Plastic bearing housings are an innovative alternative in the realm of industrial applications, offering a blend of flexibility, durability, and cost-effectiveness that traditional metal housings often struggle to match. As industries evolve, the demand for advanced materials that combine performance with sustainability has never been greater. This makes plastic bearing housings a practical solution that is reshaping the dynamics of mechanical engineering.
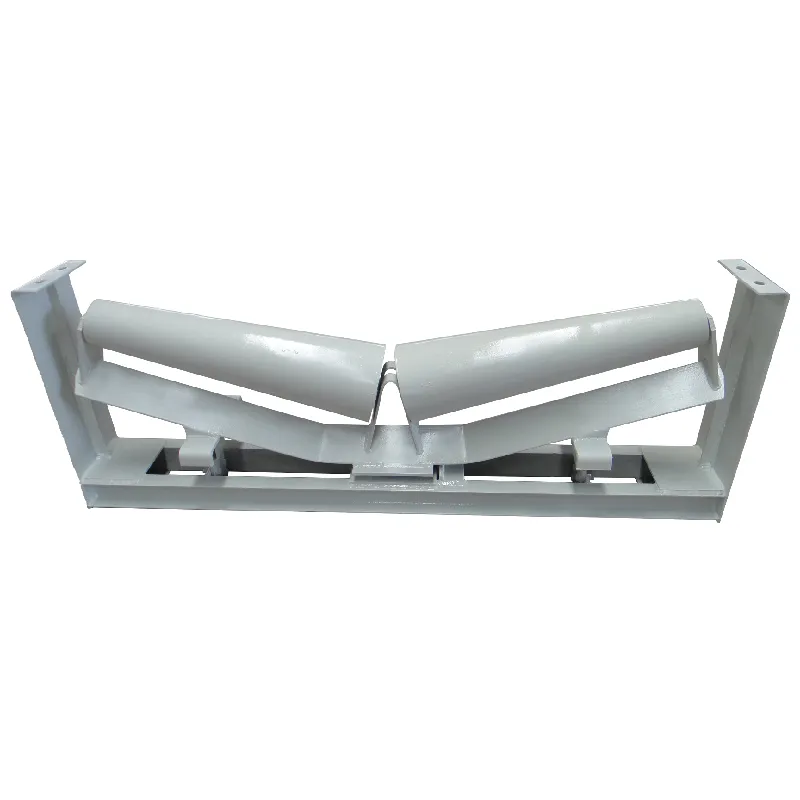
Through years of real-world application, plastic bearing housings have demonstrated their capability to withstand harsh environments without compromising efficiency. Industries such as automotive, food processing, and chemical manufacturing are increasingly trusting these components for their non-corrosive nature, essential in settings where exposure to moisture, chemicals, or extreme temperatures is inevitable.
The expertise behind plastic bearing housing design lies in the engineering of polymers that offer high tensile strength and excellent wear resistance. Materials such as polyethylene (PE), polyoxymethylene (POM), and polytetrafluoroethylene (PTFE) are commonly used. These plastics are lightweight and feature natural lubricity, which significantly reduces the friction between moving parts, resulting in reduced wear and tear. The reduction in friction not only prolongs the life of the moving components but also minimizes energy consumption, offering a green solution to modern industry demands.
