Conveyor head rollers are a crucial component in the world of material handling systems, acting as the driving unit that ensures seamless operation of conveyor belts. As essential elements of industrial conveyors, these rollers must be selected and maintained with expert care to maximize efficiency and reliability.
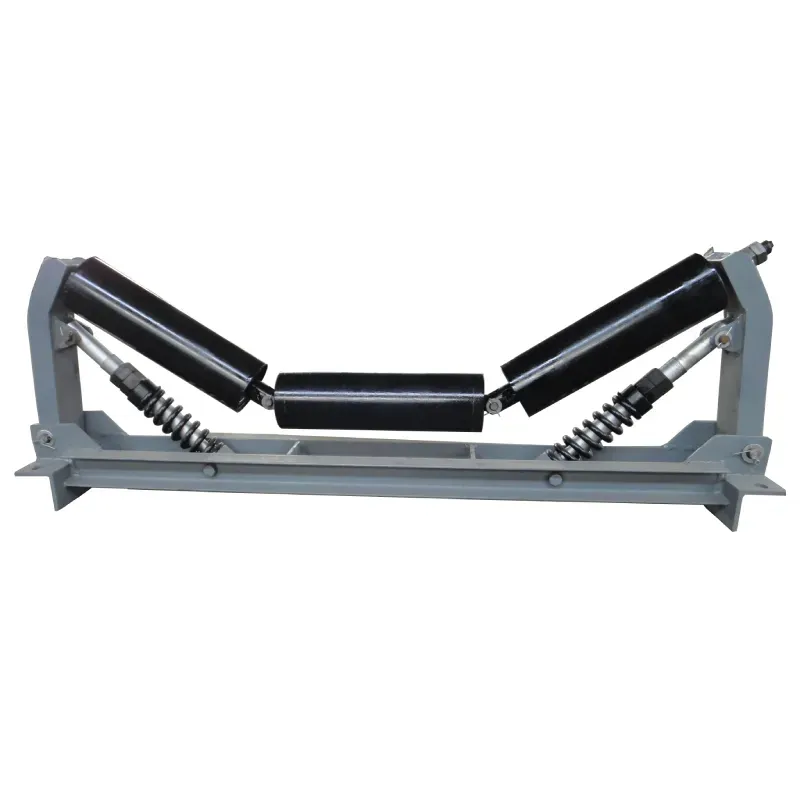
The selection of an ideal conveyor head roller depends largely on the unique operational demands of specific industries. Industries such as mining, manufacturing, and logistics each have distinct requirements, and making informed choices can greatly enhance system performance. Two primary types of conveyor head rollers deserve attention drive rollers and idler rollers. Drive rollers, the mechanical muscles propelling conveyor systems, are strategically designed to transmit torque from the motor to the conveyor belt. This demands precision engineering and advanced manufacturing techniques that utilize materials like rubberized alloys, which provide superior grip and minimized wear.
Opting for a drive roller with an appropriate diameter and material composition is critical. Rollers with the right balance of hardness and elasticity ensure reliable traction while adapting to the operational environment's temperature and moisture levels. In industries dealing with abrasive materials or heavy loads, high-grade steel rollers with protective coatings can provide enhanced durability and longevity.
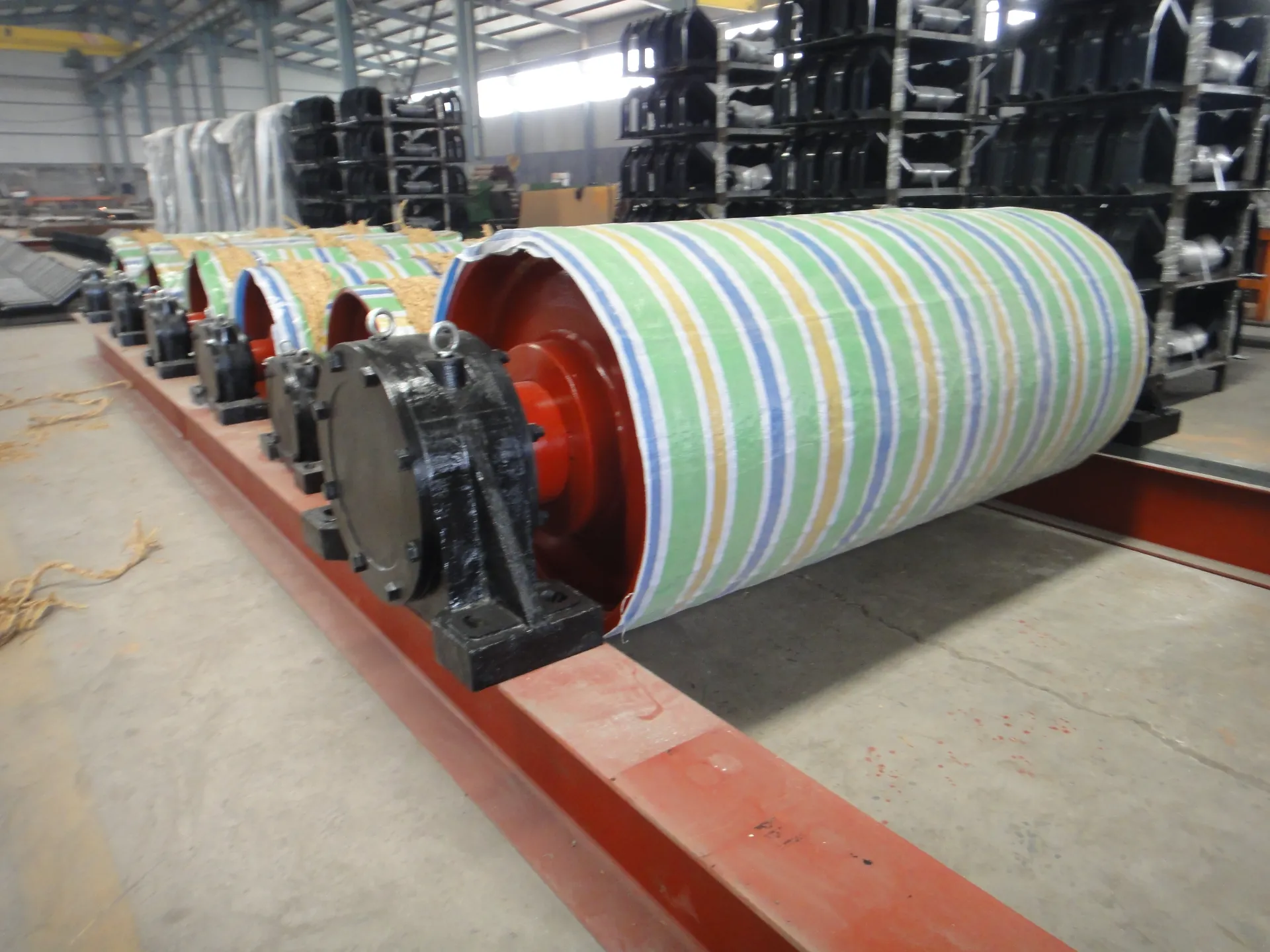
Maintenance is another pivotal aspect influencing the longevity and efficiency of conveyor head rollers. Timely inspections to detect signs of wear, alignment issues, or contamination are essential steps in an effective maintenance routine. Regular lubrication of bearings and careful cleaning to prevent material build-up can extend the lifespan of rollers significantly. Investing in rollers with sealed bearings that offer protection against dust and moisture can also reduce maintenance burden and downtime.
