Guide rollers, pivotal components in various industrial applications, have garnered significant attention for their roles in enhancing mechanical efficiency and product longevity. These unassuming devices, often overshadowed by the larger machinery they accompany, are crucial for ensuring smooth operation across multiple sectors, from manufacturing to transportation.
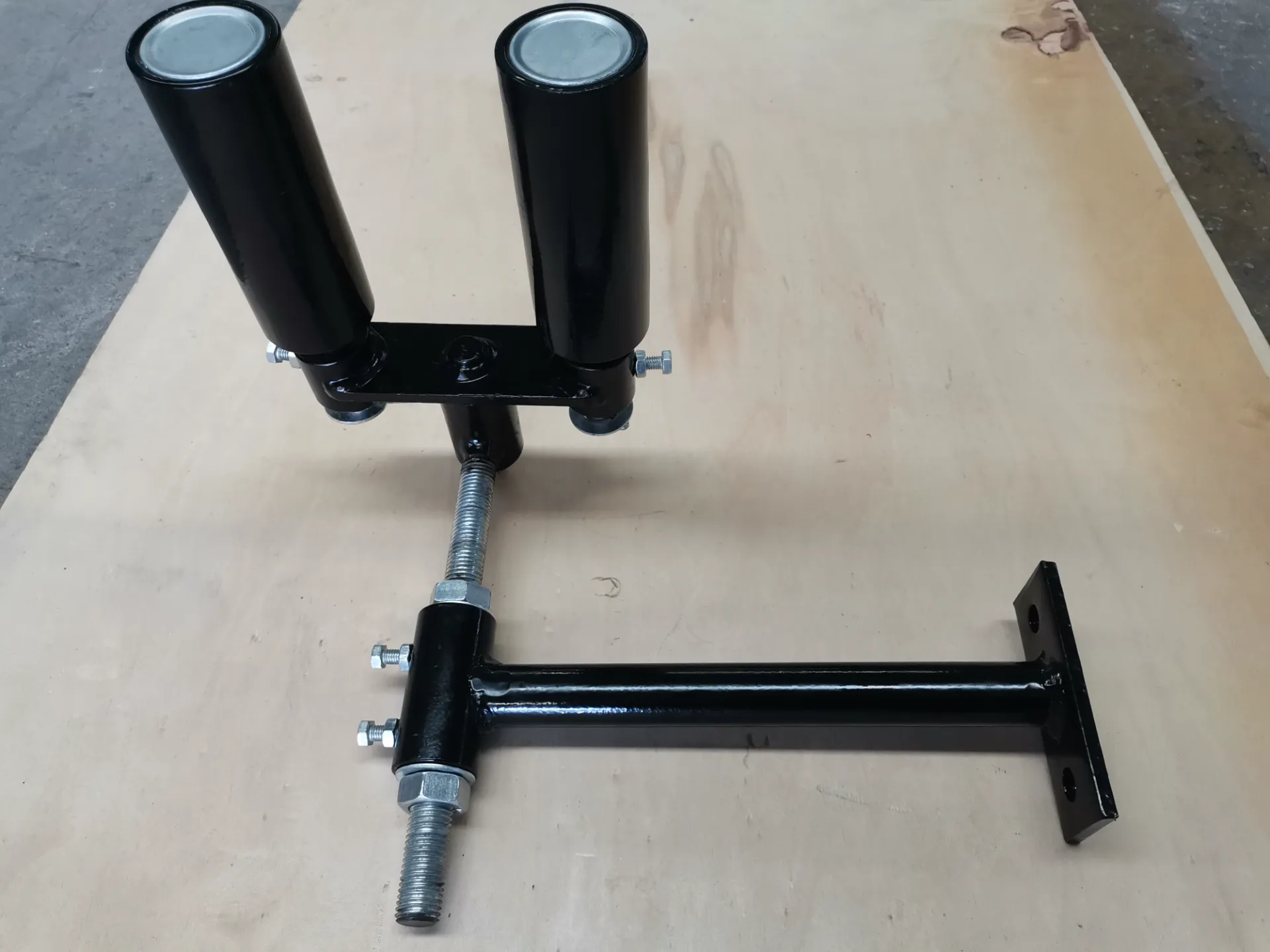
In the realm of production, the guide roller's primary function is to direct and support movement along a designed path. This is especially crucial in conveyor systems where precision and consistency are imperative. A well-placed guide roller can drastically reduce friction, thus minimizing wear and tear on both the roller and the material it interacts with. This not only extends the lifespan of the equipment but also enhances the overall throughput by reducing downtime and maintenance costs.
For those immersed in industries such as automotive manufacturing, the importance of high-quality guide rollers cannot be overstated.
These rollers can make or break the delicate balance required in assembly lines. Imagine a conveyor belt in a car manufacturing plant — each chassis moving down the line must align accurately for the robotic arms to perform their tasks. Here, guide rollers ensure each panel glides seamlessly, avoiding jams and misalignments that could halt production.
