Conveyor drum lagging plays a crucial role in the optimal functioning of conveyor systems across various industries. As someone with extensive expertise in the field, I have witnessed first-hand the advantages of high-quality drum lagging and its integral role in prolonging the lifespan of conveyors while enhancing safety and performance.
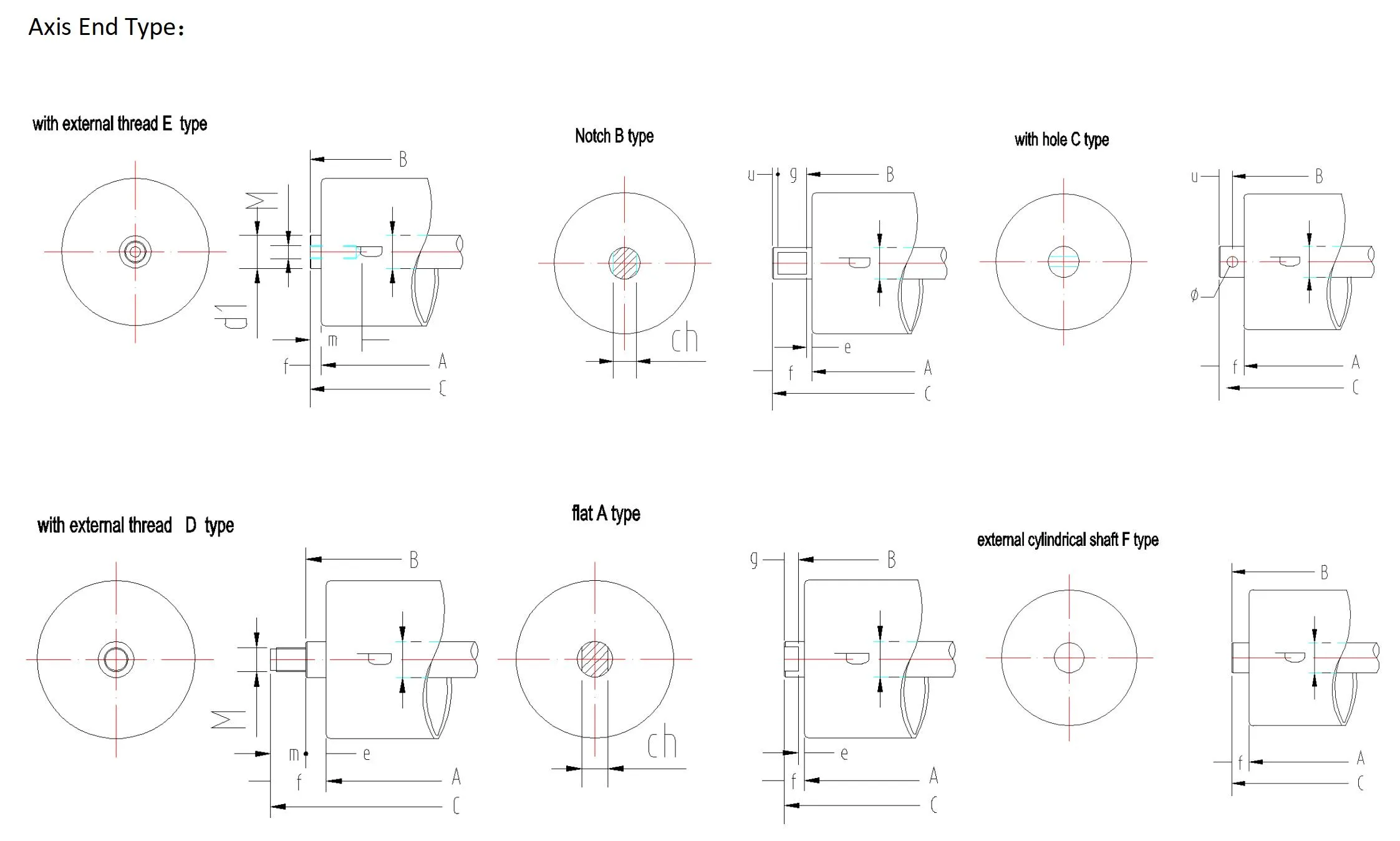
Experience underscores the importance of selecting the right type of conveyor drum lagging. Over the years, I've observed that companies that invest in superior drum lagging materials enjoy a substantial reduction in maintenance costs and downtime. The interaction between the conveyor belt and the drum is a key factor. Properly installed lagging enhances grip, which minimizes belt slippage and reduces the risk of belt misalignment—common issues that can lead to costly replacements and repairs. Quality lagging materials, such as ceramic, rubber, or polyurethane, can effectively provide the necessary friction and wear resistance, suitable for the operational conditions of both the environment and the material handled.
Expertise in drum lagging requires understanding the specific requirements of each application. Not all conveyor systems are created equal,
and neither are their lagging needs. High-temperature applications, for instance, call for laggings with superior heat resistance, whereas applications involving corrosive materials demand chemical-resistant properties. Selecting the incorrect lagging material can lead to rapid deterioration and operational inefficiencies. Therefore, a profound knowledge of material properties, coupled with precise assessment of operational conditions, is essential for effective drum lagging solutions.
