The concave guide roller is an essential component in various industrial and commercial applications, specifically in fields requiring precise measurement, intense loading, or delicate material handling. While not widely recognized outside of specific industries, its contribution cannot be overstated. This piece aims to explore the intricacies and advantages of concave guide rollers, providing insights that underscore their indispensable nature in modern engineering and manufacturing.
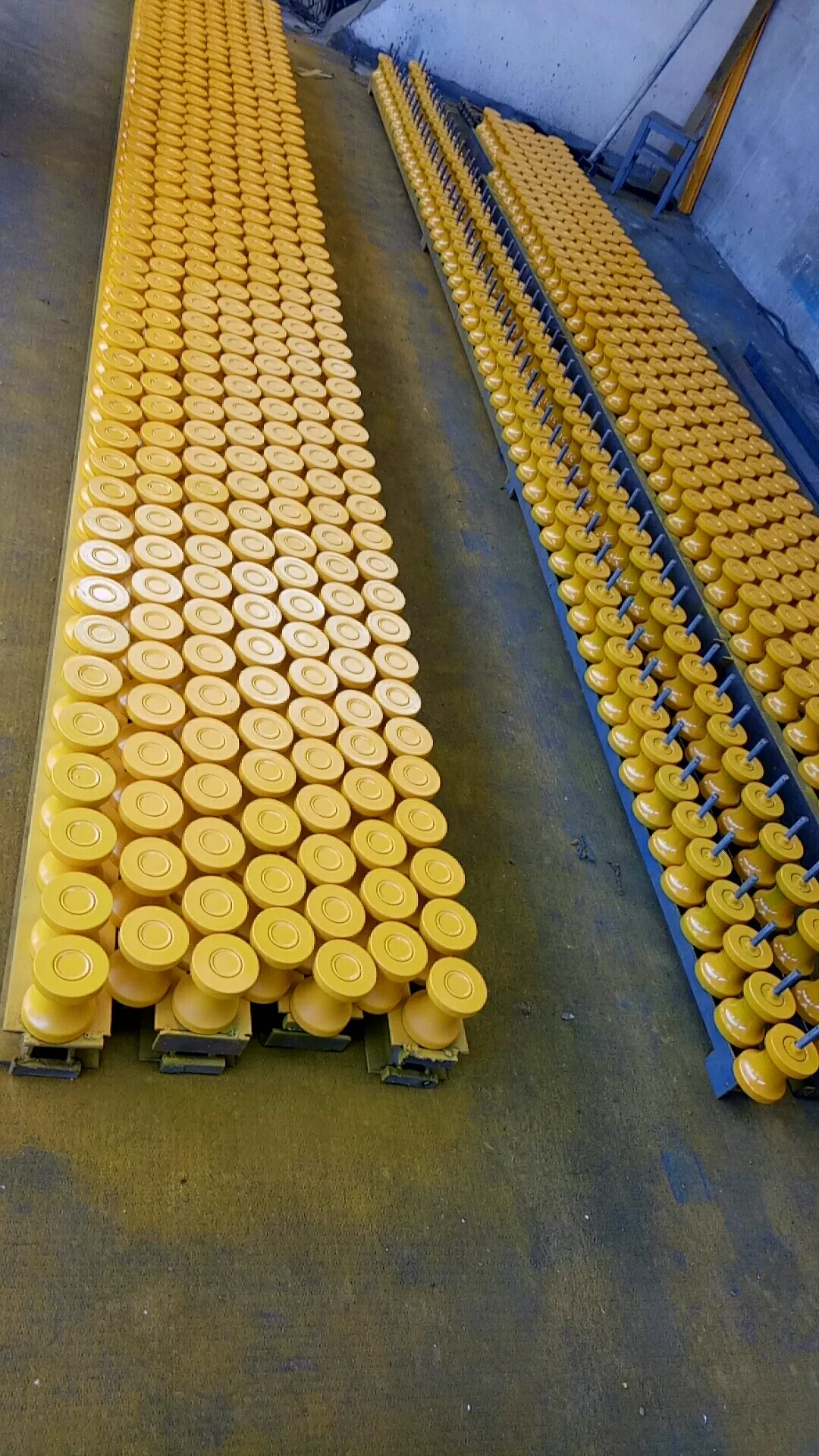
Concave guide rollers, as the name implies, are cylindrical tools featuring a curved or concave surface. This unique design enables them to efficiently accommodate and guide materials, particularly those that are tubular or cylindrical in nature. One of the primary advantages of using concave guide rollers is their ability to control lateral movement of material, ensuring stability and precision in operations such as conveyor systems, textile manufacturing, and web handling.
