In the realm of material handling and conveyor systems, the idler for conveyor belts plays a crucial, yet often overlooked role. These components are pillars of efficiency and durability, ensuring seamless operations across industries. Companies like CEMA have set the standards for conveyor idlers, providing guidelines that ensure quality and performance. Understanding the functionality, variety, and significance of idlers can enhance not only the efficiency of your conveyor system but also the overall productivity of your operation.
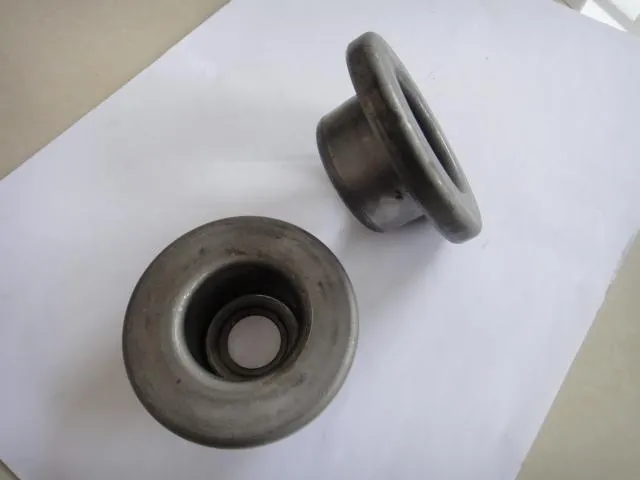
Idlers are essentially cylindrical rollers that support the conveyor belt and its load, helping maintain belt alignment. This function, though seemingly simple, is central to preventing the belt from sagging or deviating, which can lead to system malfunctions or even costly downtimes. The quality of idlers, therefore, significantly impacts the longevity and efficiency of conveyor systems. Manufacturers use a range of materials to construct idlers, including steel, rubber, and high-density polyethylene, each offering distinct advantages depending on specific operational needs and environments.
Choosing the right idlers involves understanding various factors such as load weight, conveyor speed, and environmental conditions. For instance, in high-moisture or corrosive environments, rubber or polyethylene idlers are preferable due to their resistance to corrosion and moisture absorption. On the other hand, steel idlers are ideal for heavy-load operations thanks to their durability and strength. It's imperative to conduct a thorough analysis of your operational demands to select idlers that align with your conveyor's requirements.
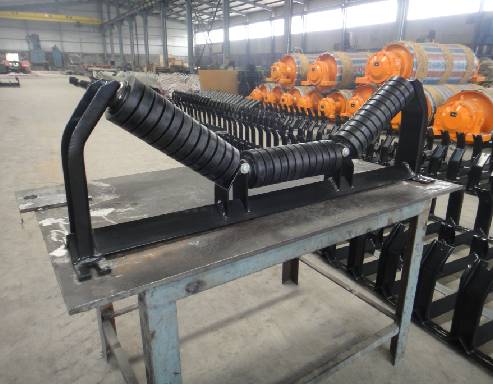
Moreover, different types of idlers cater to specific functions. Carrying idlers support the loaded side of the belt, while return idlers support the unloaded side, preventing it from sagging. Training idlers are vital for maintaining belt alignment and preventing lateral movement. Incorporating impact idlers at loading points can mitigate shock and wear on the belt caused by material loading, thus prolonging the belt's lifespan.
Understanding these variations allows for a more tailored and efficient conveyor system.
idler for conveyor belt
From an engineering perspective, the design and installation of idlers should adhere to recognized standards and best practices, aiming for optimal alignment and spacing. Misaligned or improperly spaced idlers can result in uneven wear and increased stress on the belt, ultimately leading to premature failure. Regular maintenance checks and prompt replacements of worn-out idlers further enhance the reliability and durability of the conveyor system.
Trust in the expertise of reputable manufacturers and suppliers is crucial when selecting idlers. Companies with certifications and a proven track record guarantee that their products meet stringent quality and performance standards. Investing in high-quality idlers is an investment in the longevity and efficiency of your conveyor system, offering savings on maintenance costs and reducing operational downtimes in the long run.
In summary, the idler for conveyor belts is not merely a supporting component but a critical one that ensures the operational efficiency of conveyor systems. By selecting the appropriate type, material, and design, businesses can significantly enhance their material handling operations, increase the lifespan of their conveyors, and maintain smooth, uninterrupted workflow. This strategic approach not only underscores a company's commitment to operational excellence but also reinforces its credibility and authority in the industry. Understanding these elements is essential for anyone looking to optimize their conveyor systems and maximize their return on investment.