In the advancing world of material handling and logistics, conveyor systems have become integral to operations requiring efficient transportation of goods. Among the components of these systems, the conveyor roller bracket often assumes an underestimated role. Though inconspicuous, it is crucial for maintaining the stability and functionality of the conveyor systems. As an expert in industrial components with years of hands-on experience, let's delve into why the conveyor roller bracket deserves attention in your next purchase and implementation decision.
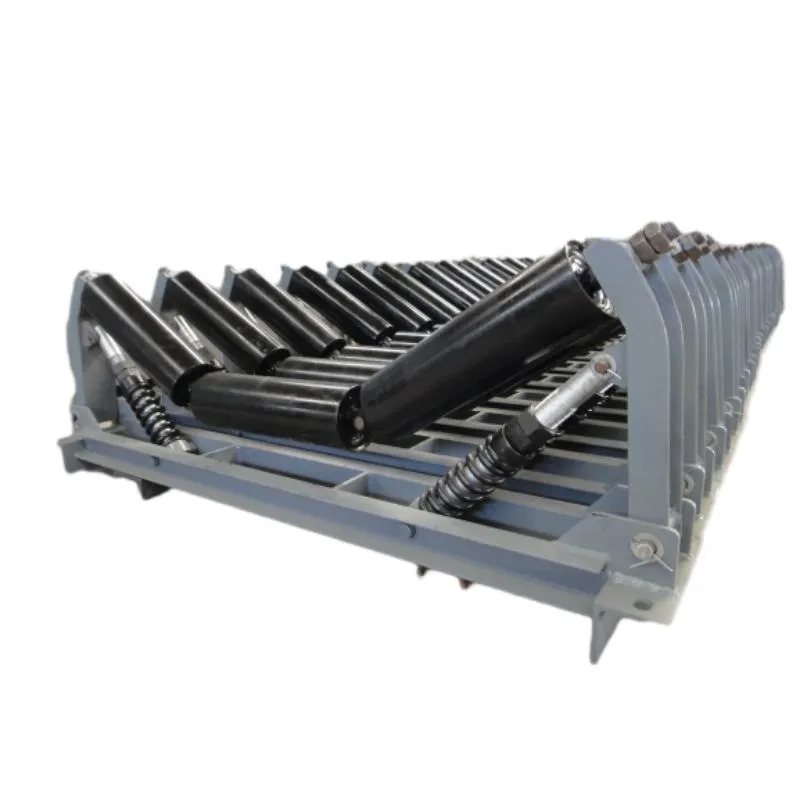
For those involved in process industries, the reliability of conveyor roller brackets directly correlates with the smoothness and longevity of your conveyor systems. While their name might slip under the radar compared to other more prominent conveyor components, such as rollers or belts, the wrong choice of a roller bracket can lead to operational inefficiencies and increased maintenance needs. Selecting the right bracket involves taking a comprehensive look at its material, adaptability, and load-bearing capacity to meet the demands of the specific environment where it will be employed.
Materials matter when choosing a conveyor roller bracket, especially in environments that are corrosive or require sterilization. Common materials include stainless steel, galvanized steel, and thermoplastics, each suitable for different working conditions. Stainless steel brackets are renowned for their durability and corrosion resistance, making them ideal for food processing or chemical industries. Galvanized steel, on the other hand, offers a cost-effective solution for environments where the threat of corrosion is moderate. Thermoplastic brackets, while less traditional, provide a lightweight option that can reduce overall wear on conveyor systems without compromising the structural integrity.
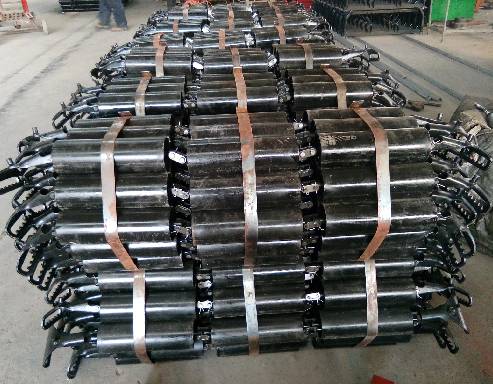
Another crucial factor is the adaptability of the conveyor roller bracket. Standard designs work well for common applications, but custom brackets may be necessary for conveying systems with unique dimensions or operational needs. Companies offering custom fabrication tend to integrate innovative designs tailored to specific operational challenges, offering modular solutions that ease installation and maintenance. The right adaptability enhances not just functionality, but also reduces downtimes, contributing to significant cost savings over time.
Load-bearing capacity cannot be ignored when selecting a suitable conveyor roller bracket.
Accurate assessment of the weight the bracket will bear is imperative. This involves understanding the type of items being transported and their cumulative weight. Underestimating the weight capacity could result in mechanical failures and pose safety risks. Therefore, it is essential to consult load ratings and consider a safety margin, ensuring that the bracket can handle more than the maximum anticipated load.
conveyor roller bracket
A crucial part of ensuring the trustworthiness of your chosen conveyor roller bracket is sourcing them from reputable manufacturers known for stringent quality control standards. Quality certifications, compliance with international standards, and positive customer feedback serve as important indicators of a manufacturer’s reliability. Reputation also plays into the manufacturer's ability to provide ongoing support and warranties, which is indispensable should you encounter any operational issues.
In terms of cost-efficiency, investing in higher-quality roller brackets may appear more expensive upfront, but it guarantees more extended system durability and less frequent maintenance. This is where a thorough cost-benefit analysis can align with budgetary constraints while prioritizing long-term operational efficiency. Vendors who offer consultancy and after-sales service can often provide insights into making the most out of your investment, advising on installation, use, and care routines to maximize efficiency.
As industrial settings continue to evolve with technology integration, some manufacturers are now incorporating smart design features in conveyor roller brackets. These advancements include sensor compatibility for automated systems, allowing for real-time monitoring of the conveyor's operational status. With these innovations, systems become capable of predictive maintenance, reducing unscheduled downtimes and contributing to overall operational resilience.
In conclusion, the conveyor roller bracket, while a small part of the vast world of conveyor components, plays a foundational role in ensuring system stability and efficiency. Choosing the right bracket requires attention to material, adaptability, load capacity, and manufacturer reputation. By understanding these nuances, businesses can enhance their conveyor systems' performance, reduce operating costs, and ensure long-term productivity. The future of conveying might be quietly revolving around these unnoticed champions, making thoughtful selection all the more critical.