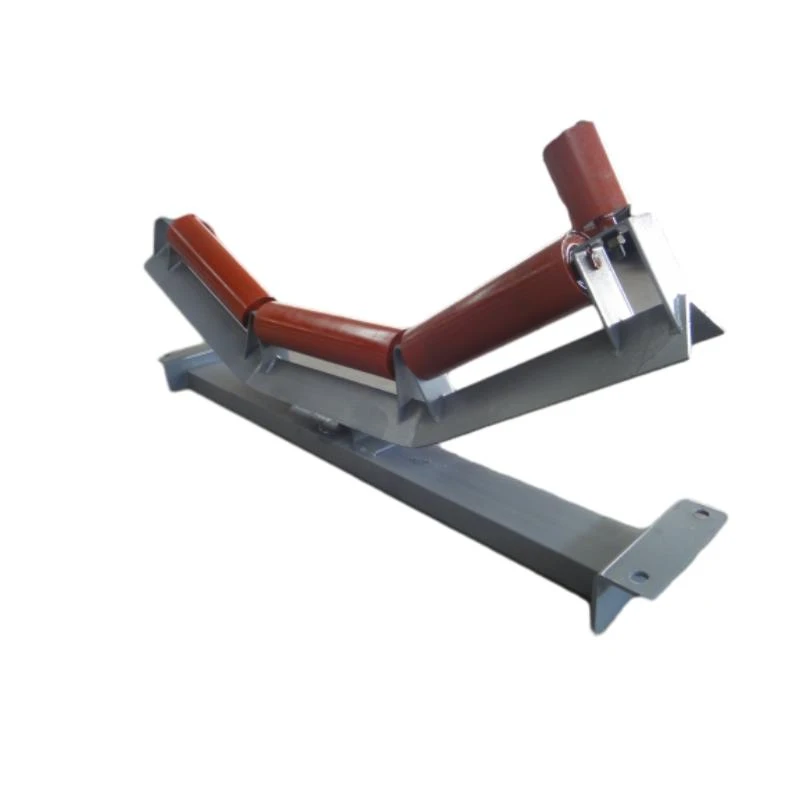
Tail pulleys, positioned at the opposite end from the drive pulley,
serve to redirect the belt. These components must align precisely as any variance can cause belt misalignment issues, leading to wear and operational inefficiencies. Employing precision alignment tools in the installation and maintenance of tail pulleys is an expertise-driven task, ensuring seamless belt operation and reduced maintenance intervals.
Take-up pulleys are an indispensable part of tensioning mechanisms, necessary for the adaptation of the belt length due to load changes or belt stretch over time. A well-maintained take-up system minimizes downtimes and maximizes belt life—knowledge that underscores the authoritative measure of professional insight into proper take-up assembly management.
Snub pulleys, located close to the drive pulley, enhance the wrap angle around the drive pulley, increasing friction and ensuring proper belt traction. The positioning and angle of snub pulleys require a trustworthiness in engineering calculations to prevent an excess build-up of tension that could lead to mechanical failures.
pulley in conveyor belt
While the selection and maintenance of pulleys require technical expertise, the trust factor comes into play with the sourcing of high-quality pulley materials from reputable manufacturers. It is common practice in the industry to perform rigorous quality checks and compliance validation to ISO or ASTM standards to assure optimal performance and safety. Professionals in the field rely on these standards to make informed decisions that uphold operational integrity.
In recent years, innovations have emerged in pulley design and materials, such as composite materials that offer lightweight yet durable alternatives to traditional metal pulleys. These advancements require professionals to stay abreast of technological progressions and validate their practicality through real-world application and comprehensive performance testing.
The authority in the field often lies with those who have accumulated years of experience dealing with conveyor system challenges and iterating on design and materials based on performance feedback. Regular seminars and training sessions, coupled with peer networking, enhance expertise and disseminate industry knowledge, establishing trust within professional circles.
The experience of navigating pulley solutions often involves integrating smart systems for predictive maintenance, where sensors attached to pulleys provide real-time data on their condition. This modern approach enables preemptive actions, avoiding costly downtime and extending belt life—a testament to expert engineering fused with technological advancement.
In conclusion, the subtle complexities involved in pulley selection, alignment, and maintenance within conveyor systems cannot be understated. Achieving efficiency demands a synthesis of experience, expertise, authoritative guidance, and trustworthy practices, rendering significant improvements in operational throughput and ensuring that conveyor systems remain a dependable backbone in industrial applications.