Conveyor lagging, an integral component in conveying systems, requires precise expertise to leverage its full potential effectively. This pivotal element enhances conveyor belt traction, minimizes slippage, and ultimately boosts conveyor system efficiency, playing a critical role in industries ranging from mining to manufacturing. As experts in the field, we are committed to providing in-depth insights that not only inform but also empower your business decision-making process.
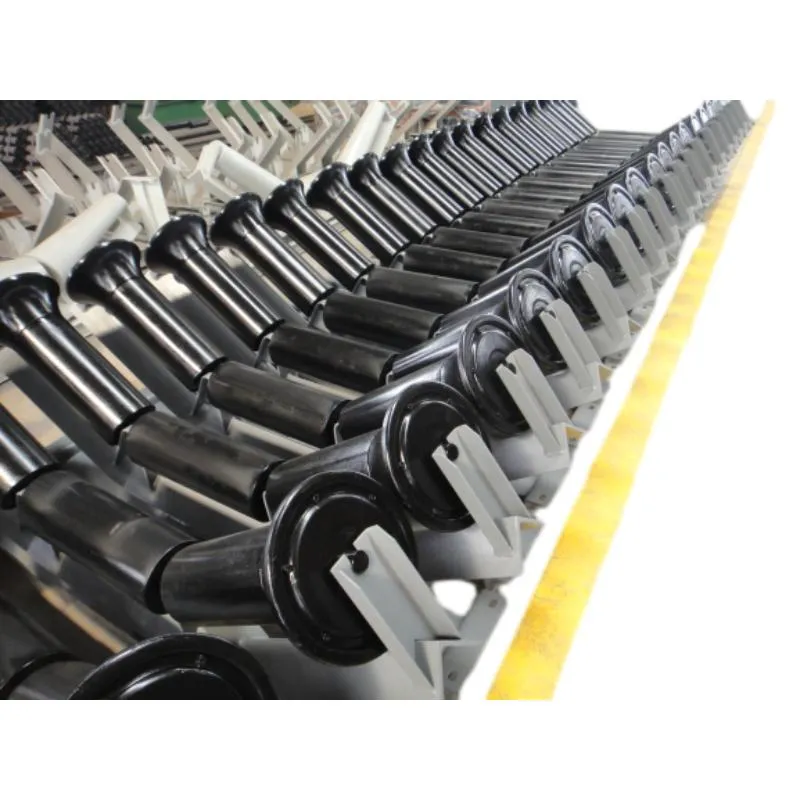
Understanding the nuances of conveyor lagging begins with recognizing its primary function increasing friction between the conveyor belt and the drive pulley. This friction is essential to convey heavy loads efficiently, ensuring operational continuity and enhancing productivity. The expertise to choose the correct lagging material, be it rubber, ceramic, or urethane, hinges on understanding specific operational demands and environmental conditions, such as wet environments, where ceramic lagging stands out due to its superior grip and durability.
The real-world experience gleaned from decades in the field underscores the significance of precise lagging installation. Incorrect installation can lead to increased belt wear, operational downtime, and greater financial costs due to frequent replacements. This is why partnering with seasoned professionals in the field who utilize advanced installation techniques is invaluable, ensuring that each conveyor system operates at peak performance.
