Ensuring optimal performance and longevity of your conveyor belt system is critical to maintaining efficient operations. One aspect that often gets overlooked is the adjustment of the conveyor belt scraper. With years of experience in conveyor system maintenance and management, I will detail the intricacies of this essential component, shedding light on best practices and expert tips for adjustment.
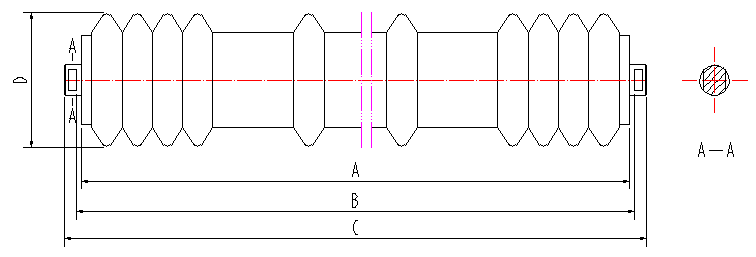
A conveyor belt scraper, also known as a belt cleaner, is an integral part of a conveyor system. Its primary function is to keep the conveyor belt clean by removing any material adhering to the belt. Proper adjustment of these scrapers is crucial not only for maintaining cleanliness but also for preventing wear and tear, which can lead to costly downtimes.
Experience has shown that the first step in ensuring proper scraper adjustment is selecting the right type for your specific conveyor system. Scrapers come in various designs, including primary, secondary, and tertiary configurations. Primary scrapers are typically installed on the head pulley, while secondary and tertiary evolve as additional cleaning stages further along the conveyor. Ensuring you have the correct scraper configuration tailored to the material being transported is fundamental.
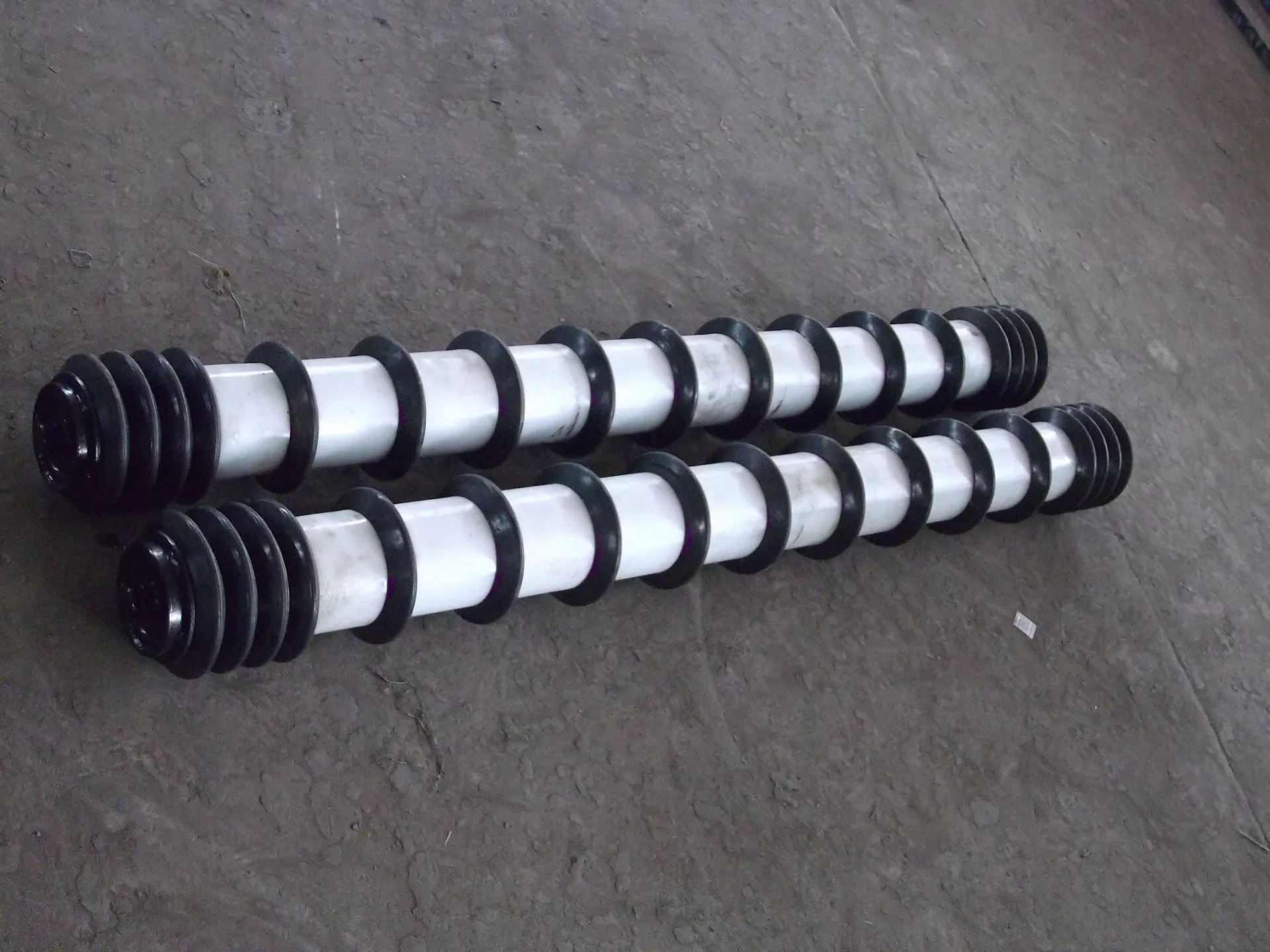
Expertise in this field tells us that regular inspection of scrapers is necessary. This involves checking for wear and ensuring that tension settings are correct. Effective tension maintains scraper-to-belt contact, which is pivotal for efficient material removal. Too little tension and the scraper will be ineffective; too much tension risks damaging the belt. Therefore, achieving and maintaining the optimal tension is a fine balance that must be managed meticulously.
conveyor belt scraper adjustment
Adjustments should be made based on the manufacturer's guidelines and the specific conditions of the conveyor system. When adjusting scrapers, make sure to clean the belt thoroughly, using a gauge to measure scraper positioning. Utilize materials and tools designed for the adjustment process to prevent accidental damage to the scraper or the belt. Testing the scraper's effectiveness post-adjustment is also crucial — run a small load to ensure it's clearing all residues without causing smearing or unnecessary strain on the motor.
Authoritativeness in this domain is bolstered through data-backed methods. Utilize sensor technology where possible, to provide real-time feedback on scraper performance. This integration of technology not only guides more precise adjustments but also introduces predictive maintenance capabilities, highlighting potential issues before they cause interruptions. This proactive approach results in increased reliability and efficiency, reinforcing productivity across operations.
Trustworthiness in conveyor system maintenance arises from consistency and a commitment to best practices. Implement a regular maintenance schedule that includes detailed records of adjustments, inspections, and any parts replacements. Engaging with experts is also advisable, fostering a culture of learning and adherence to the latest industry standards and innovations.
In conclusion, the process of conveyor belt scraper adjustment is a nuanced task that demands a blend of experience, expertise, authority, and trustworthiness. By leveraging these principles, you ensure smoother operations, reduce downtime, and extend the lifespan of your conveyor system. By maintaining a systematic adjustment regimen, employing the latest technology, and following expert guidelines, you can optimize your conveyor systems for peak performance. Regular investment in training and development of personnel also ensures that these adjustments are accurately and effectively managed, leading to a more productive and reliable operation.