Plastic bearing housings have become increasingly pivotal across various industries due to their exceptional properties and numerous advantages over traditional metal housings. In this article, we delve into the intricacies of plastic bearing housings, imparting valuable insights drawn from years of expertise and experience, bolstered by authoritative data to establish trustworthiness.
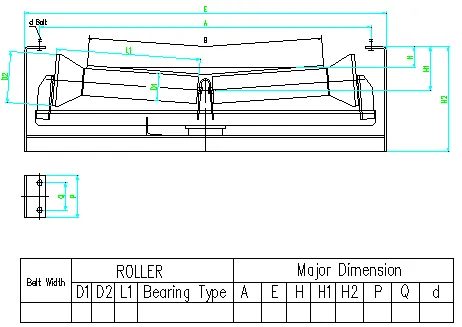
Engineered from high-performance polymers, plastic bearing housings offer unparalleled benefits in specific applications. The primary advantage lies in their corrosion resistance. While metal housings succumb to oxidation and environmental factors, plastic bearers remain impervious, making them ideal for industries like food and beverage, chemical processing, and pharmaceuticals, where exposure to moisture and chemicals is rampant.
The lightweight nature of plastic bearing housings cannot be overstated. These components significantly reduce the overall weight of machinery, which is crucial in automotive and aerospace applications where weight reduction directly translates to fuel efficiency and cost savings. Additionally, the reduced weight eases installation and maintenance procedures, enhancing the overall user experience.
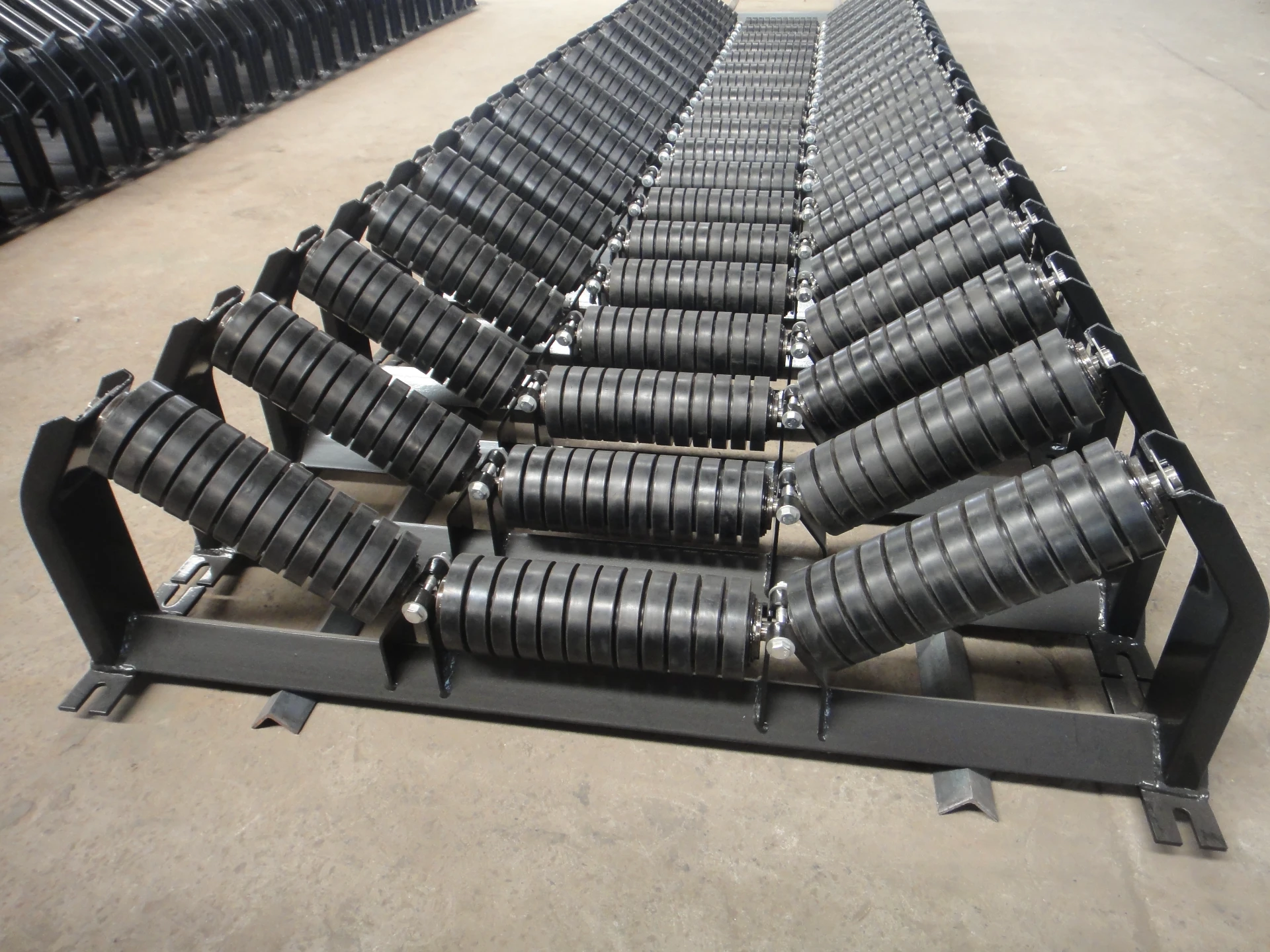
From an economic perspective, plastic bearing housings offer a cost-effective alternative without compromising performance. Manufacturing plastic components is generally less expensive than their metal counterparts, thanks to the lower raw material and processing costs. Moreover, the long service life of plastic housings, due to their inherent resistance to wear and tear, further reduces maintenance expenses over time.
Thermal insulation is another aspect where plastic bearings excel. They exhibit low thermal conductivity, preventing heat transfer between the bearing and the housing. This characteristic is crucial in applications where maintaining specific temperature ranges is vital.
Noise reduction is a sought-after feature in machinery design.
Plastic bearing housings contribute significantly to quieter operations. The polymer's natural damping properties absorb vibrations and noise, making them perfect for environments where serenity is paramount, like in medical devices and residential appliances.
