In the realm of material handling and mechanical systems, the significance of the non-drive pulley often goes unsung, overshadowed by its more active cousin, the drive pulley. Yet, for those with experience in engineering and equipment maintenance, the role of the non-drive pulley is clear a crucial component in ensuring optimal system performance and longevity.
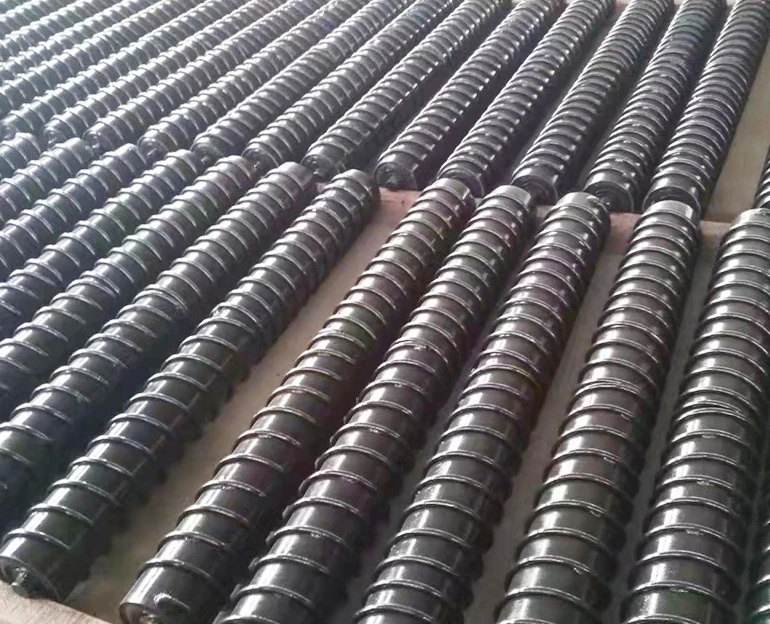
Non-drive pulleys, sometimes referred to as idler pulleys, are primarily used to guide and support the movement of the belt or cable in a system, maintaining tension and alignment. This seemingly passive component can have a profound impact on the functionality and efficiency of the machinery in which it's installed.
Expertise in selecting and maintaining non-drive pulleys can prevent myriad issues that could lead to system failure. For professionals sourcing these pulleys, understanding the materials, design specifications, and the intended operational environment is essential. The choice of material—be it steel, aluminum, or even high-strength plastics—can influence the durability and load capacity of the pulley. Moreover, the operational environment plays a critical role; non-drive pulleys used in high-temperature areas or exposed to corrosive substances must possess resistance properties to withstand such conditions.
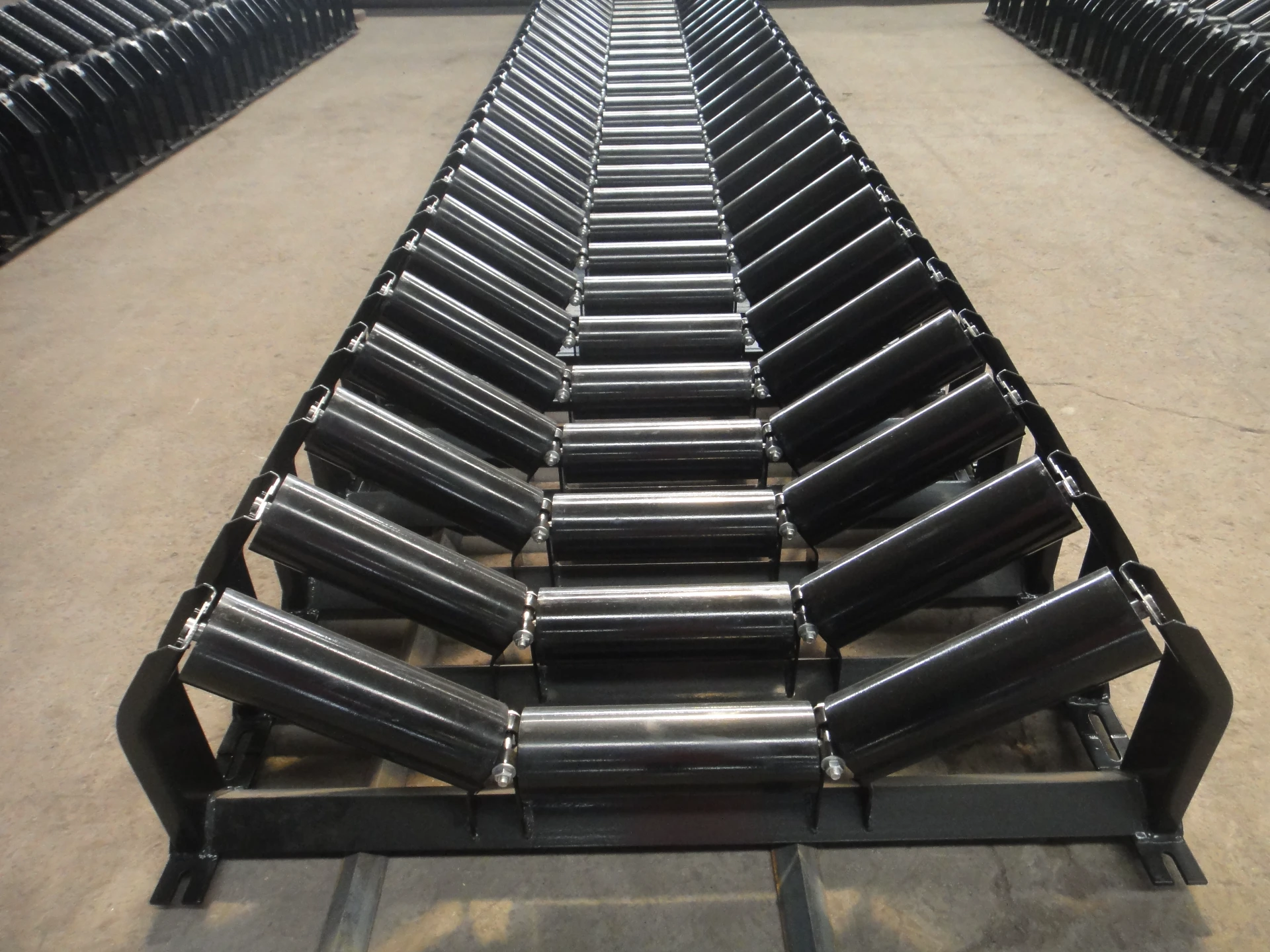
Renowned manufacturers often engineer non-drive pulleys with specific features to enhance their performance. For instance,
