In the diverse world of industrial applications, one crucial yet often overlooked component is drum lagging. This essential product plays a pivotal role in ensuring the efficient and smooth operation of conveyor systems. As a leading authority on industrial processes, we delve into the significance of drum lagging, exploring its benefits, types, and the expert considerations for selection to offer insight and guidance drawn from extensive experience in the field.
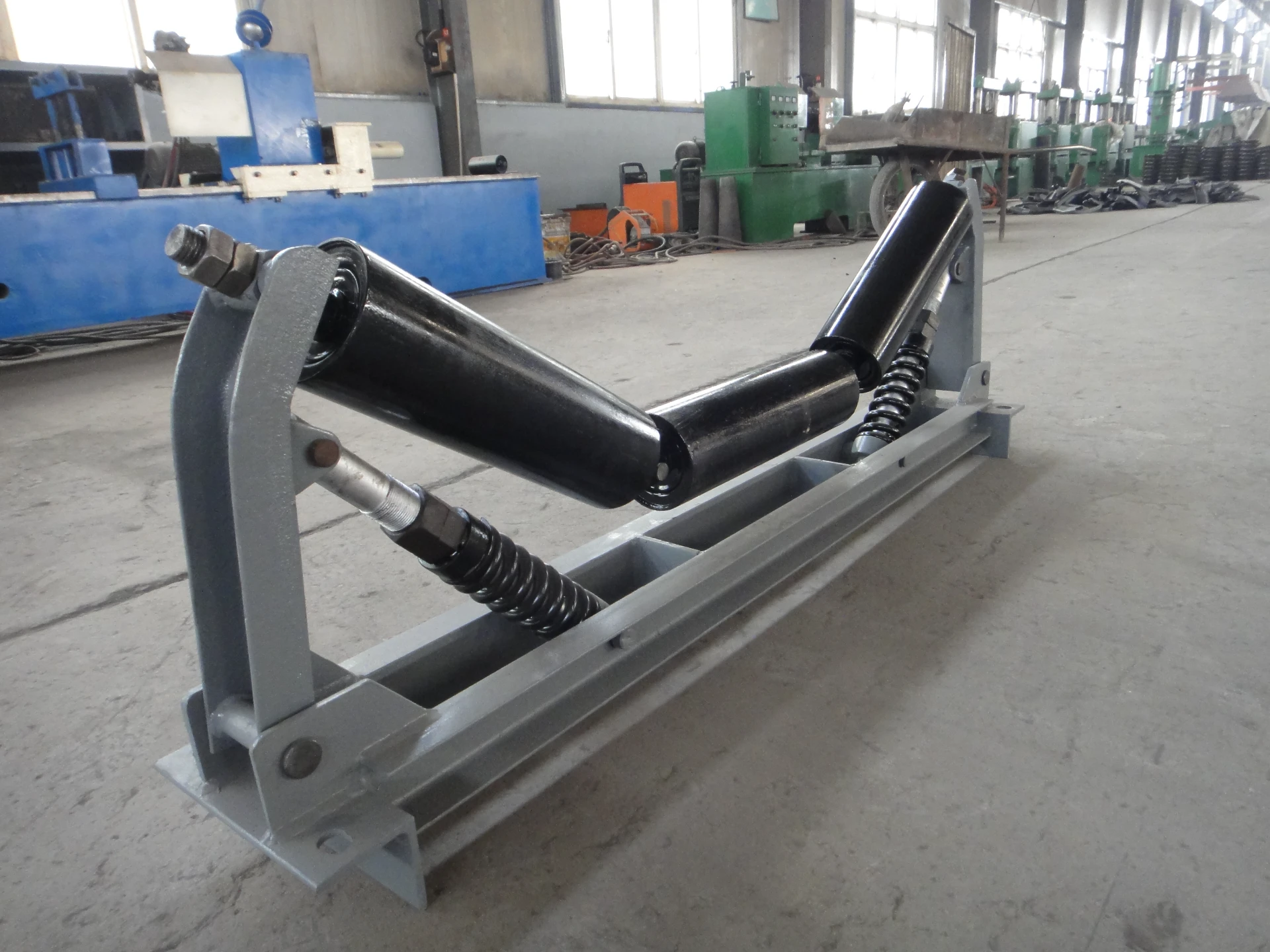
Drum lagging is a process applied to the pulleys of conveyor systems to enhance traction and reduce slippage between the belt and the pulley. Its application signifies a vital upgrade in any belt-driven system, enhancing performance and extending operational lifespan. By offering a friction coefficient that ensures optimal drive performance, drum lagging directly impacts system efficiency and reliability—two keywords every industrial operator strives for.
Industrially, the importance of expertise in the application of drum lagging cannot be overstated.
An optimized pulley system reduces wear and tear, leading to higher efficiency and lower maintenance costs. Various materials are used for lagging, including natural rubber, ceramic, and polyurethane, each offering distinct advantages tailored to specific environments. For instance, natural rubber provides excellent elasticity and shock absorption, making it suitable for general-purpose applications. In contrast, ceramic drum lagging is preferred in highly abrasive environments due to its robust durability and enhanced gripping features.
