Drive pulleys and driven pulleys are pivotal components in the realm of mechanical engineering and industrial machinery. These elements are not mere components; they are the powerhouses that seamlessly transfer motion and force. Understanding the intricacies of their operation, design, and application not only amplifies machinery efficiency but also significantly enhances the longevity of the systems they form a part of. This comprehensive exploration delves into their roles, technical specificities, and the unparalleled benefits they bring to industrial operations.
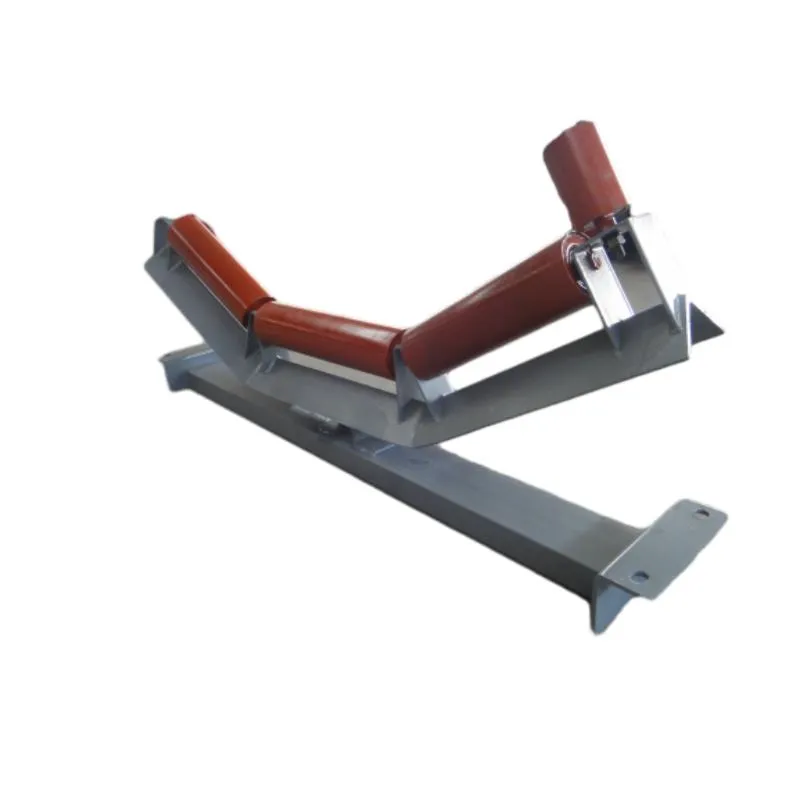
In any mechanical transmission system,
drive pulleys and driven pulleys work in harmony. The drive pulley, connected to a power source, initiates motion—translating rotational energy into linear movement in systems like conveyor belts. Its counterpart, the driven pulley, is on the receiving end of this energy transfer. This interchange is the essence of power transmission; it transforms generated energy into useful work in machinery.
Material selection for these pulleys is more than just a choice—it's a science. Drive pulleys need materials that withstand the rigors of high-speed operations and resist wear and tear, such as steel or ductile iron. Conversely, driven pulleys might utilize lighter materials like plastics or composites, especially when weight reduction is critical. This careful pairing ensures that the system operates optimally under varied loads and operational conditions.
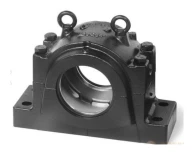
Precision engineering is paramount in the manufacture of these components. A drive pulley’s efficiency heavily relies on its alignment and machining precision. Deviations can lead to misalignment, increased friction, and eventually, premature equipment failure. Using Computer Numerical Control (CNC) technology is a common practice, providing the accuracy required to mill pulleys to exact specifications—delivering perfectly balanced systems that minimize downtime and maintenance costs.
drive pulley and driven pulley
One cannot overlook the importance of surface treatment and coatings for these pulleys. Treatments like anodizing or powder coating can extend the lifespan of pulleys by providing corrosion resistance, thus maintaining their performance even in harsh environments. Additionally, incorporating grooves or teeth into their design can enhance grip and traction on the belt or cable, ensuring that energy transmission remains efficient and effective.
In terms of maintenance, routine assessments are crucial. Wear and tear, though inevitable, can be meticulously tracked with regular inspections and predictive maintenance practices. For drive pulley systems, maintaining the integrity of the belt that connects them is essential. Regular tension adjustments, alignment checks, and replacement of worn belts can prevent unexpected breakdowns and help maintain continuous operation.
The real-life applications of drive and driven pulleys are extensive, with usage spanning from mundane conveyor belts in warehouses to advanced aerospace applications. Their versatility and reliability make them indispensable in industries such as automotive manufacturing, packaging, and material handling. In each instance, the pulleys' ability to subtly adjust and align ensures that mechanical systems operate flawlessly, meeting the demands of modern industrial processes.
In conclusion, drive pulleys and driven pulleys are not mere mechanical components; they are the cornerstone of efficient industrial operations. Their design, material composition, and maintenance serve as testament to their importance in ensuring mechanical systems' reliability and efficiency. For anyone invested in the field of mechanical engineering or industrial maintenance, understanding the dynamics of these critical components is not just beneficial—it is essential. Their profound influence on operational efficiency and system functionality makes them pivotal in the quest for heightened industrial productivity and reliability.