Conveyor mounting brackets play a critical role in the industrial and manufacturing sectors, proving indispensable for the seamless operation of conveyor systems. These crucial components secure conveyor systems in place, ensuring operational stability and efficiency. When addressing the needs associated with conveyor mounting brackets, it is essential to understand their influence not only on the machinery but also on the operational outcomes they support.
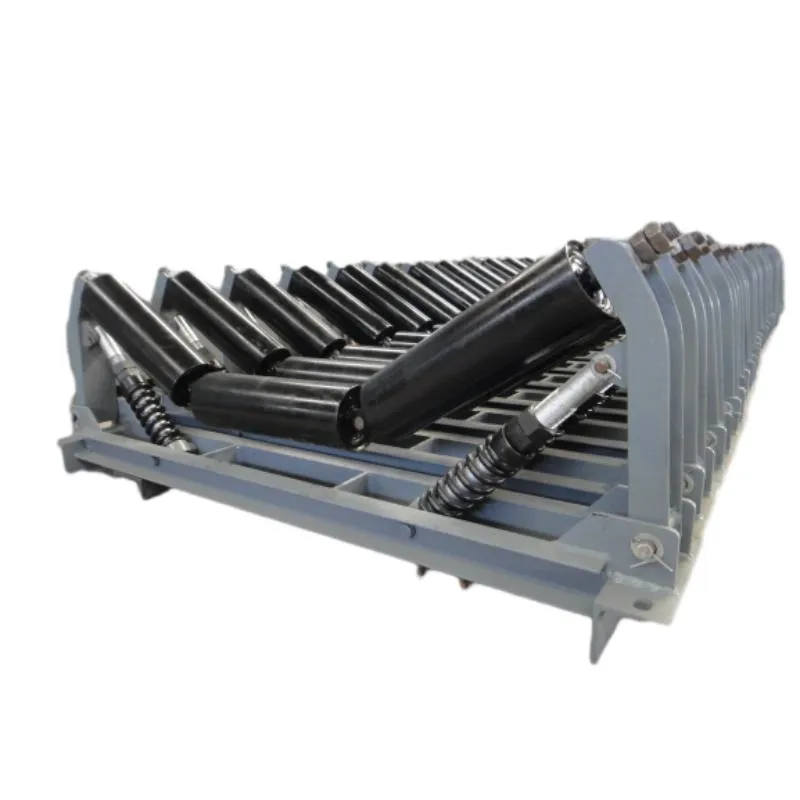
The experience with conveyor mounting brackets can significantly differ depending on their quality and appropriateness for the specific conveyor systems. Those who have engaged deeply with various types of conveyor systems know that selecting the right mounting brackets can enhance system stability, durability, and overall performance. For instance, poorly chosen brackets may lead to costly downtimes due to mechanical failures or misalignments. Thus, investing in high-quality, appropriate mounting brackets is not just a matter of convenience but an assurance of efficiency and reliability in production processes.
From a technical perspective, mounting brackets must possess superior durability and adaptability to different conveyor designs. Constructed from robust materials such as stainless steel or aluminum, these brackets must withstand the mechanical stresses and environmental conditions they encounter. An expertise in material science can guide the appropriate selection of materials that provide optimum strength without unnecessary weight, thus contributing to a more energy-efficient conveyor system.
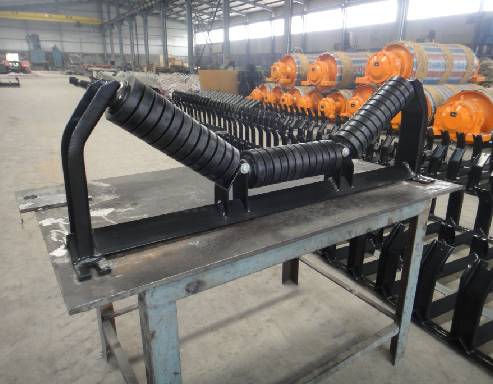
Moreover, the design and engineering of conveyor mounting brackets speak volumes about their effectiveness. Experts in mechanical engineering emphasize the importance of brackets having an adjustable design to cater to different conveyor sizes and configurations. The brackets should allow for easy installation and removal, facilitating maintenance tasks without extensive downtime. As specialists would advise, understanding the load-bearing capacities and specific mechanical requirements of your conveyor system is vital for selecting the ideal mounting brackets.
conveyor mounting brackets
The domain of conveyor systems, continuously evolving with advancing technology, calls for authoritative sources providing guidance on the latest bracket innovations. Technical whitepapers, industry reports, and case studies from reputable engineering firms can serve as valuable resources for understanding the best practices in selecting and utilizing conveyor mounting brackets. Staying updated with these sources ensures access to cutting-edge developments that can enhance operational efficiency.
When considering trustworthiness in the context of conveyor mounting brackets, one must look at manufacturers with proven track records for quality and reliability. Companies with ISO certification or other recognized quality management endorsements tend to offer products that meet stringent manufacturing standards, ensuring consistency and reliability in their performance. Trust is further reinforced by endorsements from third-party testing agencies that validate the safety and efficiency of the mounting brackets before they reach the market.
Customer reviews and testimonials also play an influential role in establishing the trustworthiness of conveyor mounting bracket suppliers. Feedback from industry peers can provide insights into the practical benefits and potential pitfalls of specific product offerings. Engaging with communities and forums where industrial and manufacturing professionals exchange experiences can uncover firsthand accounts of product reliability and customer service, allowing new users to make informed purchasing decisions.
Ultimately, the selection and application of conveyor mounting brackets is a nuanced task that requires careful consideration of multiple factors including material quality, design flexibility, manufacturer credibility, and user experience. As we look to optimize these critical components, it is essential to balance technical specifications with operational needs to achieve the best outcome for conveyor operations. In doing so, businesses can ensure not only the longevity of their conveyor systems but also the sustained efficiency and productivity essential for remaining competitive in a demanding marketplace.