The world of conveyor systems is vast and varied, catering to numerous industries and applications across the globe. At the heart of these systems are conveyor rollers, critical components designed to facilitate smooth and efficient material handling. Exploring the different types of conveyor rollers can greatly enhance your understanding of conveyor systems and their optimal use in various environments.
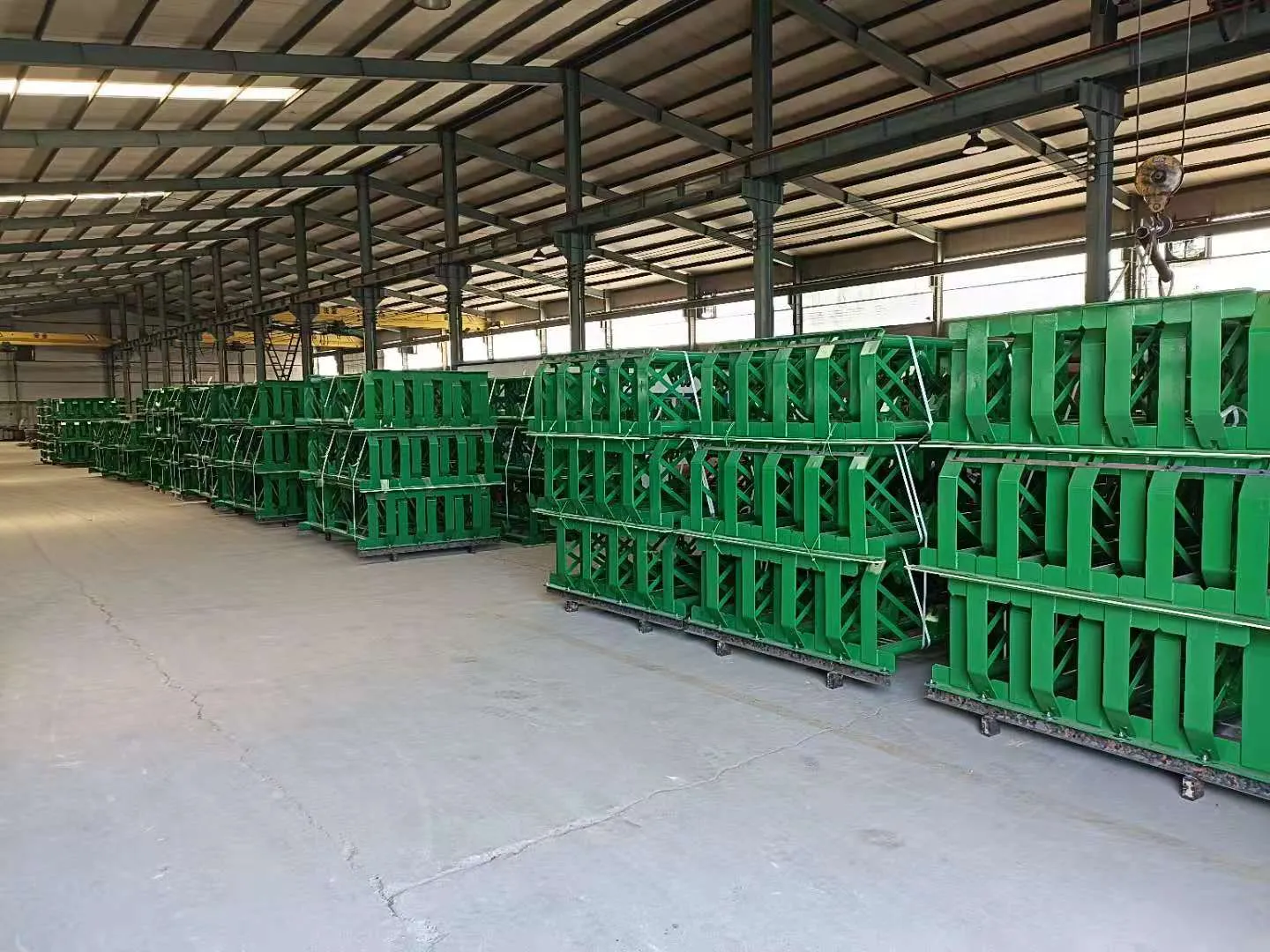
Conveyor rollers are diverse, tailored for specific needs ranging from light-duty applications to heavy-duty material handling. Their primary purpose is to support and transport items along a conveyor belt, while also dictating the speed and direction of materials.
One major type of conveyor roller is the gravity roller. Preferred for its simplicity and efficiency, the gravity roller is unpowered and relies on gravity to move materials along a conveyor pathway. This type of roller is ideal for flat or declining planes and is commonly used in warehouses and shipping areas where manual handling needs minimizing.
Another essential type is the powered roller. Unlike gravity rollers, powered rollers are motor-driven and can move items regardless of the incline or platform design. These rollers are indispensable in automated production lines where speed and precision are crucial. Highlighted by their versatility, powered rollers come in various forms, such as motorized drive rollers and chain-driven rollers, each suited to different industrial needs. For example, motorized drive rollers are compact and energy-efficient, often used in settings requiring high-speed applications, whereas chain-driven rollers are robust, designed for transferring heavy loads through difficult environments.

When considering environments with temperature extremes or high corrosive potential, specialized rollers like stainless steel and plastic conveyor rollers are paramount. Stainless steel rollers offer a corrosion-resistant solution with a high load-bearing capacity, making them suitable for food processing and outdoor environments. Conversely, plastic rollers, being lightweight and resistant to chemicals, work well in applications demanding hygiene and quiet operation, like in pharmaceutical manufacturing or light packaging.
different types of conveyor rollers
Furthermore, industries requiring precision and minimal friction find tapered rollers particularly beneficial. Tapered rollers are designed to help with maintaining the alignment and position of items on a conveyor, preventing slippage or misalignment. Used predominantly in curved conveyor systems, they ensure that materials navigate bends efficiently without significant variation in speed or trajectory.
For sectors focused on sustainability and energy efficiency, energy-saving rollers are an innovative option. Equipped with smart sensing technology, these rollers can automatically adjust speed and torque according to the load requirements, significantly reducing energy consumption and operational costs. These modern rollers reflect the industry's shift towards more sustainable and cost-effective solutions.
Expert opinions from leading conveyor system experts suggest that the choice of conveyor rollers should align closely with specific operational needs and the environmental conditions of your facility. Achieving optimal results requires a nuanced understanding of material specifications, operational demands, and maintenance capabilities. Regular maintenance and proper installation are equally crucial to extend the lifespan of the rollers and ensure seamless operation.
In conclusion, the variety of conveyor rollers available today underscores their importance in modern material handling systems. Each type holds specific advantages tailored to particular industries, load requirements, and operational conditions. As technology advances, the potential for enhanced efficiency and sustainability in conveyor solutions will continue to grow, shaping the future of material transport across all sectors. Understanding and selecting the right conveyor rollers not only maximizes productivity but also fortifies the infrastructure of contemporary industrial operations.