Conveyor belt scrapers are an essential component in the bulk material handling industry, ensuring materials are efficiently and effectively moved, minimizing spillage, and maintaining cleaner belt surfaces. Adjusting these scrapers properly is crucial for optimal performance and longevity. Drawing on decades of experience in conveyor systems, this guide explores the intricacies of conveyor belt scraper adjustment, backed by industry expertise and trustworthiness.
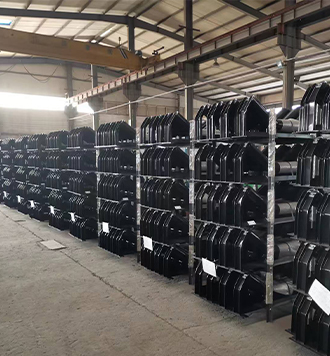
Understanding the Importance of Proper Scraper Adjustment
Conveyor belt scrapers serve the vital purpose of cleaning the belt surface, preventing material buildup that can lead to uneven wear, belt misalignment, and inefficiencies in material handling. An improperly adjusted scraper can allow fines and debris to escape, leading to costly clean-ups and potential system downtime. Thus, achieving the right balance, placement, and pressure is fundamental to ensuring operational efficiency.
Experience-based Techniques for Scraper Adjustment
Professionals with hands-on experience emphasize the importance of tailored adjustments based on belt speed, material nature, and scraper type. For instance, accommodating for variations in temperature can prevent damage from excessive expansion or contraction. Furthermore, experienced operators know that periodic inspections find that even new systems may require recalibration as components settle.
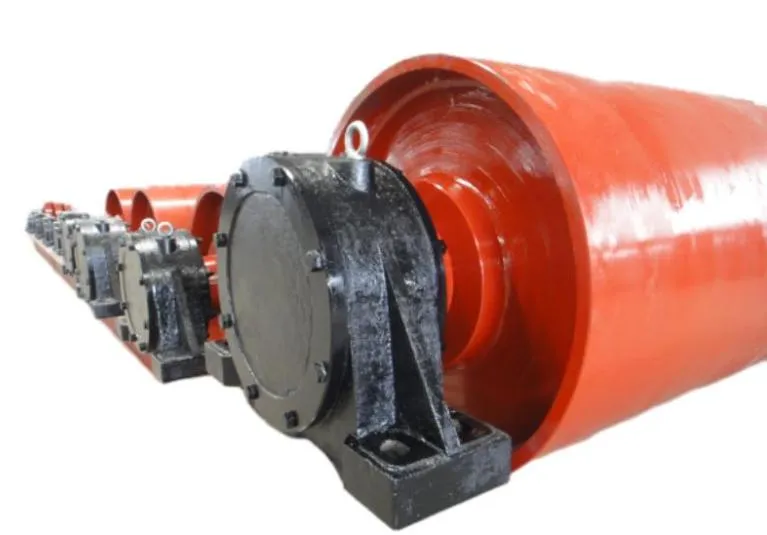
Professional Expertise on Scraper Types and Their Adjustments
The scraper type dictates the necessary adjustment techniques. Primary scrapers, located near the head pulley, require careful alignment to remove the bulk of material while secondary scrapers, positioned further downstream, focus on finer residues. Adjusting pressure based on the scraper material—polyurethane versus tungsten carbide—impacts durability and efficacy. Mastery of these nuances highlights the role of expert knowledge in maintaining high-functioning conveyor systems.
conveyor belt scraper adjustment
Authoritative Guidance on Balancing Efficiency and Maintenance
Industry authorities stress the need for regular maintenance checks to ensure that scrapers are performing optimally. Routine monitoring can prevent excessive blade wear, which if unchecked, may damage the belt. Adjustments should maintain a contact point that ensures steady pressure without excessive force that can lead to belt damage or premature scraper wear. Authoritative voices recommend adopting an adjustment protocol that includes checking scraper tension and alignment after every few operational hours, particularly for demanding environments.
Establishing Trust through Demonstrated Reliability and Performance Optimization
Reliable conveyor performance hinges on trust in the adjustment process, which is built through consistent outcomes and documented procedures. Document adjustments meticulously, noting the conditions and settings for future reference—a practice that builds trust both internally within maintenance teams and externally with stakeholders. Historical data, integrated into maintenance records, provides an invaluable resource for refining future processes and decision-making.
Through rigorous adjustment procedures and an understanding rooted in real-world practice, businesses can enhance the reliability and efficiency of their conveyor belt systems. Opting for expert guidance tailored to specific operational contexts not only prolongs the life of the conveyance systems but also significantly boosts overall productivity. By prioritizing accurate conveyor belt scraper adjustments, companies can achieve seamless operations and solidify their standing as industry leaders.