Conveyor roller mounting brackets might seem like a niche topic, but they play a critical role in the efficient operation of conveyor systems used across various industries. Whether in manufacturing, distribution, or even in food production, the right mounting brackets ensure seamless performance, minimization of downtime, and enhanced safety.
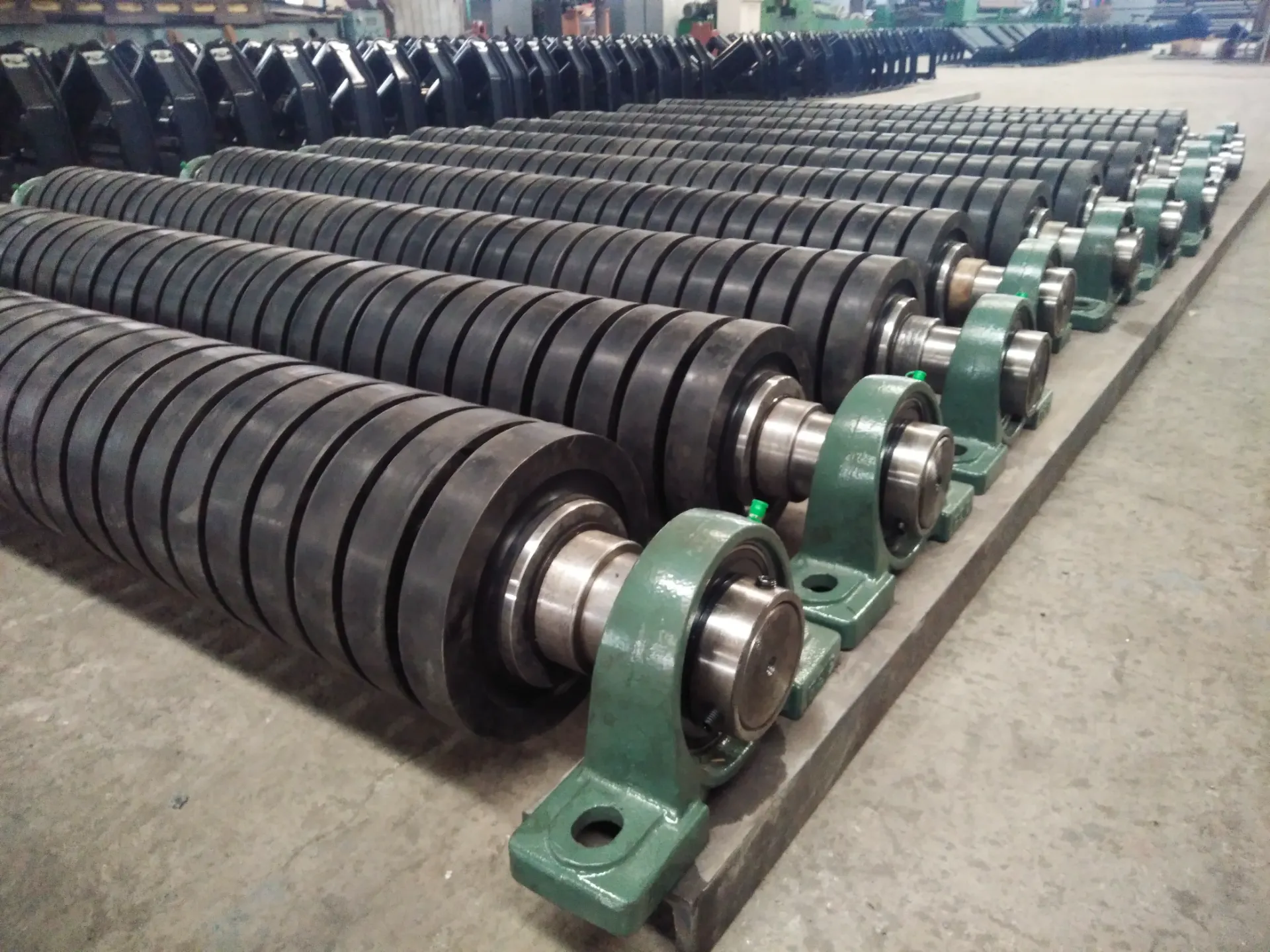
Understanding the variety and application of mounting brackets begins with recognizing their fundamental purpose. These brackets serve as the pivotal connecting piece that holds each roller in place within a conveyor framework. They ensure accurate alignment, consistent spacing, and reliable support for the entire conveyor system. Depending on the load and environment, brackets can be composed of various materials such as steel for heavy-duty applications, or corrosion-resistant materials for more challenging environments.
