Conveyor return idlers play a critical role in mining, manufacturing, and a plethora of other industries that rely on material transport systems. Understanding the intricacies of these essential components provides valuable insights into maintaining efficient and safe conveyor operations.
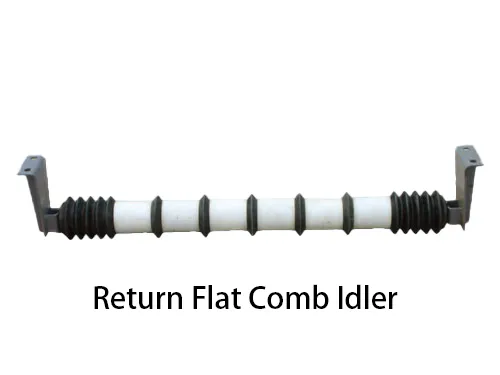
Unlike carrying idlers that support the conveyor belt carrying the load, return idlers support the empty belt on its return journey. This distinction is crucial as return idlers must efficiently support the slack and freely moving belt without adding too much resistance. The reduced weight they handle allows for a variation in design, with options such as single return idlers, V-type, and inverted type configurations depending on the application requirements.
For professionals operating in environments where belt conveyors are integral, selecting the appropriate return idlers can avert system inefficiencies and prevent costly downtimes. An often underestimated aspect of return idlers is their contribution to energy savings. By minimizing friction, wear on the belt can be reduced, thus extending the life of the system and saving costs related to belt replacement. Furthermore, efficient return idlers can contribute to reduced power consumption by ensuring the belt runs smoothly without unnecessary mechanical resistance.
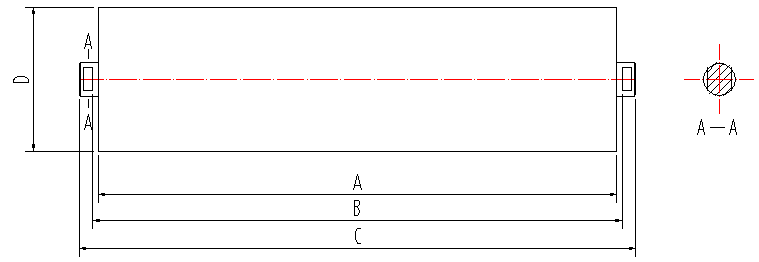
Material selection in return idlers impacts both performance and durability. High-density polyethylene (HDPE) and rubber are common materials for their resistance to corrosive materials and environments, while steel offers robustness essential for heavy-duty applications. Engineers must consider environmental factors — such as temperature fluctuations, humidity, and potential exposure to chemicals — when selecting the materials for return idlers to ensure longevity and reliability.
conveyor return idlers
The installation of return idlers requires precision. Misalignment can lead to belt tracking issues, increasing wear or even causing the belt to derail. Implementing a regular maintenance schedule, including inspections and adjustments, is necessary to keep return idlers functioning properly. In environments with high dust levels, sealed or self-cleaning return idlers might be beneficial to prevent abrasive materials from settling and causing premature wear.
As technology advances, innovations in return idler design continue to emerge. For instance, the integration of smart monitoring systems allows for real-time tracking of idler performance, alerting operators to issues before they result in failures. These systems can enhance the trustworthiness of the conveyor setup by reducing unscheduled downtimes and ensuring operational efficiency.
Expertise in selecting and maintaining return idlers extends beyond basic operational knowledge. It requires an understanding of the specific needs of the conveyor system and the environment it operates in. Consulting experts with a deep understanding of conveyor technologies can provide operators with tailored solutions, ensuring that every aspect of the conveyor system, including the return idlers, minimizes operational risks.
In summary, conveyor return idlers, although often overlooked, are vital components that contribute significantly to the overall performance of conveyor systems. Proper selection, installation, and maintenance of these idlers can enhance system efficiency, reduce operational costs, and extend the lifespan of the conveyor belt. By leveraging advancements in materials and technology, businesses can improve the reliability and efficiency of their conveyor systems, thereby maintaining a competitive edge in their operations.