Experts emphasize the importance of customizing rollers to meet specific operational needs. Precision approaches, such as engineering custom diameter rollers or introducing lagging materials specific to operational environments, contribute to optimized performance. Innovative surface treatments can improve grip and reduce energy consumption, presenting a substantial advantage for sustainable operations.
conveyor head roller
A shift towards technologically advanced head rollers is gaining momentum in global markets. Smart conveyor rollers integrated with IoT sensors have emerged as a forward-thinking solution, offering real-time monitoring capabilities. These sensors provide critical data on roller speed, temperature, and wear conditions, enabling predictive maintenance and minimizing unexpected failures. This technological integration not only reduces operational costs but aligns with sustainability goals by prolonging equipment life.
Manufacturers from around the globe advocate for eco-friendly production practices, realizing the growing demand for sustainable solutions. Recycled materials in the production of conveyor head rollers contribute to the reduction of carbon footprints and promote responsible resource utilization.
The expertise required to design and select conveyor head rollers entails a comprehensive understanding of the material characteristics, operational challenges, and environmental conditions. Collaboration between engineers and material scientists often results in innovative designs that address specific industrial challenges. As thought leaders in the conveyor manufacturing industry, experts take pride in sharing best practices and insights that guide the development of superior products designed to withstand the test of time.
In conclusion, conveyor head rollers are indispensable components in material handling systems, demanding careful selection, tailored designs, and pro-active maintenance to optimize functionality. Embracing advancements in technology and sustainable manufacturing practices can position industries at the forefront of efficiency and innovation. Engaging with experienced professionals ensures that systems not only meet the demands of today's industrial landscape but do so with a forward-thinking approach that promises resilience and adaptability.