An efficiently functioning conveyor system is the backbone of a productive warehouse or manufacturing setup, dynamically handling everything from lightweight packages to heavy industrial components. Understanding the importance of each part of a conveyor system can elevate your operations by reducing downtime and increasing reliability. This guide delves into the intricacies of conveyor system parts, leveraging industry-leading expertise to enhance your product knowledge and operational trust.
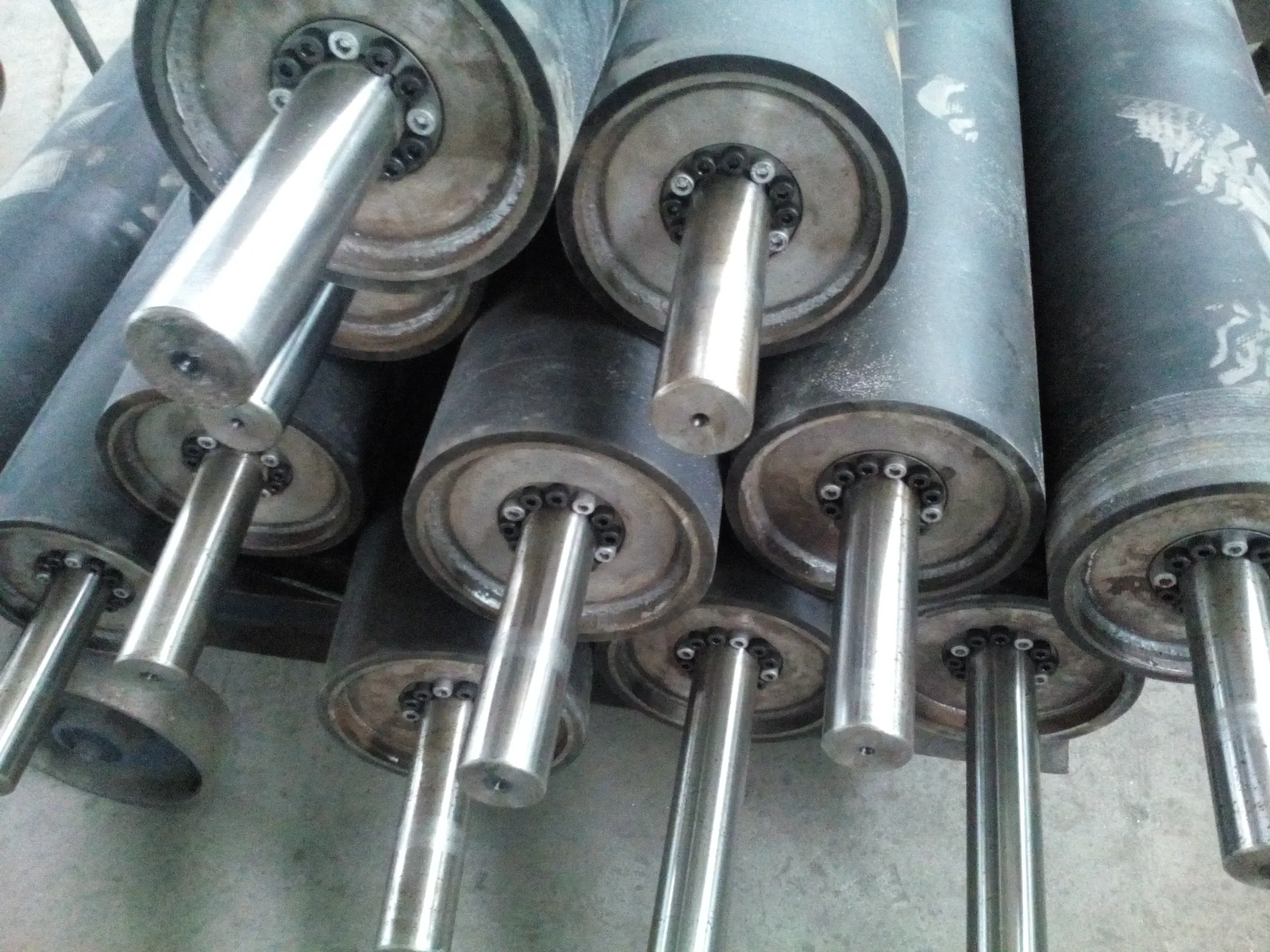
At the core of any conveyor system are the conveyor belts. These belts, often made from rubber, polyester, nylon, or other synthetic materials, are selected based on the specific requirements of the transporting goods. For example, heat-resistant belts are essential in environments exposed to high temperatures. Conducting regular inspections and maintenance checks is vital to identify wear and tear early on, thus extending belt life and maintaining efficiency.
