Non-drive pulleys, although often overshadowed by their more frequently discussed counterparts—the drive pulleys—play an indispensable role in numerous industrial applications. Their unique function of redirecting force without actively transmitting power underscores their importance.
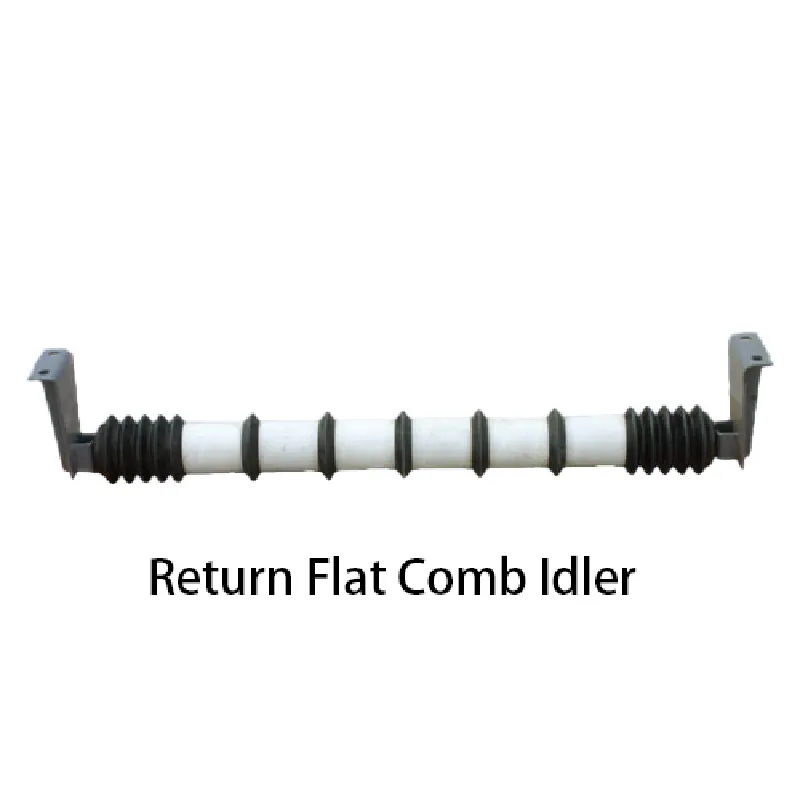
In the realm of conveyor systems, non-drive pulleys are elemental. Conveyor belts circulate raw materials, components, and finished products using a combination of drive and non-drive pulleys. A non-drive pulley, also known as an idler pulley, primarily guides the belt, ensuring it follows the designated path smoothly and with minimal friction. This aspect is pivotal in maintaining operational efficiency by significantly reducing wear and tear on the belt, consequently prolonging its lifespan. Industries ranging from mining to food processing rely heavily on these components for seamless logistics operations.
The choice of materials in non-drive pulleys is crucial. Metals such as steel and aluminum are common, given their robust mechanical properties and resistance to environmental conditions. However, advances in polymer technology have ushered in a new era where non-metal materials are gaining prominence. Polymers like nylon and Teflon provide lightweight yet durable alternatives that are highly resistant to corrosion and wear. These properties are especially appealing in industries where exposure to chemicals or extreme temperatures is frequent. Leveraging such materials not only enhances the longevity of the pulley but also reduces overall system weight, contributing to energy efficiency in large-scale operations.
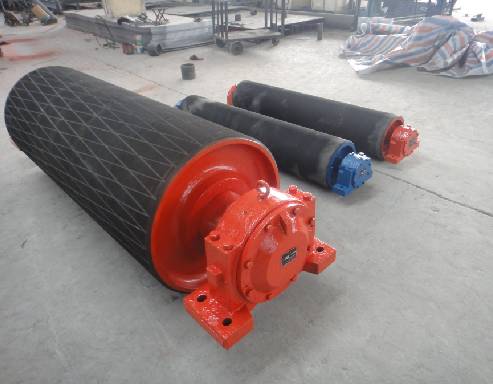
Alignment is another pivotal aspect commonly underestimated. Misalignment can lead to premature failure, inefficient energy use, and costly downtimes. Using laser alignment tools, technicians can ensure optimal pulley placement, ensuring longevity and efficiency. Industries have witnessed marked improvements in system performance through precise alignment practices, leading to a reduction in maintenance costs and an extended lifecycle of conveyor systems.
Lubrication, while often associated with drive pulleys, is equally vital for non-drive versions. The reduction of friction between the belt and pulley surface reduces energy consumption and decreases operational noise. Selecting the right lubricant—often a specialized grease or dry film lubricant—is crucial as it must withstand the operating environments where temperatures and chemical exposures vary widely.
non drive pulley
Given their critical yet understated role, understanding the nuances of non-drive pulley maintenance is essential for operational success. Routine inspections should be scheduled to check for signs of wear, alignment issues, and lubrication needs. Employing predictive maintenance strategies, such as condition monitoring tools, enables facilities to anticipate issues before they manifest into more severe problems.
Moreover, the increasing trend toward smart technology in industrial operations has not bypassed the humble pulley. Integration with IoT (Internet of Things) sensors allows real-time monitoring of pulley conditions. This advancement provides data-driven insights, facilitating proactive maintenance decisions that optimize equipment performance and minimize disruptions.
It’s important to note that the expertise required to manage and optimize these components extends across both mechanical engineering and operational management fields. Cooperation between these disciplines ensures that non-drive pulleys are not only appropriately selected and installed but are continuously monitored and maintained for peak performance. Such a holistic approach ultimately drives down costs and enhances system reliability.
The value of non-drive pulleys extends far beyond their apparent simplicity, providing critical support in systems where efficiency and reliability are paramount. Industry professionals must maintain an informed approach, staying abreast of advancements in materials and technology to fully leverage the advantages they offer. Their silent service within the operational systems underscores a fundamental truth often, the unseen components hold the wheels of industry in motion.