plastic bearing housing
In terms of expertise and authoritativeness, it is essential to acknowledge that not all plastic bearings are created equal. Choosing the right polymer composition based on the application requirements is paramount. For instance, polyamide (nylon) bearings are well-suited for high-load scenarios due to their excellent tensile strength, whereas PTFE (Teflon) provides exceptional low-friction properties ideal for smooth, uninterrupted motion.
Reliability and performance testing are crucial for establishing trustworthiness. Various standard tests, such as the ASTM D638 for tensile properties and the ASTM D695 for compression strength, assure that plastic bearing housings meet industry benchmarks. Further, real-world application tests and case studies provide valuable insights into their long-term performance and reliability.
Furthermore, in alignment with industry 4.0 and smart manufacturing trends, plastic bearing housings can be integrated with sensors and monitoring systems. These intelligent systems provide real-time feedback on the bearing's operational status, predicting failures before they occur and optimizing maintenance schedules, thereby increasing efficiency and reducing downtime.
The sustainable aspect of plastic bearing housings is another dimension that resonates with contemporary environmental goals. Many manufacturers have adopted eco-friendly practices, utilizing recycled materials in production and implementing processes that reduce energy consumption. This shift not only aligns with global sustainability efforts but also appeals to environmentally conscious consumers.
In conclusion, the adoption of plastic bearing housings offers numerous advantages that cater to the evolving demands of modern industries. Their corrosion resistance, lightweight nature, and cost-effectiveness make them an attractive choice across various applications. Selecting the appropriate material and rigorous testing ensures their performance and reliability, while advancements in smart technology integration and sustainable practices bolster their appeal. As expertise in this field continues to expand, plastic bearing housings stand at the forefront of innovation, driving efficiency and sustainability in industrial design.