In the world of material handling and conveyor systems, the role of conveyor return idlers often goes underappreciated, yet their significance in maintaining a smooth, efficient, and safe operation cannot be overstressed. With an evolving industry that increasingly emphasizes precision, durability, and cost-efficiency, understanding the multifaceted functions of these components can optimize operations significantly.
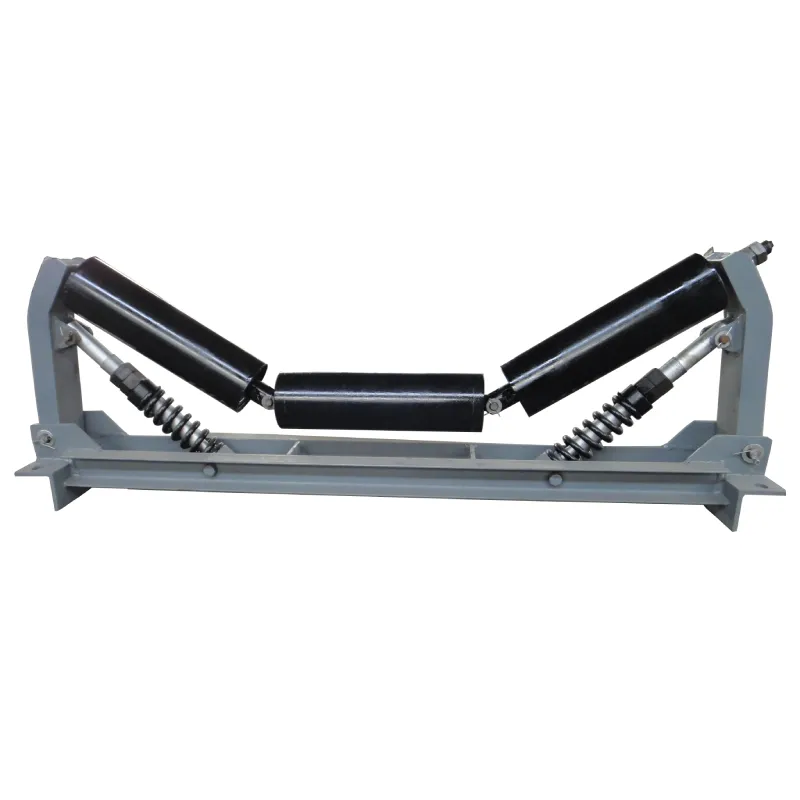
Conveyor return idlers are essential components strategically placed to support the belt on its return trip, minimizing any sagging and ensuring the belt remains aligned. A small misalignment might seem trivial at first glance but can result in significant operational inefficiencies and cost escalations due to increased wear and tear. These idlers are designed to rotate freely, minimizing friction, which is paramount in preserving the belt’s integrity over extended periods.
In an industrial setting, where every component's failure can have cascading effects on production timelines and financial outcomes, reliability and efficiency in conveyor systems are non-negotiable. Employing high-quality return idlers ensures that the conveyor belts can withstand the rigors of constant use. They are typically crafted from durable materials, often steel or high-density polymers, providing the resilience needed to operate in harsh conditions, whether it's extreme temperatures or corrosive environments.
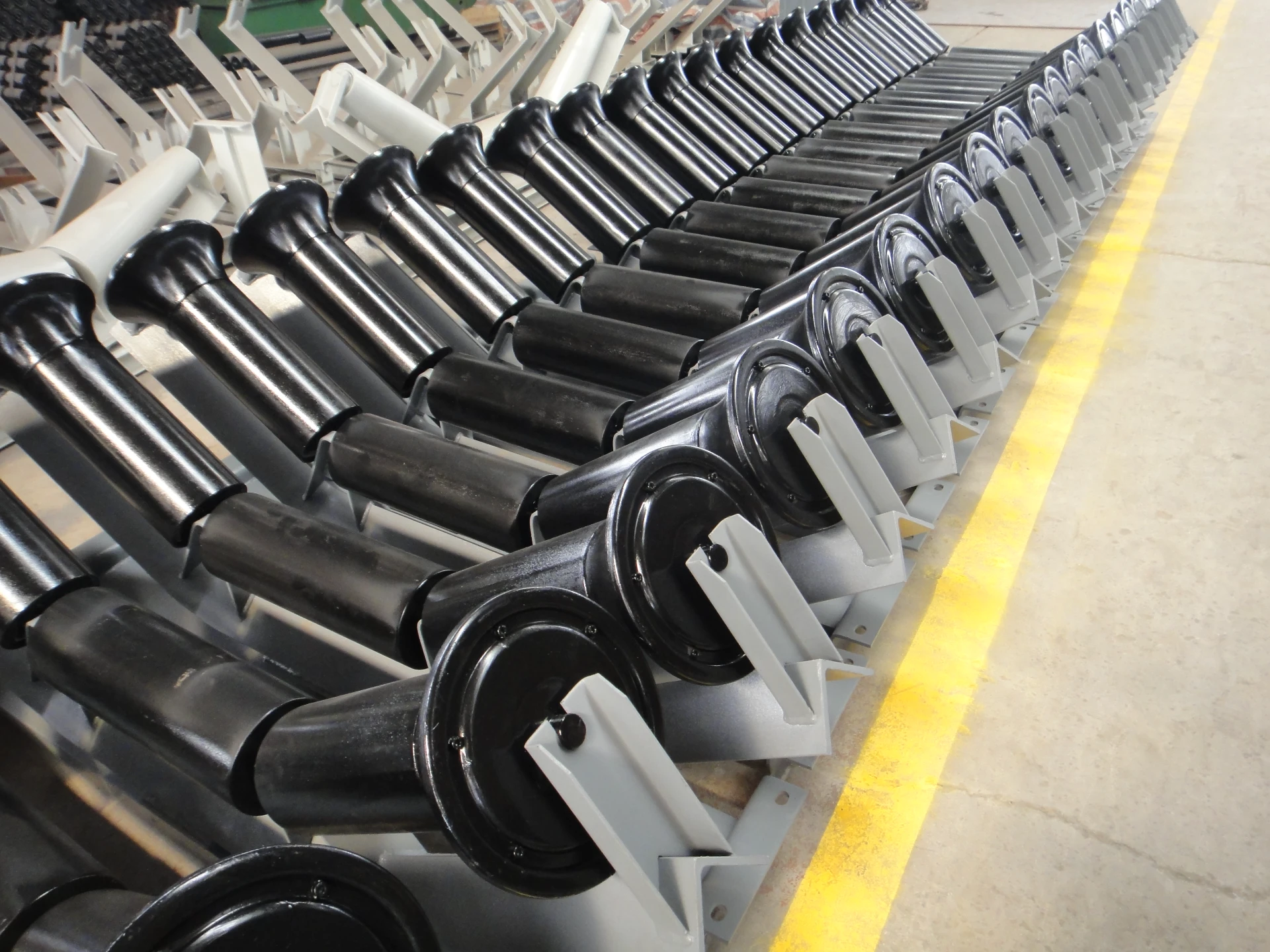
Professional engineers often recommend regular maintenance and timely inspections of conveyor return idlers to ensure they function optimally. A routine check can preemptively identify wear and potential failures, preventing any operational disruptions. Replacement or adjustment should not be delayed, as the repercussions, such as belt damage, increased power consumption, and safety hazards, can be substantial.