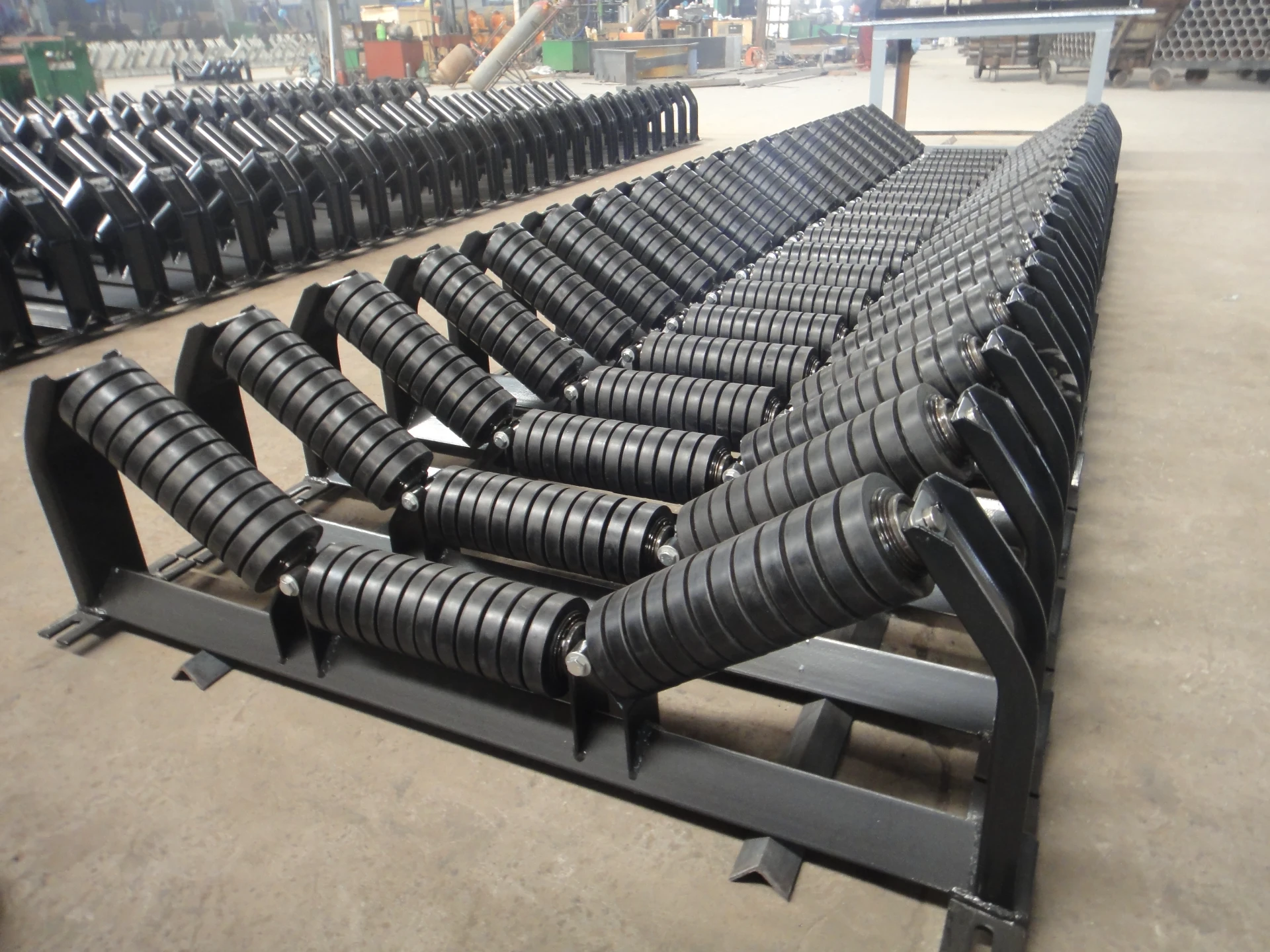
Innovative developments in the industry further bolster the authoritativeness of today's conveyor lagging solutions. Recent advancements, such as self-cleaning lagging, effectively reduce material buildup, ensuring consistent performance and prolonging the lifespan of conveyor belts. Moreover, tailored lagging solutions can now be designed to suit specific operational needs, incorporating proprietary materials that adapt to unique industrial requirements.
conveyor lagging
Trustworthiness is paramount when discussing conveyor lagging due to the safety implications tied to conveyor belt operations. Properly lagged conveyors help mitigate risks of slippage-related accidents, safeguarding both personnel and machinery. Ensuring systematic checks and balances through regular maintenance further enshrines this trust, as it ensures the lagging material performs consistently under varying operational conditions.
A profound understanding of conveyor lagging not only enhances immediate operational efficiencies but also contributes to sustainable environmental practices. By reducing unnecessary energy expenditure and preventing frequent material replacements, high-quality lagging solutions align with eco-friendly initiatives, paving the way for greener industrial practices.
Finally, integrating a well-informed lagging strategy with your conveyor systems enables scalability as your operations grow. By anticipating future demands and potential stressors on your conveyor systems, investing in robust, adaptable lagging solutions ensures long-term operational success.
Conveyor lagging is not merely a technical requirement but a strategic asset in optimizing operational efficiencies. By harnessing the expertise of industry veterans and leveraging cutting-edge technologies, your business can enhance safety, reduce costs, and solidify its competitive edge. Engage with proven professionals to explore how expertly executed conveyor lagging solutions can transform your operational landscape.