bearings within these pulleys minimize friction, thus reducing wear and energy consumption. Additionally, advanced surface treatments can further extend their lifespan by offering greater resistance to wear and corrosion. An authoritative choice in a non-drive pulley can lead to smoother operations, reduced maintenance costs, and an overall increased output of the system.
non-drive pulley
Trustworthiness in product performance for non-drive pulleys often comes down to the meticulous quality checks and rigorous testing protocols adhered to by manufacturers. Companies that maintain stringent quality standards and provide comprehensive warranties are indicators of reliability. Certifications and adherence to international standards can offer assurance regarding the structural integrity and performance consistency of these components.
From the perspective of someone with real-world experience in the field, the implementation of superior non-drive pulleys can translate to tangible benefits on the factory floor or in the field. For instance, in a conveyor system in a manufacturing plant, the consistent tension and alignment offered by a well-maintained non-drive pulley can prevent costly downtimes and prolong the life of the belt, thus safeguarding the overall investment in the machinery.
In conclusion, while non-drive pulleys may not carry the glamour or direct functionality of drive pulleys, their contribution to the efficacy and durability of mechanical systems is indisputable. Ensuring the right selection and maintenance of these pulleys requires a blend of experience, expertise, and trust in authoritative sources. By focusing on these aspects, businesses not only enhance their operational efficiency but also secure their infrastructure from unexpected failures, paving the way for sustained success in their respective industries.