Many industries, ranging from mining and heavy manufacturing to agriculture and logistics, leverage conveyor systems with return idlers to streamline their operations. Each sector presents unique challenges that can inform the choice of return idlers. For example, in a mining context where the conveyor system handles heavy loads, the idlers should be robust enough to sustain the weight and abrasive nature of the materials transported. Conversely, lighter-duty idlers might be appropriate in warehousing environments where the load is more manageable and environmental stresses are minimized.
conveyor return idlers
Moreover, advancements in technology have ushered in a new era of efficiency for conveyor return idlers. Smart idler systems, equipped with sensors, now provide real-time data on performance metrics. This innovation allows operations managers to monitor the condition of the conveyor systems remotely, predict when maintenance is required, and make data-driven decisions to enhance productivity.
Thanks to their critical yet understated role, return idlers also contribute significantly towards energy conservation.
A smoothly running conveyor reduces the drag that can lead to increased energy usage. By facilitating effortless belt motion, these idlers help maintain reduced operational costs, aligning with sustainability goals that many companies prioritize today.
When it comes to installation, precision is critical. Misalignment during setup can negate the benefits these components confer. Therefore, employing skilled technicians with expertise in conveyor systems is crucial to ensure that the idlers are installed correctly, minimizing any chances of operational inefficiencies.
In closing, exploring enhancements in conveyor system technology should invariably include evaluating the type and condition of conveyor return idlers being utilized. For businesses aiming to leverage efficiency, reduce downtime, and ensure product longevity in their production lines, investing in high-quality return idlers aligned with their specific operational demands stands as a prudent strategy.
Choosing the right return idlers is not merely a technical decision but a strategic one that reflects a company’s commitment to excellence in operations management. Attention to detail in selecting such components can yield significant competitive advantages, thus demonstrating the intersection of technology, reliability, and strategic foresight in modern industrial practices.