Drum lagging is an essential component in the optimal performance and longevity of conveyor systems, and understanding its application and benefits can greatly enhance operational efficiency. This article delves into the intricacies of drum lagging, providing a rich blend of insights and practical advice drawn from years of expertise, aimed at users seeking to maximize their system's potential.
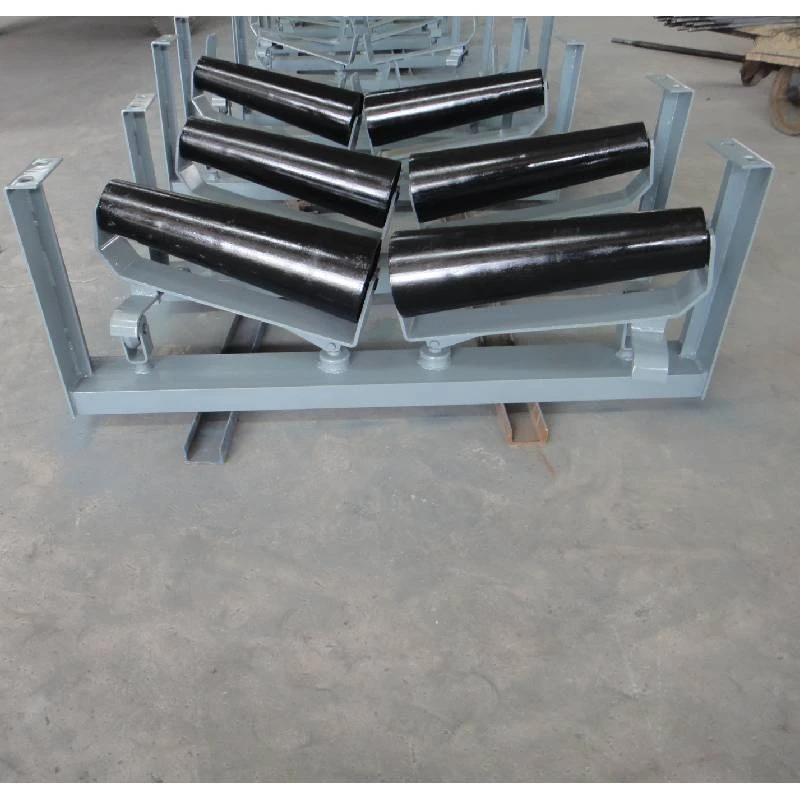
Drum lagging refers to the protective covering applied to conveyor pulleys, an integral aspect of conveyor systems widely utilized across various industries, including mining, manufacturing, and logistics. The primary purpose of drum lagging is to enhance the friction between the belt and the pulley, thereby preventing slippage and ensuring smooth and reliable operation. This protective layer is typically made from a variety of materials, each offering unique benefits and tailored to specific operational needs.
One of the most common materials used for drum lagging is rubber, a versatile choice valued for its balance between durability and cost-effectiveness.
Rubber lagging is particularly suitable for environments where abrasion resistance is crucial. In more specialized settings, ceramic lagging is preferred, especially when dealing with high-tension and aggressive applications. Ceramic lagging boasts superior gripping capabilities and resistance to wear, effectively extending the service life of conveyors and reducing maintenance costs and downtime.
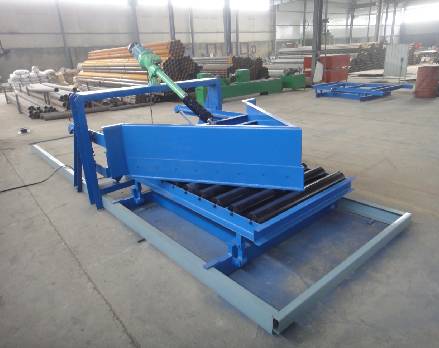
The selection of the appropriate lagging material is a critical decision, influenced by several factors such as operating temperature, environmental conditions, and load requirements. For instance, in environments where heat resistance is a priority, vulcanized rubber or silicone lagging might be preferable. Conversely, in moisture-prone or outdoor settings, a corrosion-resistant material like urethane or ceramic might offer substantial operational advantages.
Beyond material selection, the pattern of the lagging surface also plays a pivotal role in enhancing conveyor efficiency. Classic patterns include diamond, herringbone, and strip, each designed to improve traction and facilitate water shedding. The right pattern choice can significantly impact the performance of a conveyor system, affecting both its efficiency and reliability.
drum lagging
Implementing effective drum lagging requires technical expertise, both in terms of installation and maintenance. Precise alignment and secure attachment are crucial to prevent early failure and ensure consistent performance. For companies lacking internal expertise, partnering with a trusted supplier or service provider can be beneficial. These partnerships not only ensure proper installation but also offer insights into newer technologies and materials that can further enhance system efficiency.
Proactive maintenance of drum lagging is equally important in sustaining conveyor system performance. Regular inspections to monitor wear and tear allow for timely replacement and prevent operational disruptions. Adopting a proactive approach to maintenance, which includes scheduled checks and timely interventions, minimizes unexpected downtimes and fosters a longer lifespan for both the lagging and the conveyor system as a whole.
In terms of authority and trustworthiness, selecting a reputable provider for drum lagging is paramount. Reputable vendors offer guaranteed product quality, backed by extensive industry experience and compliance with international standards. Checking for customer reviews, testimonials, and industry certifications can help in assessing a provider’s credibility and the reliability of their products.
For those looking to optimize their conveyor systems, investing in quality drum lagging represents a critical step. By prioritizing the selection of appropriate materials and patterns, ensuring expert installation, and maintaining a steadfast maintenance routine, companies can significantly enhance conveyor efficiency and reliability. As operations expand and evolve, staying informed about the latest advancements in drum lagging technologies is essential, enabling businesses to adapt and thrive in a competitive marketplace.
In conclusion, drum lagging is not merely an accessory but a fundamental component that can drive operational success. Its role in reducing slippage and protecting conveyor elements is invaluable, contributing to a smoother workflow and enhanced productivity. By understanding the complexities and benefits of drum lagging, businesses can harness its full potential, achieving sustainable growth and operational excellence in their respective fields.