Herringbone rubber lagging, a distinguished feature in industrial conveyor systems, remains pivotal in enhancing the efficiency and lifespan of conveyor pulleys. This specialized rubber lagging employs a unique herringbone pattern, often selected for its increased grip and effective water dispersal, crucial in preventing conveyor belt slippage—a common concern in wet or humid environments.
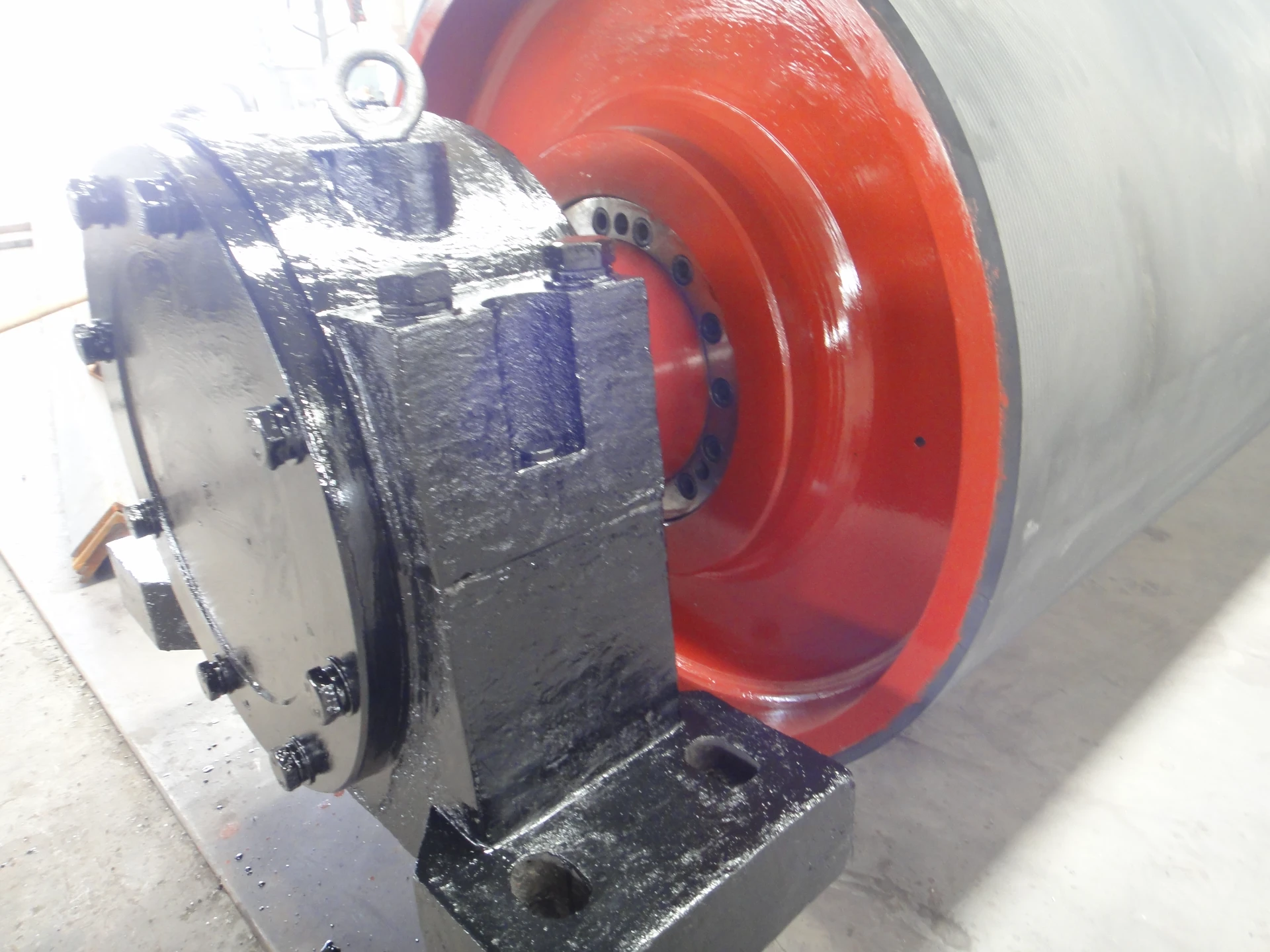
Crafted from highly durable rubber compounds, herringbone rubber lagging showcases superior abrasion resistance. This characteristic is not merely a testament to its robustness but also evidence of its engineering designed to extend operational life without frequent replacements. Withstanding extreme temperatures and harsh contaminants, it offers an extended period of service that ensures a reduction in maintenance costs and downtime—key factors in maintaining uninterrupted industrial operations.