Supporting these belts are idlers, rollers tasked with reducing operational friction and wear. Selecting rollers suited to conveyance speed and load requirements is critical. Steel rollers are preferred for heavy-duty applications, while plastic rollers might be utilized for lighter loads. Enclosed end designs protect the inner mechanisms from dust and moisture, elongating their service life and ensuring consistent performance.
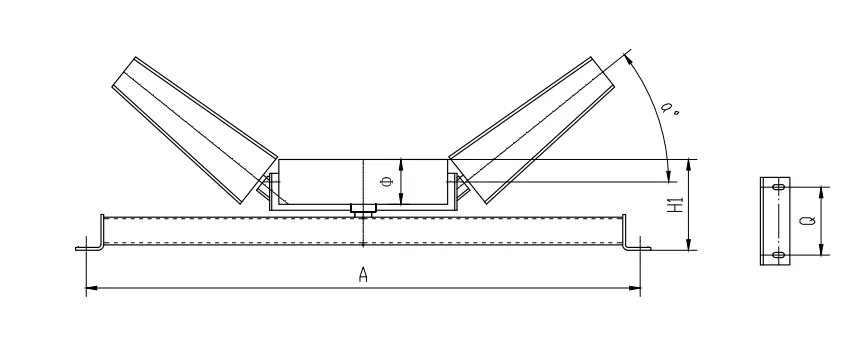
Drives are another essential component; they determine the speed and direction of the belt. Drive pulleys, equipped with motorized hubs, must be regularly monitored to ensure they are not overloaded, which can lead to decreased lifespan or even damage. Proper alignment and tension settings are crucial to optimize their function and prevent operational disruptions. Innovations in variable frequency drives (VFD) allow for precise control of belt speed, adapting to changes in production demands or reducing energy consumption during idle times.
Transfer systems, whether for merging, diverting, or sorting items, must be designed with precision to avoid bottlenecks and ensure smooth transitions between different conveyor zones. These systems can utilize a variety of mechanisms, including pushers, pop-up rollers, and turntables, each suited to different applications. Investing in transfer systems that offer flexibility can greatly enhance the efficiency of your logistics operations.
conveyor system parts
Controls and sensors are indispensable for automation in modern conveyor systems. They ensure the synchronized movement of parts, responding in real-time to changes in the workflow. Sensor technology, such as photoelectric or proximity sensors, detects position and movement, sending signals to controls which can adjust the system's operation accordingly. Having a centralized control system that can monitor and manage all components ensures seamless integration and minimal human intervention, leading to higher productivity and consistent throughput.
Safety mechanisms cannot be overlooked. Guardrails, emergency stops, and protective netting or barriers are essential in preventing accidents. Regular training sessions and safety audits ensure that workers are aware of the safety features and know how to react in case of an emergency. Maintaining compliance with safety regulations not only protects your workforce but enhances your company's reputation for reliability and responsibility.
Incorporating regular maintenance checks and having a clear strategy for parts replacement is crucial for minimizing downtime in case of system failure. Implementing a detailed inventory of spare parts for critical components like belts, rollers, and motors, along with a partnership with trusted suppliers, ensures quick replacement and repairs. Emphasizing predictive maintenance strategies, supported by data analytics, can preemptively signal worn-out parts, allowing for timely interventions before failures occur.
By focusing on these crucial elements of conveyor system parts, businesses can achieve a robust, efficient, and sustainable conveyor operation. It enhances not only the operational workflow but also boosts credibility and trustworthiness within the industry. Leveraging expertise and knowledge in conveyor systems ensures that your operations run seamlessly, supporting your operational goals and delivering exceptional value to your client base.