In a bustling industrial environment, conveyor systems play a critical role in enhancing productivity and efficiency. Central to the success of these systems is a component often overlooked yet fundamental to the optimal operation and longevity of the entire conveyor system conveyor drum lagging. This article delves into the nuances of conveyor drum lagging, exploring its types, benefits, and the rationale behind its necessity, drawing upon years of industry expertise and practical insights.
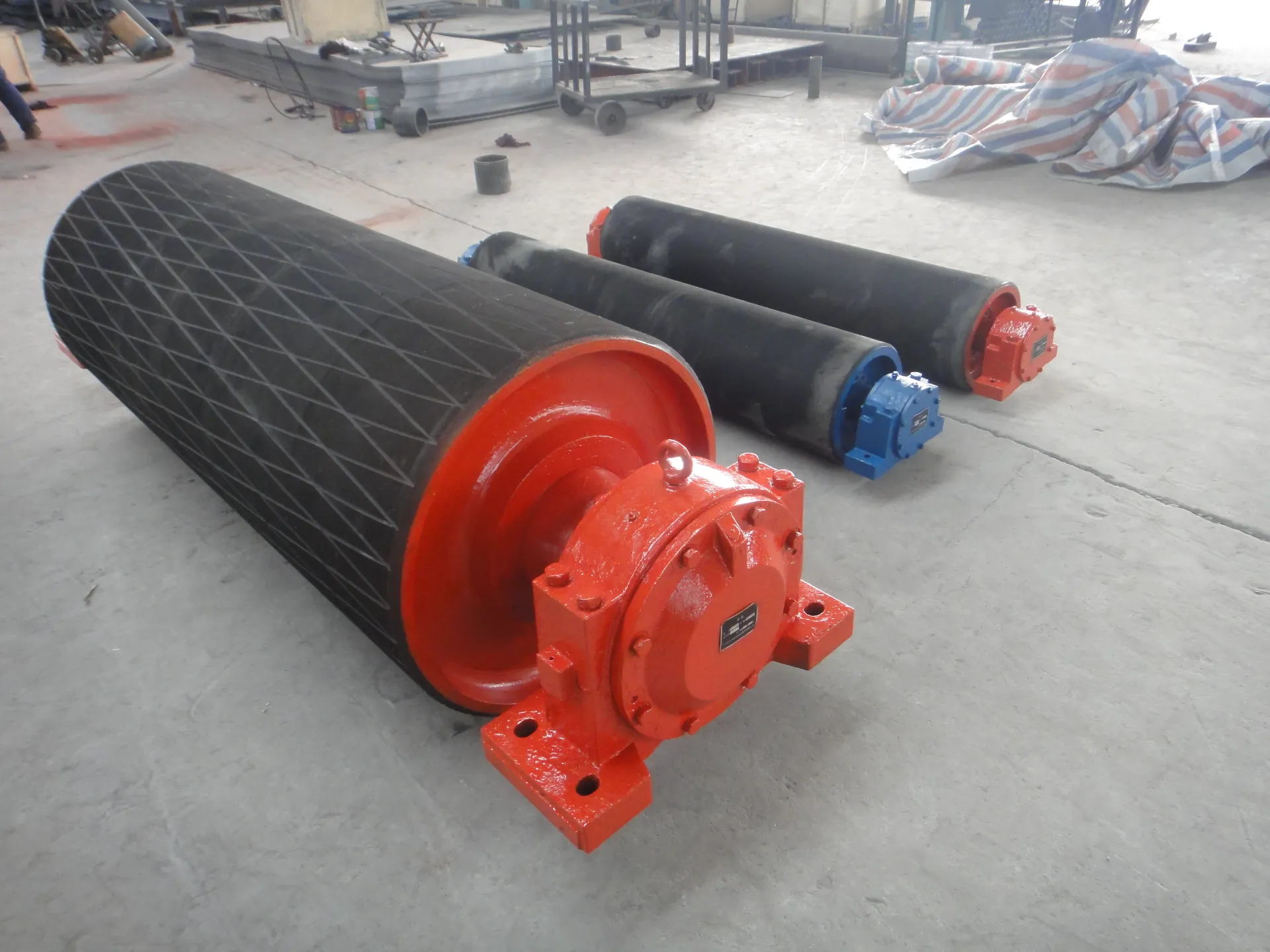
Conveyor drum lagging refers to the protective layer applied to the surface of conveyor pulleys. This protective layer can be made from a variety of materials including rubber, ceramic, and polyurethane, each offering distinct attributes suitable for different applications. The primary function of lagging is to increase the coefficient of friction between the drum and the conveyor belt, reducing slippage and improving belt traction. This frictional attribute not only ensures the smooth and efficient operation of conveyor systems but also prolongs the life of the belt and the drum itself.
Rubber lagging, often composed of natural or synthetic rubber compounds, is the most commonly used type due to its flexibility and cost-effectiveness. It's particularly effective in environments where moisture is a concern, offering excellent water resistance. In contrast, ceramic lagging is selected for high-tension conveyor applications. This type of lagging incorporates ceramic tiles that provide a superior grip and are remarkably durable under abrasive conditions. Lastly, polyurethane lagging is sought after for its extreme resilience and ability to withstand prolonged exposure to harsh chemicals, making it suitable for specialized industries like mining and chemical processing.

From an operational perspective, the implementation of conveyor drum lagging has proven transformative. By addressing the prevalent issue of belt slippage, operational downtime is significantly reduced, thereby maintaining consistent productivity levels. For industries reliant on heavy-duty and high-throughput operations, such enhancements are not just beneficial but essential. Moreover, the reduction in slippage also decreases energy consumption, which translates into cost savings and a lower environmental footprint.
One of the most compelling reasons for the growing adoption of conveyor drum lagging is its direct impact on maintenance costs. The friction reduction it provides minimizes unnecessary drum and belt wear. Without lagging, friction-induced wear could lead to frequent replacements of conveyor belts and drums, escalating maintenance expenses. Thus, the application of conveyor drum lagging is not merely a preventive measure but an economically prudent one.
conveyor drum lagging
Credentials and experience matter greatly in the application and selection of the appropriate type of conveyor drum lagging. Choosing the right product involves understanding the specific needs of an operation, including the nature of the materials being transported, environmental conditions, and the operational demands of the conveyor system. Consequently, consulting with seasoned professionals who possess comprehensive expertise in belt systems and materials handling is advisable. Their authoritative experience ensures a tailored approach, maximizing both the performance and lifespan of the conveyor system.
Trust in supplier credibility is another cornerstone in the successful utilization of conveyor drum lagging. With manufacturers innovating rapidly to enhance the qualities of lagging materials, sourcing from reputable suppliers ensures that you are accessing cutting-edge solutions. Quality assurance and adherence to industry standards by these suppliers are critical in safeguarding against potential safety hazards and ensuring compliance with regulatory requirements.
Real-world experiences reiterate that the decision to integrate conveyor drum lagging should be considered an integral component of conveyor system design and maintenance strategy. Reports from various industries highlight a noticeable improvement in operational stability and equipment reliability post-installation. Testimonials from maintenance teams underscore not only a reduction in unexpected breakdowns but also a marked decrease in repair frequency and material wastage.
In conclusion, while conveyor drum lagging might seem like a minor component within larger systems, its implications are substantial. Embracing this technology can markedly elevate system performance and provide a considerable return on investment through increased efficiency, reduced maintenance, and enhanced safety. As such, the dialogue around conveyor drum lagging should not be confined to technical circles but broadened to encompass decision-makers who are tasked with steering industrial operations towards more sustainable and forward-thinking practices.