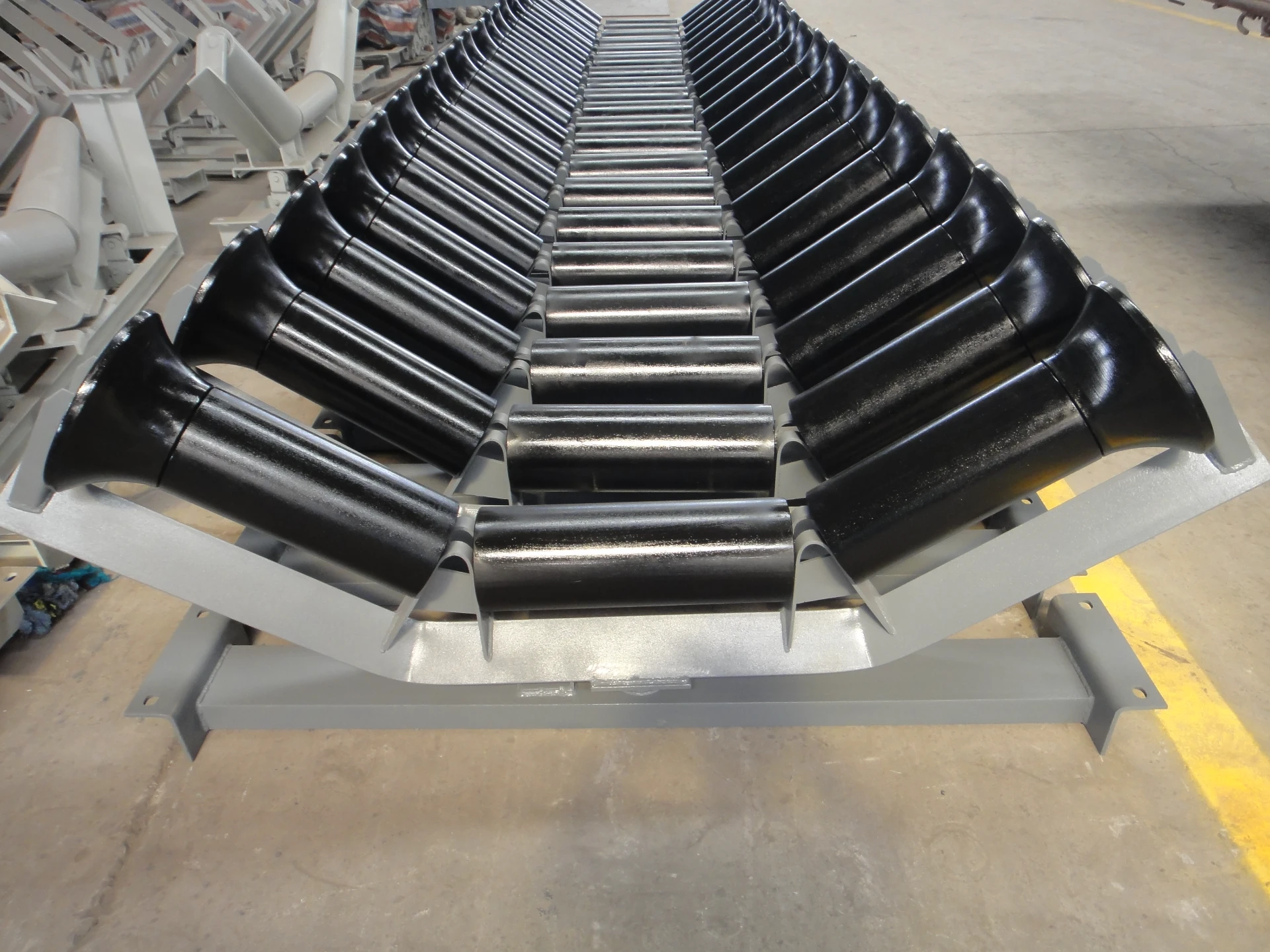
conveyor drum lagging
Authoritativeness is demonstrated through our ability to guide industries in making informed decisions aligned with their unique operational needs. Diving deeper into why quality drum lagging is vital, it's clear that it can significantly mitigate operational risks. Smooth and uninterrupted conveyor operations ensure that production targets are met consistently, and operational hazards like belt misalignment or slippage are significantly minimized. This not only aids in meeting regulatory safety standards but also cultivates a safe working environment which is at the heart of sustainable industrial operations.
Trustworthiness in delivering effective conveyor drum lagging solutions is built on decades of accumulated knowledge and successful project implementations. Many industries rely on expert guidance to navigate complex operational challenges. Trust is earned through demonstrable success, from reducing operational bottlenecks to enhancing production efficiency. Testimonials and case studies from satisfied clients reflect this trust. Companies that source their components from reputable suppliers validate not only the quality of the materials used but also the efficacy of the implemented solution.
In conclusion, conveyor drum lagging is an unassuming yet essential component in the logistical dance of production. Leveraging it effectively demands a balance of experience, expertise, authoritative guidance, and established trust. Whether it's ensuring minimal downtime or maximizing the lifespan of conveyor belts, investing in the right drum lagging solution is pivotal. As industries evolve and requirements become more challenging, it remains our responsibility to adapt and deliver solutions that reflect not only the current needs but also anticipate future demands. Always prioritize quality and expertise; your operations depend on it.