In industries focusing on mass production, customizability in conveyor systems is paramount. This is where modularity, provided by a broad range of mounting bracket styles, proves indispensable. Brackets need to allow adjustments to cater to different roller sizes and configurations. This flexibility is crucial for industries dealing in products that vary significantly in size and weight during different production cycles. The ease with which these brackets can be adjusted or replaced directly affects production efficiency. Imagine the loss of operational efficiency due to prolonged downtime when adjusting for different production runs — a nightmare for any production manager.
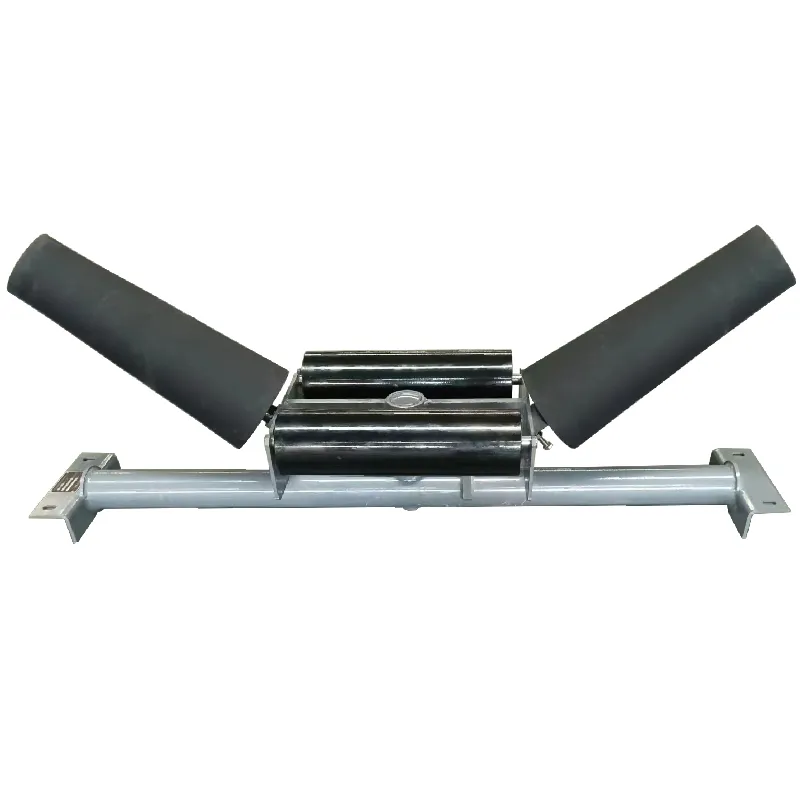
From a technical standpoint, selecting the correct mounting bracket involves understanding the specific requirements of your conveyor system. Variables such as load capacity, environmental conditions, and system longevity need to be considered. For example, a conveyor system in a high moisture environment might require stainless steel brackets with additional sealing to prevent rust and corrosion, effectively extending the system's lifespan.
The skillful integration of conveyor roller mounting brackets also contributes significantly to operational safety. Incorrectly mounted brackets can cause roller misalignment, leading to increased wear and tear on the system and potential safety hazards. An expert approach involves not only selecting the appropriate bracket but also ensuring precise installation using standardized methods and regular maintenance checks. This attention to detail aligns with industry Standards such as those set forth by the Occupational Safety and Health Administration (OSHA) and other regulatory bodies, guaranteeing compliance and maintaining high safety standards.
conveyor roller mounting brackets
Moreover, advancements in technology have ushered in innovative mounting bracket designs that promote energy efficiency. Modern brackets can be designed to incorporate energy-saving components, such as low-resistance bearings, which reduce the energy required to move the conveyor belt. This feature is particularly beneficial in industries with high electricity costs or those striving to meet stricter environmental regulations.
From an authoritative perspective, industry leaders are continuously researching and refining bracket and conveyor system designs to push the boundaries of efficiency and reliability. Companies manufacturing conveyor components are investing in research and development to create products that are not only durable but also sustainable, reflecting a broader commitment to corporate social responsibility. This dedication to innovation is evident in the partnerships between academia and industry, where new materials and design techniques are tested and implemented, leading to cutting-edge solutions.
In today’s competitive environment, trust in your components supplier can make a significant difference. Choosing suppliers with a proven track record and established expertise in conveyor systems ensures that you are acquiring not just a component, but a comprehensive solution backed by years of experience and commitment to quality. Establishing ongoing partnerships with these suppliers allows for constant updates and improvements to your conveyor systems, ensuring that your operations remain ahead of industry standards.
In conclusion,
the humble conveyor roller mounting bracket is more than just a piece of metal in your system. It is a crucial component that supports efficiency, safety, and sustainability in your operations. Its selection and implementation require a nuanced understanding and a strategic approach informed by industry experience and expertise. Trust in experienced suppliers and keep abreast of technological advancements to maintain a cutting-edge conveyor system that meets the rigors of modern production demands.