The conveyor head and tail pulleys are critical components in conveyor systems, serving as the driving and guiding forces for belts in various material handling applications. For organizations aiming to optimize operational efficiency and bolster safety, understanding these components' intricacies is imperative.
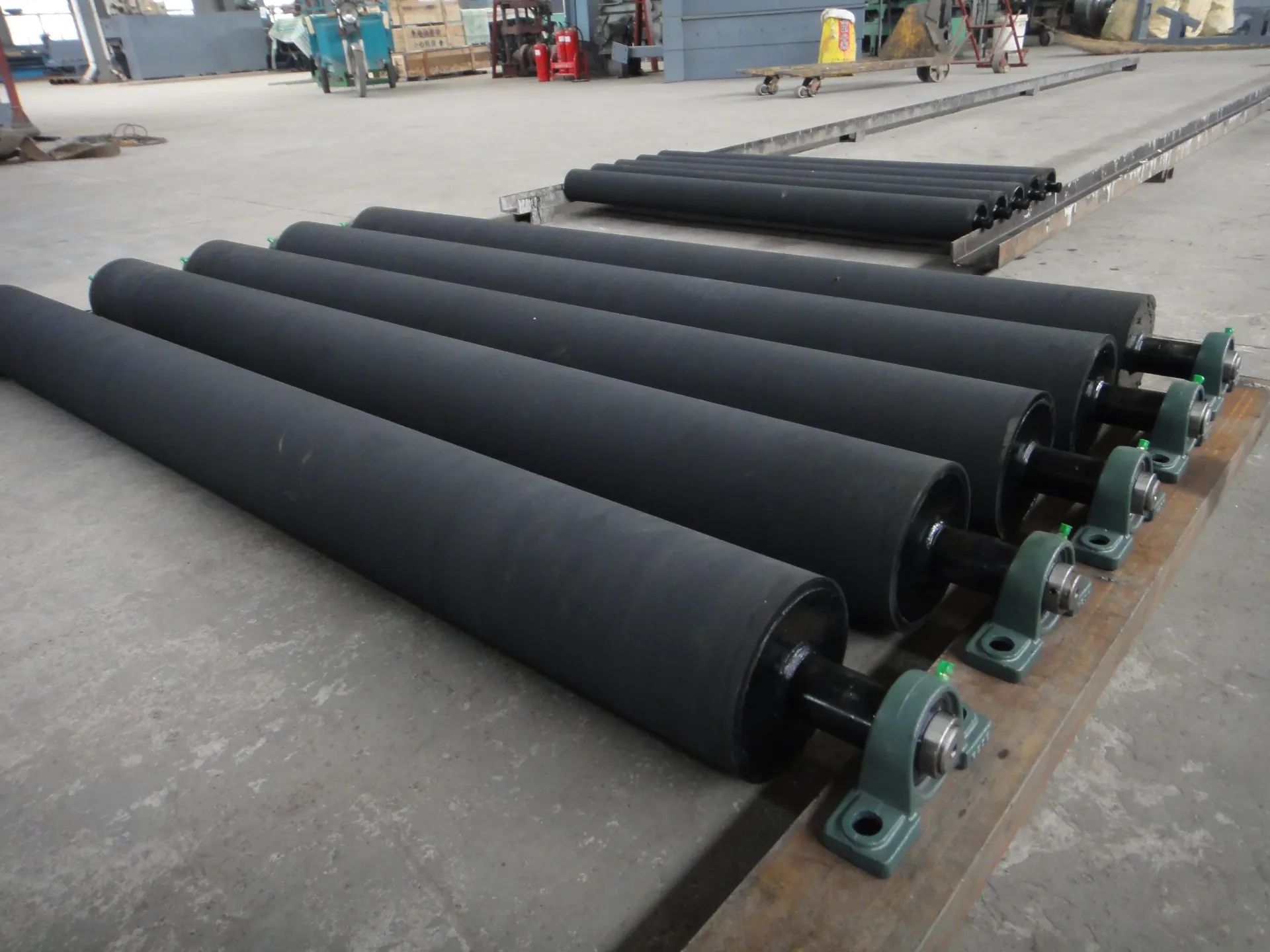
Conveyor head pulleys, positioned at the discharge end of the conveyor, are predominantly responsible for driving the conveyor belt. Their primary function is to guide the motion of the belt as it releases material, ensuring that the product is efficiently conveyed to subsequent processing stages or collection points. Advanced designs incorporate dynamic balancing and robust materials such as steel or aluminum, enhancing the durability and precision of head pulleys. By evenly distributing stress across the belt surface and minimizing wear, these pulleys markedly reduce maintenance costs and downtime, providing a financially prudent solution for long-term operation.
Conversely,
tail pulleys are situated at the loading end of the conveyor system. Their role extends beyond merely supporting the belt; they maintain tension and alignment, which is crucial for stable and efficient belt performance. Notably, free-turning tail pulleys aid in reducing friction-induced wear and conserve energy by decreasing the drive force needed to operate the conveyor. This translates to lower operational costs and a reduced environmental footprint, aligning with sustainable practices that are increasingly prioritized in the industry.
