Conveyor idlers play a pivotal role in the efficiency and longevity of conveyor systems, transcending mere transport functions to become keystones in industrial operations. When selecting the right conveyor idler for a production environment, several critical factors are at play, ensuring the idler delivers optimal performance under demanding conditions.
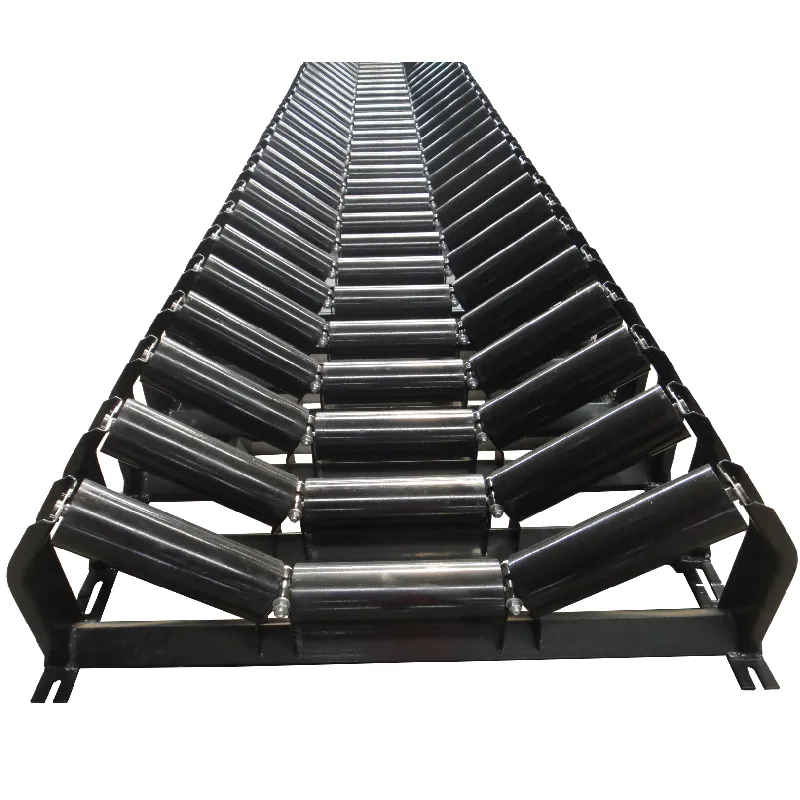
As an industry professional with years of experience in materials handling systems, understanding the nuances of conveyor idlers begins with recognizing the key types carrying, impact, and training idlers. Each is designed for specific tasks; for example, carrying idlers support the conveyor belt, providing stability and reducing drag. Their advanced designs often feature sealed bearing housings, ensuring longevity by preventing contamination from dust and debris—a common challenge in various industrial settings.
When it comes to impact idlers, these are usually positioned at loading points. They are engineered to withstand the substantial forces generated when large or heavy materials are dropped onto the conveyor belt. Utilizing robust materials such as rubber or reinforced polymers, impact idlers not only protect the belt but also enhance operational endurance. This innovation stems from years of specialized expertise, reflecting a thorough understanding of mechanical stresses and material dynamics.
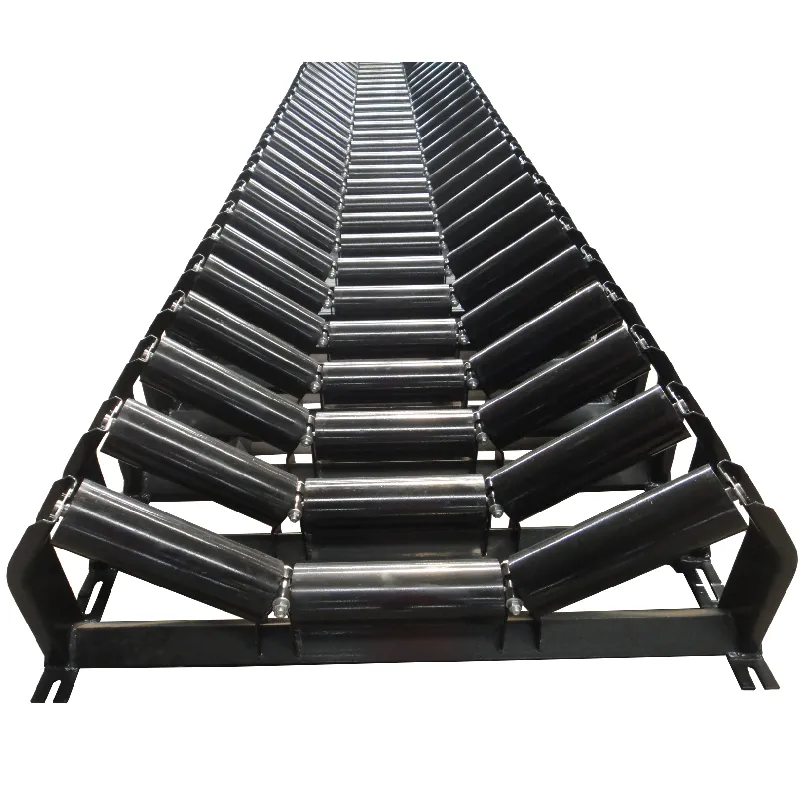
Training idlers, on the other hand, address belt misalignment—a frequent issue in conveyor systems. Misalignment can lead to significant operational inefficiencies, including spillage and increased wear. Designed with pivoting mechanisms, training idlers automatically correct any belt deviation, showcasing engineering excellence and operational reliability. Choosing training idlers with high-precision rotational mechanisms and superior fabrication materials can considerably enhance their effectiveness and lifecycle.
Material selection extends beyond just the idler type and delves into specific idler components. The bearings and shafts are essential elements that determine the operational efficiency and lifespan of the idler. High-quality bearings, typically made from stainless steel or specialized alloys, are recommended to manage both radial and axial loads, minimizing the risk of premature breakdowns. Expertise in metallurgy and materials science informs the choice of these materials, optimizing their performance under various environmental conditions, including temperature extremes and corrosive atmospheres.
conveyor idler
Professional installation and maintenance further bolster the effectiveness of conveyor idlers. Proper alignment and tensioning during installation can prevent common issues such as belt slippage and uneven wear. Additionally, routine inspections and timely lubrication are crucial practices that extend the working life of the idlers. This maintenance regimen should be underpinned by authoritative guidelines grounded in the latest engineering research and industry standards.
Moreover, the development and implementation of conveyor idlers should consider technological advancements. The integration of smart technologies, such as IoT sensors, represents the cutting edge of conveyor system management. These sensors provide real-time data on idler performance, belt load, and speed, enabling predictive maintenance strategies that preempt failures before they occur. Such innovations, driven by expert engineering teams, demonstrate a commitment to enhancing the trustworthiness of supply chains through increased reliability and efficiency.
An effective conveyor idler selection and maintenance strategy not only optimizes production but also underscores a commitment to environmental stewardship. The minimization of material spillage and wear not only advances production continuity but also lessens environmental impact by reducing waste and energy consumption. This aspect of sustainability becomes increasingly vital as industries strive to balance operational needs with ecological considerations.
In summary, conveyor idlers embody a blend of engineering prowess, operational endurance, and innovative thinking. Their role in industrial systems is characterized by a demand for precision, reliability, and a forward-thinking approach that integrates new technologies to deliver trusted, long-term solutions. By harnessing expertise in mechanical design, materials science, and technology, conveyor idlers can significantly enhance operational efficiency while contributing to a sustainable future.