When discussing conveyor systems,
the role of the conveyor idler cannot be understated. Its fundamental purpose is to support the conveyor belt and the material being transported. Without an understanding of the different types of conveyor idlers, businesses may face inefficiencies and increased operational costs. This article draws upon extensive industry experience and expertise to explore various types of conveyor idlers, ensuring informed decisions that enhance productivity and trustworthiness.
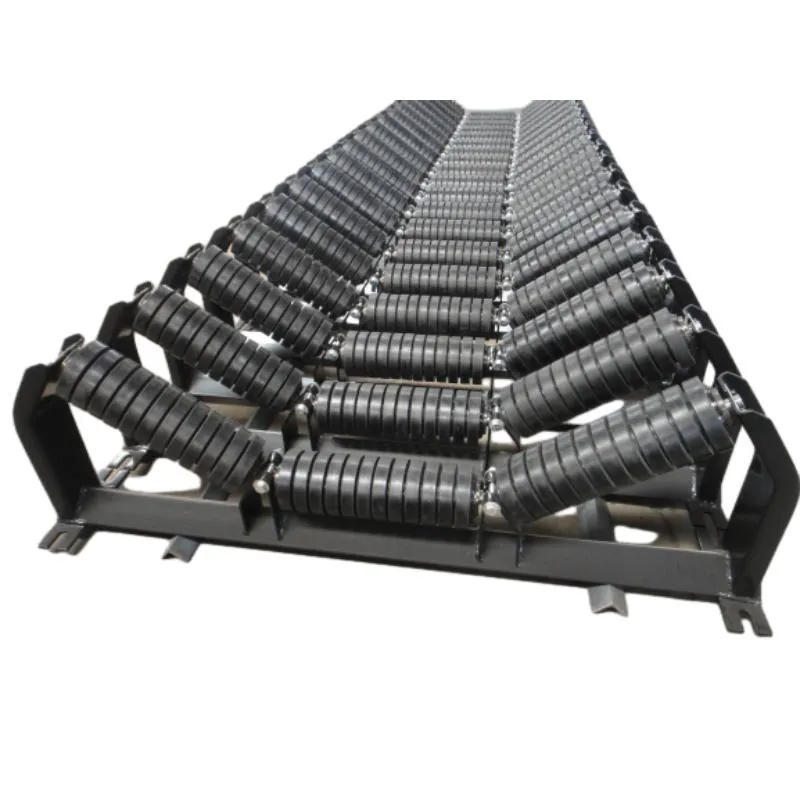
Conveyor idlers are typically divided into three major categories carrying idlers, return idlers, and impact idlers. Each type serves a specialized function within the conveyor system, contributing to its overall efficiency and longevity.
Carrying idlers are primarily used to support the loaded side of the conveyor belt, ensuring that materials are transported smoothly from one point to another. These idlers are essential in maintaining belt alignment and preventing spillage. Common subtypes include troughing idlers, which come in sets of three or more to support wider belts and heavier loads by forming a trough shape. This design reduces spillage and enhances load capacity, instrumental in industries like mining and cement.
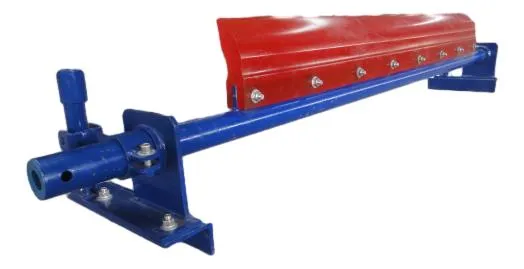
Flat carrying idlers provide a flat surface support for belts carrying uniformly shaped materials such as boxes and packaged goods. Their simple design makes maintenance straightforward, and they are often employed in sortation systems where smooth, precise handling is crucial.
Return idlers support the empty side of the belt as it returns from the discharge end to the feed end. Their primary role is to ensure the belt runs back smoothly, preventing unnecessary wear and tear. Unlike carrying idlers, return idlers usually feature a simpler construction. Standard types include flat return idlers and V-return idlers, the latter of which incorporates two rollers forming a “V” to maintain belt alignment more effectively on longer conveyors or those with variable loads.
Given the harsh environments in which many conveyors operate, selecting the right idler material and design is critical. Steel idlers are robust and suited to heavy-duty operations but can be susceptible to corrosion. Alternatively, HDPE (High-Density Polyethylene) idlers offer excellent corrosion resistance and reduced sound pollution, making them ideal for chemical processing plants or coastal installations.
In high-impact areas prone to material falling from a height, impact idlers are used to absorb shock and minimize damage to both the belt and the idlers themselves. Incorporating rubber disc rollers, these idlers are strategically placed to prolong the conveyor's service life and prevent costly downtime due to maintenance.
conveyor idler types
Given the diverse needs across different industries, proprietary designs and custom-fitted idlers are becoming more prevalent. Businesses specializing in highly specific materials may require tailored solutions to ensure maximum efficiency and safety standards. The innovative use of advanced materials, such as composite rollers, offer numerous benefits over traditional materials, including weight reduction and energy savings through lower rolling resistance.
When selecting the appropriate idler type, factors like load weight, environmental conditions, and belt speed must be considered. A trusted supplier with high expertise in conveyor systems can provide crucial advice, helping businesses choose idlers that align with their operational requirements and contribute to sustainable practices.
The technological evolution in conveyor idler manufacturing has also introduced features like automated idler alignment and monitoring systems. These advancements allow for real-time tracking of idler performance, enabling preemptive maintenance and thus reducing the risk of unexpected failures.
Industry professionals understand that neglected or poorly designed idlers are often the unseen culprits behind conveyor system failures. Investing in the right idler setup not only enhances productivity but also reduces long-term costs and cultivates trustworthiness in system design and functionality.
To implement a reliable and efficient idler system, collaboration with experienced engineers and utilizing reputable suppliers is imperative. This ensures that each component of the conveyor system, especially idlers, is optimized for maximum efficiency and longevity.
In summary, the types of conveyor idlers—carrying, return, and impact—each play a vital role within conveyor systems. Thoughtful selection and proper maintenance of these idlers, tailored to specific industry needs and conditions, will enhance operational efficiency, introduce cost-savings, and instill confidence in the technology utilized. Such informed decisions not only reflect a deep understanding and expertise in conveyor technology but also uphold the principles of authority and trustworthiness in industrial operations.