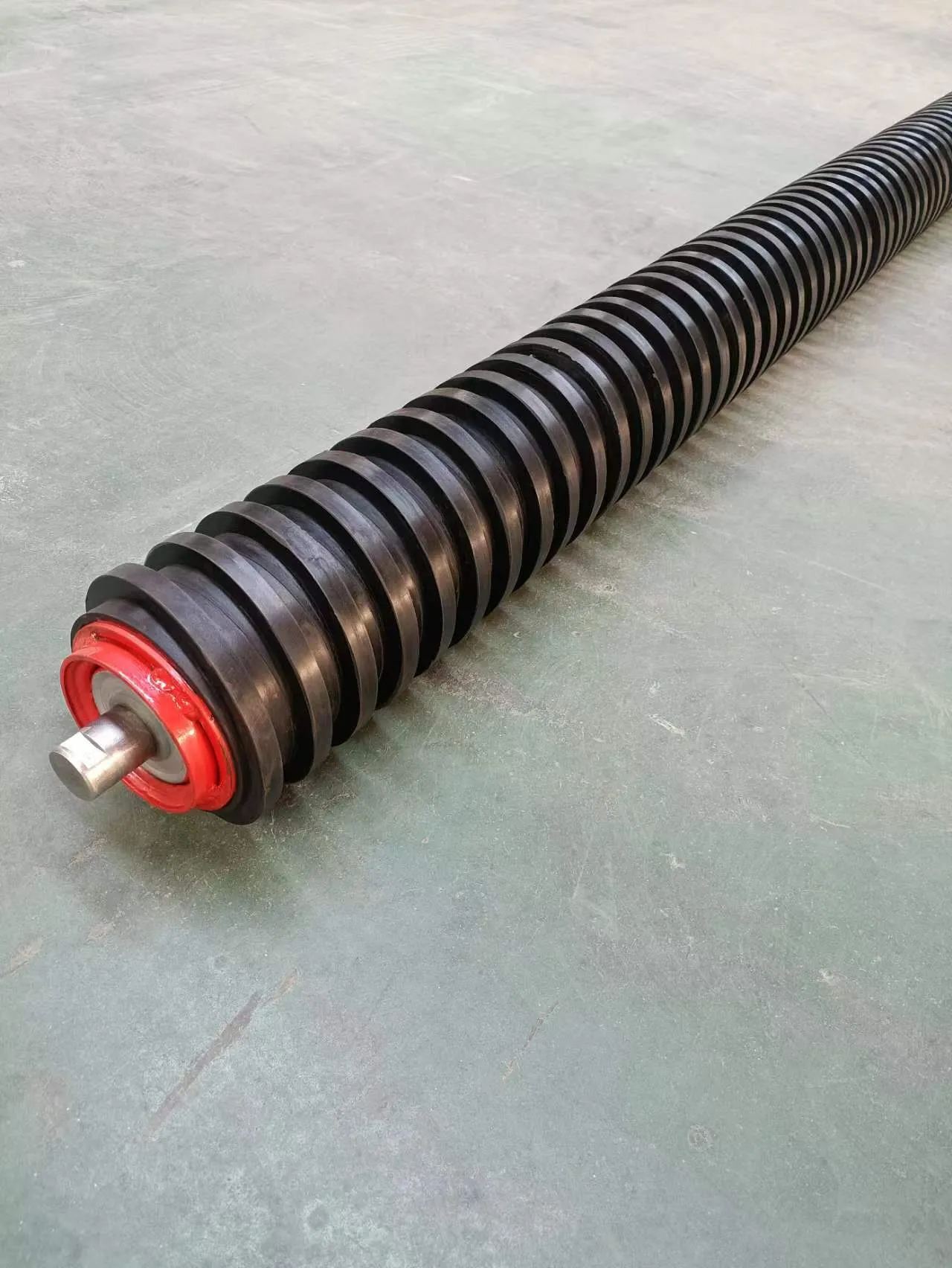
Choosing the right head and tail pulleys involves a meticulous assessment of the conveyed materials, operational speed, and environmental conditions. For instance, operations dealing with abrasive materials may favor ceramic lagging on head pulleys to bolster resistance against wear. Lagging can significantly enhance the lifespan of the pulley by providing better grip and reducing slippage. Tail pulleys often benefit from self-cleaning options to mitigate material build-up that could compromise belt tracking or lead to wear.
Installations in extreme environmental conditions, such as those requiring high corrosion resistance or extreme temperature endurance, influence material selection for pulley construction. Stainless steel and specialty alloys cater to these demands, ensuring uninterrupted operation in adverse conditions while maintaining structural integrity.
conveyor head and tail pulley
The integration of technology in the design and monitoring of conveyor pulleys has ushered in an era of predictive maintenance and performance optimization. Sensor technology can provide real-time data on pulley alignment, vibration, and temperature, allowing for proactive intervention before minor issues escalate into costly repairs. This technological advance not only enhances efficiency but also ensures safety by minimizing the risk of system failure.
Furthermore, the strategic design of head and tail pulleys contributes significantly to improving worker safety and operational efficiency. Ergonomically designed systems with accessible maintenance points reduce manual strain and downtime. Incorporating smart technologies, such as sensor-equipped monitoring systems, facilitates the prediction of potential failures, averting hazardous situations and supporting seamless system maintenance.
In highly competitive industries where productivity and operational safety are paramount, the role of conveyor head and tail pulleys cannot be overstated. Companies that invest in high-quality pulleys benefit from improved ROI, lower operational costs, and enhanced safety standards. Experts recommend regular training for maintenance personnel, ensuring they are well-versed in the latest pulley technologies and best safety practices. This not only fosters a culture of efficiency and reliability but also promotes a collaborative environment where operational excellence is continuously pursued.
To capitalize on the advancements in conveyor technology, a collaborative relationship with experienced manufacturers or consultants is advisable. They can provide insights into customizing pulley systems to meet specific operational needs and ensure compliance with industry standards. A strategic partnership with experts infuses the customization process with knowledge and experience, resulting in systems that drive sustained operational success and safety.
Ultimately, conveyor head and tail pulleys are more than mere components within a system. They represent the synergy of engineering excellence, innovative technology, and strategic design. By prioritizing quality and leveraging the latest advancements, organizations can ensure that conveyor systems operate at their highest potential, facilitating safe and efficient material handling in any industrial setting.