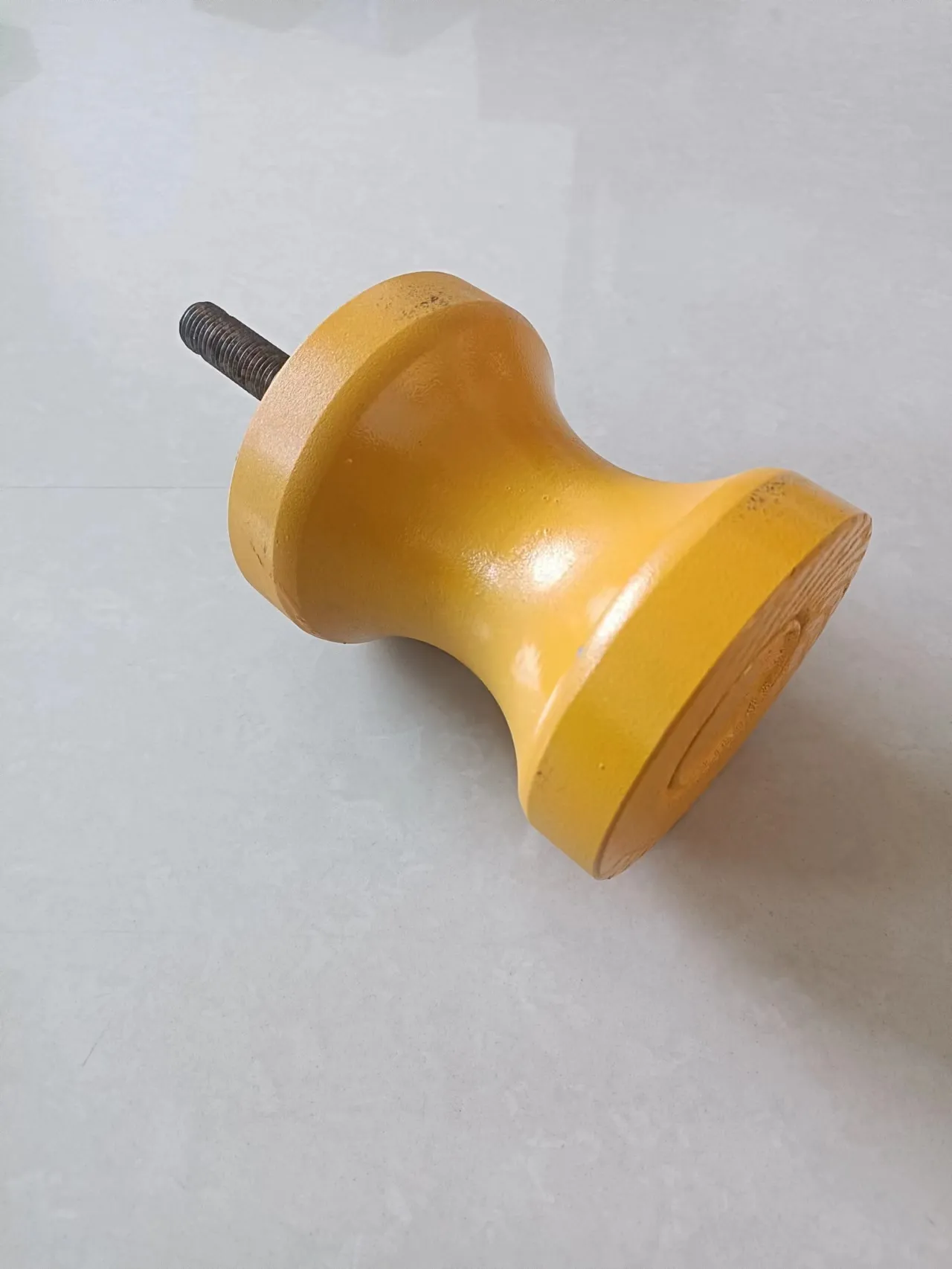
Furthermore, material choice plays a critical role in the efficiency of guide rollers. Materials such as polyurethanes offer unique advantages due to their durability and flexibility. They provide an optimal balance between rigidity and elasticity, allowing for smooth operation even under high load and speed. This choice of material also contributes to noise reduction, a significant factor in user-friendly mechanical operations. Experienced engineers always take into consideration the material properties to tailor guide rollers to their specific needs, ensuring peak performance.
guide roller
From a maintenance perspective, experts advocate for regular inspections and timely replacements of guide rollers to prevent system failures. The potential cost savings from avoiding sudden breakdowns and prolonging machinery life make such practices indispensable. True expertise in machinery maintenance involves not only understanding when to replace these components but also choosing the right specifications and materials for replacements.
In terms of design innovation, modern advancements have led to the development of self-lubricating guide rollers. These cutting-edge tools minimize the need for manual lubrication, drastically reducing maintenance effort and prolonging the operating life of machinery. This innovation underscores the industry's commitment to improving efficiency and reliability, illustrating a clear understanding of the complex challenges faced by contemporary businesses.
Highlighting the authoritativeness of guide rollers, their implementation is backed by rigorous testing and product certifications that comply with international standards. The assurance these certifications provide is invaluable, offering peace of mind to those who rely on these components to uphold the integrity of their operations. From ISO compliance to material safety data sheets, the documentation associated with guide rollers affirms their role as a trusted solution in evolved industrial landscapes.
In conclusion, as industries continue to demand higher operational efficiencies, the role of the guide roller becomes increasingly critical. Its contribution to the seamless function of machines is noteworthy, yet often under-recognized. By investing in high-quality, durable, and innovative guide rollers, businesses stand to benefit from enhanced productivity, reduced costs, and elevated trust in their operational systems. Expertise in selecting and maintaining the right guide rollers is not merely a side consideration but a pivotal component in the pursuit of industrial excellence.