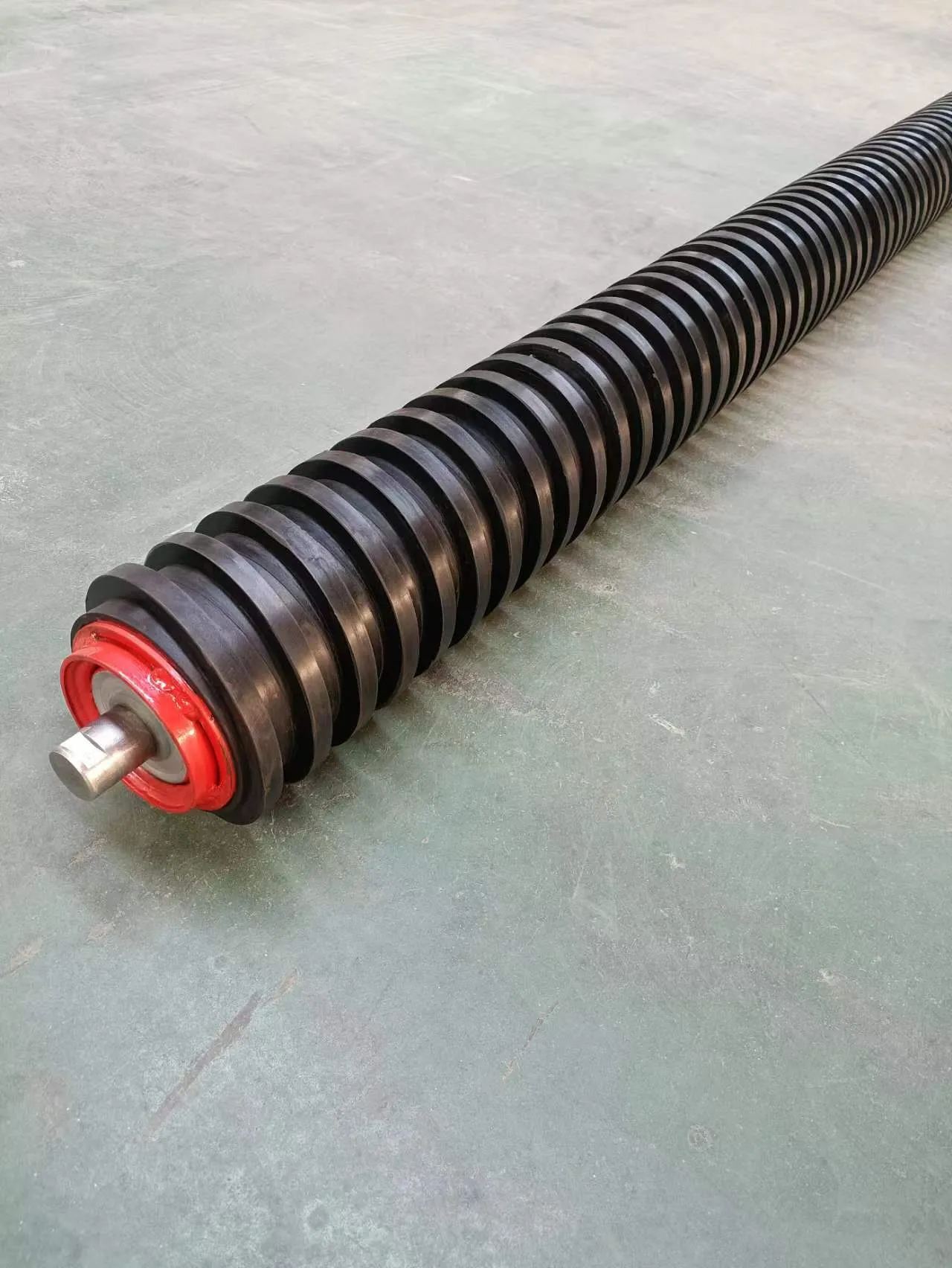
Selecting the appropriate type of lagging material necessitates an authoritative understanding of your operational environment and requirements. It's essential to consider factors such as belt tension, load carrying capacity, and environmental conditions. A thorough analysis ensures the right fit, effectively minimizing downtime and enhancing overall operational trustworthiness.
drum lagging
Furthermore, experience dictates that the method of lagging application—cold bonding or vulcanization—substantially influences performance outcomes. Cold bonding is a versatile and economical method suitable for most applications, while vulcanization, involving heat and pressure, provides a seamless bond, offering superior performance in demanding environments. Engaging with professionals who bring experience and technical proficiency to the table is crucial, as the nuances of installation can significantly affect longevity and efficiency.
In achieving expertise, understanding the interplay between drum lagging and conveyor belt performance illuminates how best to harness this technology for optimal outcomes. Given that improperly lagged drums can lead to costly operational issues, maintaining robust inspection and maintenance practices becomes indispensable. Ensuring regular checks are performed can preemptively identify issues such as wear, misalignment, or lagging detachment, thereby upholding the consistent performance of conveyor systems.
Harnessing this powerful tool also involves trusting reliable providers. Building trustworthiness in service providers becomes imperative—they should offer not only products of high quality but also comprehensive support and guidance, reinforcing your operations with top-tier solutions backed by their authoritative expertise.
In summation, while drum lagging might appear a minor detail in the grand scheme of industrial operations, it holds substantial sway over the efficiency and longevity of conveyor systems. Embedding expert insight into its selection and maintenance not only enhances machine efficiency and cost-effectiveness but underscores a commitment to maintaining elevated standards of operational excellence.