The intricate world of pulleys, specifically the driven pulley and driver pulley, plays a pivotal role in the machinery industry. To gain a comprehensive understanding of these components, one must delve into their functions, applications, and the benefits they bring to the mechanisms they are part of.
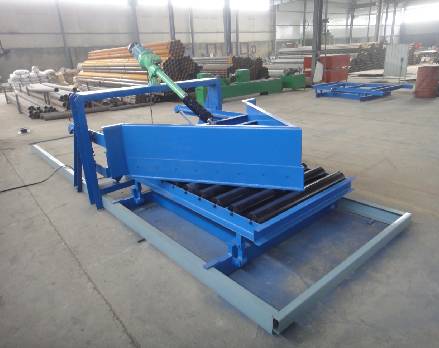
In any pulley system, the driver pulley is the initiating force within the mechanism. It is connected directly to the power source, such as a motor or an engine, and begins the transmission of energy. The primary role of the driver pulley is to propel the entire system, thereby setting the operational pace and efficiency of the machinery. By converting energy from the power source into movement, it sets the entire mechanical chain in motion.
On the other hand, the driven pulley works as the recipient of force. It is attached to the component that needs to be operated or moved. The key function of the driven pulley is to receive motion from the driver pulley through a medium—often a belt, chain, or rope—and subsequently transfer that motion to the machine part it is driving. This transmission effectively allows for controlling the speed, torque, and direction of the machinery's operations.
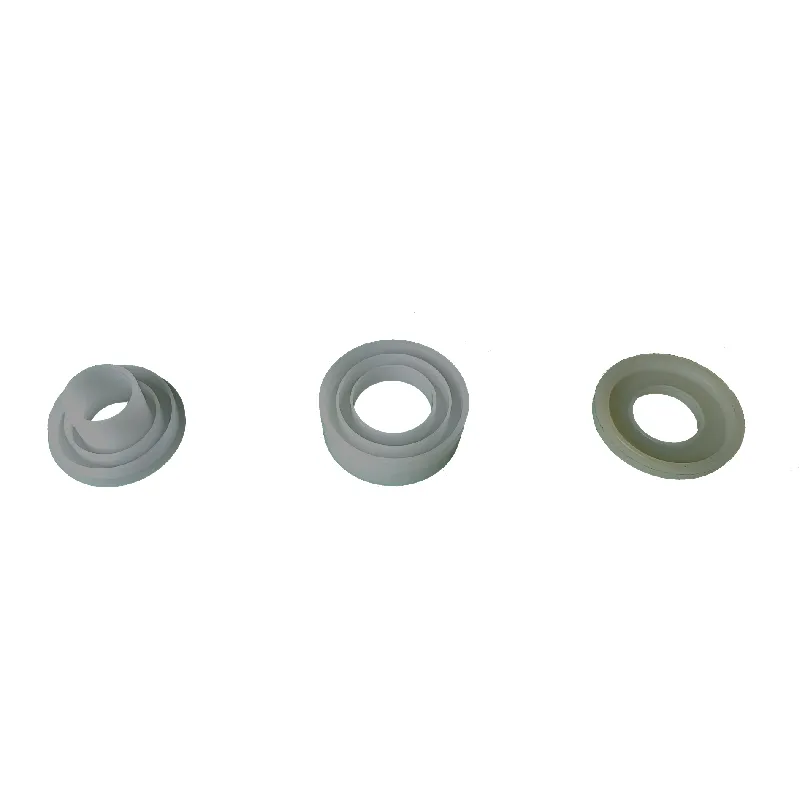
Understanding the synergy between these two pulleys is critical. Their collaboration ensures optimal performance in a wide array of applications, from automobiles to industrial machines, and even in basic machinery like bicycles. For instance, in automotive mechanics, the driver pulley often engages the crankshaft, while the driven pulley influences parts like the alternator, water pump, or air conditioning compressor. This system ensures that every component is powered adequately, boosting the vehicle's overall functionality.
In terms of material construction, choosing the right material for both pulleys is of utmost importance for durability and efficiency. Typically, pulleys are crafted from metals like steel or aluminum, noted for their robust nature and resistance to wear. Advanced applications may employ composite materials to reduce weight without compromising on strength, essential for high-speed operations.
driven pulley and driver pulley
Ergonomic design and precise engineering are fundamental in the production of driven and driver pulleys. A slight misalignment or imbalance can lead to excessive wear and tear, noisy operations, and eventually, system failure. Therefore, premium quality manufacturing standards and precision measurements during installation are key for ensuring long-lasting performance and reliability.
Moreover, the choice of belt or chain connecting the driver and driven pulley significantly impacts the system's effectiveness. Different environments and loads may require specific types; for example, a V-belt may be suitable for variable speed applications, while a serpentine belt could be more effective for systems needing continuous torque transmission. Each option offers unique benefits and choosing the correct one depends largely on the specific needs of the machinery.
Maintenance is another critical aspect that ensures the longevity of these components. Regular inspections to check for wear, alignment, and tension are necessary preventive measures. By catching minor issues early, companies can avoid costly downtime and extensive repairs, which leads to better productivity and operational efficiency.
In sum, the integration of driven and driver pulleys into machinery systems ceaselessly demonstrates their critical importance in mechanical operations. By appreciating their roles and ensuring high standards in design, material selection, application, and maintenance, industries can leverage these components to drive performance and efficiency. As technology evolves, so too does the sophistication and capability of pulley systems, promising ever-greater contributions to the machinery landscape. Understanding these components through experience and expertise instills the authority and trustworthiness necessary for informed decision-making in industrial applications.