Industry professionals often praise the herringbone design for its exceptional traction properties. The chevron-style groove patterns channel water and debris away from the surface, creating continuous friction between the conveyor belt and the pulley. This enhances conveyor performance,
ensuring smooth movement even under heavy loads or challenging environmental conditions. The operational efficiency gained through reduced belt slippage directly correlates with increased productivity and material handling efficiency.
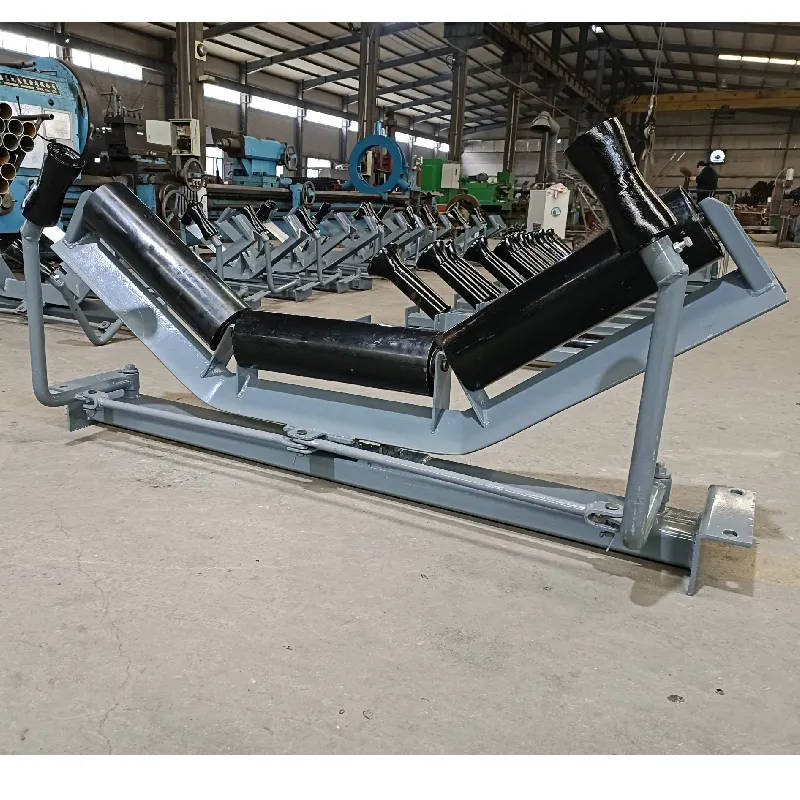
In terms of installation, herringbone rubber lagging is lauded for its adaptability. Whether applied via cold bonding adhesives or mechanical fastening systems, the installation process is streamlined, making it an appealing choice for technicians looking to minimize installation time. This adaptability extends to multiple industrial settings, including mining, aggregate, and bulk material handling industries, highlighting its versatility across sectors.
Choosing the correct type of rubber compound for lagging is a decision stemming from a comprehensive understanding of the specific operational requirements. Preferred compounds are often chloroprene or EPDM, known for their superior performance in resisting oil, chemicals, and UV radiation. Such knowledge reflects not just the expertise needed to source the appropriate materials but also an intrinsic understanding of material interaction within conveyance systems.
herringbone rubber lagging
As experienced voices within the industry would assert, the use of herringbone rubber lagging is a decision weighted on not just immediate operational demands, but also on long-term strategy and investment in operational integrity. The reduced wear on conveyor belts translates to lower replacement costs over time, echoing the principles of sustainable industrial practices. Additionally, consistent performance in reducing slippage minimizes potential safety hazards associated with conveyor operations, further underscoring the safety credentials that align with trusted industry standards.
From an expert’s viewpoint, the strategic use of herringbone rubber lagging reflects a sophisticated understanding of both mechanical dynamics and material science. It embodies the confluence of engineering, maintenance strategy, and performance optimization. The adoption of such materials showcases a commitment to not only achieving high operational standards but also aligns with a broader organizational focus on sustainable, efficient industrial practice.
The credibility of herringbone rubber lagging usage is endorsed by several case studies documenting reduced operational costs and enhanced performance metrics. These studies further validate the expert insight that positions rubber lagging as an indispensable component in optimizing conveyor system efficacy.
Therefore, when seeking solutions that blend efficiency with reliability, herringbone rubber lagging stands out as a preferred choice, embodying both the art and science of industrial material handling solutions. As businesses continue to navigate towards automation and precision in operations, the role of such advanced materials becomes even more crucial, reinforcing the importance of expert consultation and strategic implementation in harnessing their full potential.