Selecting the right conveyor pulley lagging material is crucial for the efficiency and longevity of conveyor systems across various industries. Understanding the nuances of different lagging materials can greatly enhance operational productivity and reduce maintenance costs, thereby maximizing return on investment.
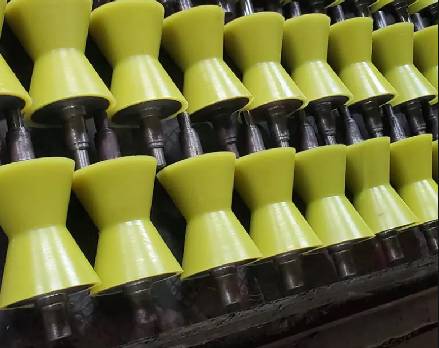
Conveyor pulley lagging is designed to increase the friction between the belt and the pulley. This not only prevents slippage but also plays a pivotal role in protecting the pulley from wear. Among various choices, rubber lagging emerges as a versatile option, widely used in industries such as mining, cement, and steel due to its high tensile strength and wear resistance. Rubber's elasticity provides a cushioning effect, which can mitigate the risk of belt wear and tear.
For environments involving heavy-duty applications and extreme conditions, ceramic lagging is often recommended. Renowned for its exceptional durability and resistance to abrasive materials, ceramic lagging significantly extends the service life of conveyor systems. Its unique dimpled surface enhances grip, making it a preferred choice in industries where material buildup and slippage are concerns. Despite the higher upfront investment, the long-term benefits of reduced maintenance and downtime make ceramic lagging a cost-effective solution.

Polyurethane lagging offers another robust alternative, particularly valued for its chemical resistance in industries where the conveyor system is exposed to oils, solvents, or other corrosive substances. Its lightweight nature reduces the overall strain on the conveyor system, contributing to energy efficiency and minimized operating costs. Additionally, polyurethane's ability to perform in a wide temperature range makes it adaptable to diverse industrial settings.
Each lagging material brings its unique strengths, yet choosing the most appropriate material depends significantly on the specific demands of the application. Factors such as environmental conditions, the abrasiveness of the conveyed material, temperature variations, and load capacity need careful evaluation to select the optimal conveying solution.
conveyor pulley lagging material
Incorporating personalized insights and industry-specific expertise, consultation with conveyor system specialists can provide invaluable guidance. These professionals assess the unique requirements and challenges of a facility, offering tailored recommendations based on years of field experience. Their expertise ensures not only material compatibility but also alignment with operational goals, such as increasing throughput, enhancing safety, and reducing unplanned downtimes.
To establish trustworthiness, manufacturers of conveyor pulley lagging materials should ensure rigorous quality control measures. Certifications such as ISO and compliance with international standards can serve as a testament to product reliability. Case studies and success stories from reputable clients further illustrate the real-world effectiveness of these materials.
Leveraging authoritative content, such as whitepapers and technical manuals, can also enhance understanding and proper usage of pulley lagging materials. This expert-driven information can guide maintenance teams and purchasing departments in making informed decisions.
In conclusion, the strategic selection of conveyor pulley lagging material requires a blend of expert knowledge, authoritative guidance, and a trustworthy approach to procurement and implementation. As industries continue to push for efficiency and cost-effectiveness, investing in the appropriate lagging material remains a cornerstone of durable and efficient conveyor system operation.