Professional experience with concave guide rollers reveals their effectiveness in reducing wear and tear on materials. This capability arises from their contact optimization—the concave shape offers a better distribution of stress along the material’s surface. This advantage not only prolongs the life of the materials but also enhances the longevity of the equipment itself. Over time, this contributes to decreased maintenance costs and increased operational efficiency, a benefit well-documented by seasoned engineers and equipment managers.
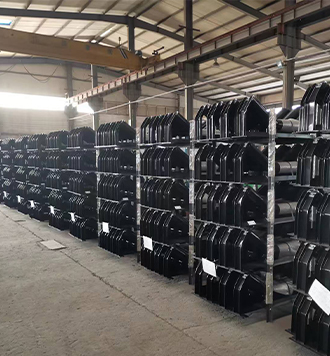
From an expertise standpoint, selecting the right concave guide roller requires a nuanced understanding of material properties and operational demands. Material composition of the roller, for instance, affects its function significantly. High-grade steel rollers are preferable for environments necessitating robust endurance and resistance to abrasion, whereas lighter materials like aluminum might be ideal for applications where weight reduction is paramount. In specialized contexts, such as those involving corrosive substances, rollers composed of chemically resistant composites are essential. Thus, industry professionals must evaluate these factors meticulously to ensure optimal performance and durability.
Concave guide rollers also possess a notable authority within their sphere of application. The precision of these rollers is pivotal in systems like conveyor belts used in the logistics sector, where seamless and accurate operation is crucial. Their ability to align and guide materials prevents mishaps that could disrupt operations or result in costly material losses. Here, the authority of concave guide rollers as reliable components becomes evident, emphasizing their integral role in productivity and quality control measures.
concave guide roller
Trustworthiness in concave guide rollers stems from their proven track record in diverse industrial applications. Industries spanning automotive manufacturing to food processing have relied on these rollers to deliver consistent performance. Trust is further enhanced when these rollers are designed and manufactured by reputable companies known for rigorous quality standards and adherence to international manufacturing guidelines.
Real-world application experiences often highlight the flexibility of concave guide rollers. For instance, in the packaging industry, these rollers skillfully handle a breadth of materials, from delicate films to heavier corrugated sheets, without compromising on speed or precision. Their adaptability is also evident in textile production lines, where they prevent fabric tears and maintain alignment under rapid motion conditions. Testimonials from field engineers frequently cite the reduction in material waste and process downtime as critical benefits attributable to these rollers, reinforcing their value proposition in high-stakes environments.
A detailed exploration of concave guide rollers reveals their quintessential nature in modern manufacturing and material handling. Their design, grounded in engineering expertise, affords them a dominant position in ensuring material integrity and operational precision. Furthermore, their widespread acceptance and reliance among industry professionals underscore their credibility and authority.
In sum, the concave guide roller serves as an unsung hero in the efficient and precise running of complex systems. Selecting and implementing these components calls for a detailed understanding backed by professional expertise, ensuring they meet the stringent demands placed upon them in various industrial applications. Their continued relevance lies in their ability to evolve with technological advancements, exemplifying the commitment of industries to forge ahead with systems that are both efficient and sustainable.