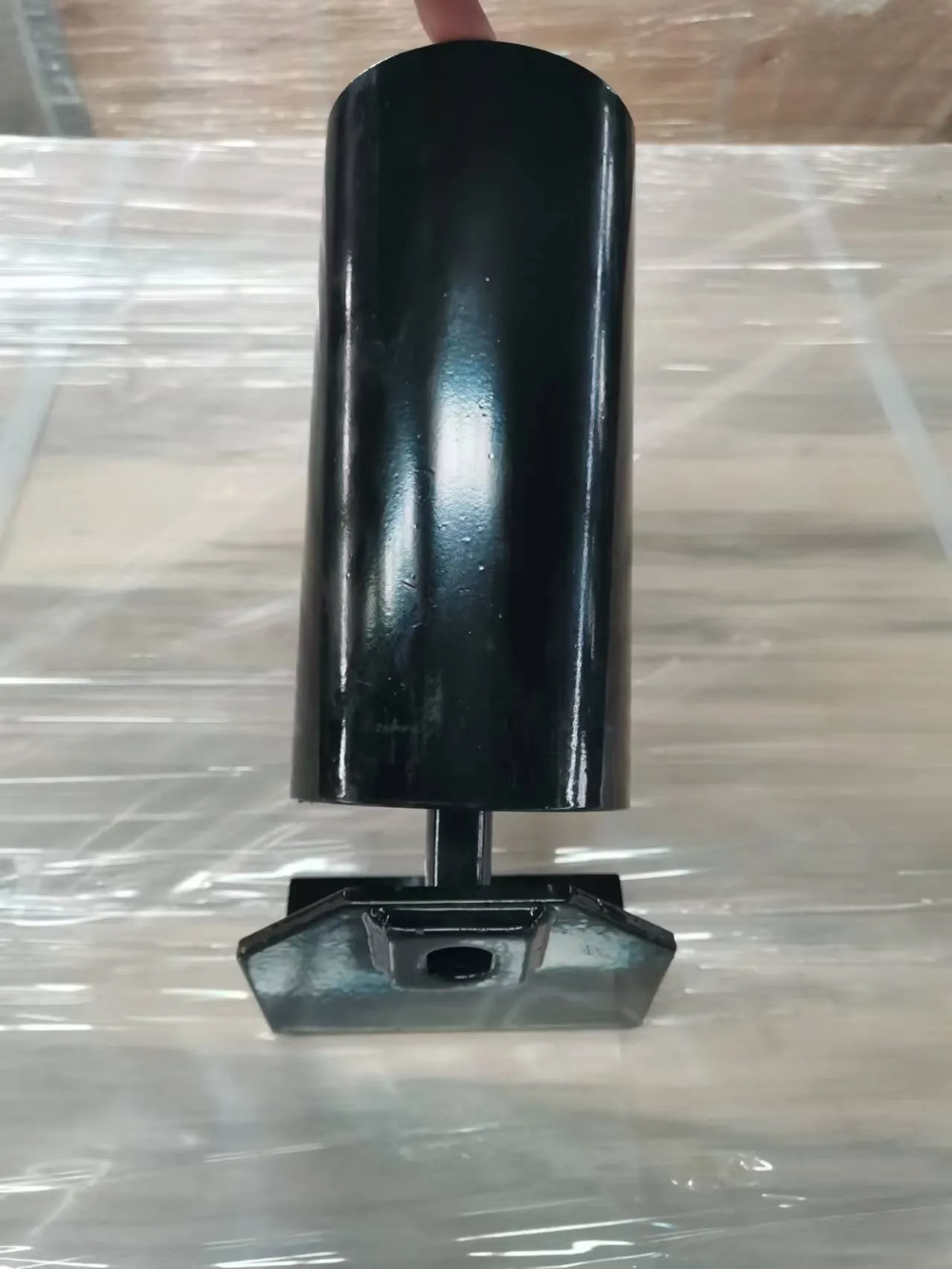
From an authoritative perspective, plastic bearing housings are supported by extensive research and development, backed by industry leaders and academic institutions that test these materials under strenuous operating conditions. These endorsements not only highlight the reliability of plastic bearing housings but also enhance their credibility in the eyes of potential users. Regulatory certifications and compliance with international quality standards further attest to their suitability for use in critical and sensitive applications.
plastic bearing housing
Trust in plastic bearing housings is built through performance validation and a track record of success across various sectors. Feedback from seasoned engineers and operators underscores the practicality of these components in extending the life of machinery and reducing maintenance costs. The inherent self-lubricating properties of selected plastics eliminate the need for additional lubrication systems, thus lowering the risk of contamination—an invaluable feature in the food and beverage industry.
Moreover, plastic bearing housings are customizable, allowing for tailored solutions that meet specific operational requirements. Advanced manufacturing techniques, such as injection molding and 3D printing, enable the production of complex geometries that can be seamlessly integrated into existing systems, providing versatility that metal alternatives lack.
The economic benefits are evident as well.
Plastic bearing housings often represent a lower initial purchase cost compared to metal options. Additionally, the reduction in maintenance expenses and increased operational longevity contribute to a lower total cost of ownership. This economic efficiency, paired with their sustainable advantages, makes plastic bearing housings an attractive proposition for businesses seeking to improve their bottom line while adhering to environmental best practices.
In an era where sustainability and efficiency are paramount, plastic bearing housings offer an advanced solution that meets these dual objectives. Their development and implementation reflect a deep understanding of modern industrial requirements, showcasing a melding of material science advances with practical engineering applications. As industries continue to explore ways to enhance productivity while minimizing environmental impact, plastic bearing housings stand out as a choice that aligns with these goals through proven performance, expert design, authoritative endorsements, and a robust trust network established by satisfied users worldwide.