Conveyor idlers are critical components of conveyor systems, offering the necessary support for the conveyor belt and facilitating smooth operations by minimizing belt friction. Optimal conveyor system performance hinges on selecting the correct conveyor idler specifications, underscoring their importance in maintaining operational efficiency and extending equipment lifespan.
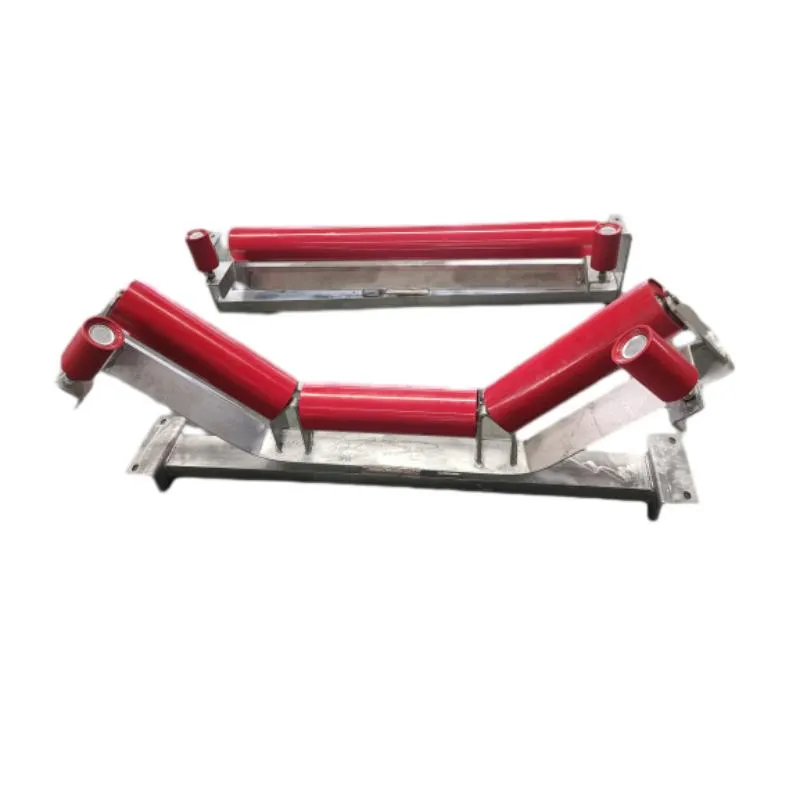
When selecting conveyor idlers, considerations should include understanding the specific needs of the application. Conveyor idlers come in various sizes and designs, each tailored to different requirements. The size and width of the belt, the load it needs to support, and the nature of the material being transported are crucial factors. Idlers must be able to accommodate the weight and volume of the material, ensuring consistent and even load distribution, which prevents premature wear on the belts.
Roll diameter is another key specification to consider. Larger diameters are often employed for heavy materials, as they provide additional strength and reduce the likelihood of belt sagging. Smaller diameters are more suitable for light materials and offer increased flexibility. Bearing type and quality within the idler also contribute significantly to its durability and efficiency. High-quality sealed bearings are often preferable, as they provide smooth rotation and minimize maintenance needs by being resistant to dust and moisture ingress.
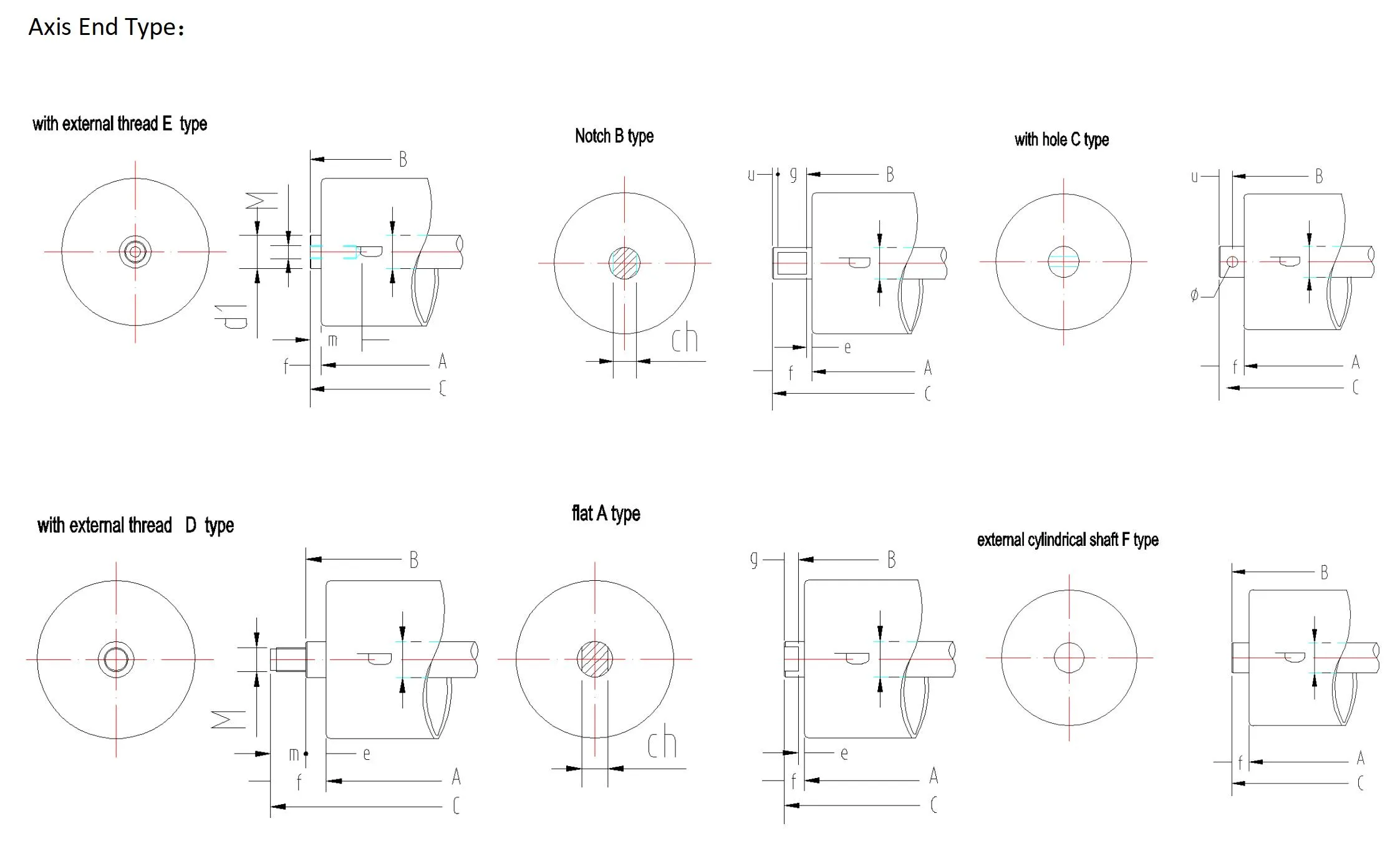
The spacing between idlers can significantly impact the conveyor's performance. Incorrect spacing can lead to increased power consumption and decreased motor efficiency. Recommended spacing often relies on the belt’s characteristics and the operational conditions. Closer spacing may be needed for heavier loads to distribute weight more uniformly across the conveyor structure, whereas lighter materials might allow for greater idler spacing, which can reduce costs while maintaining efficiency.
conveyor idler specifications
Material and environmental conditions play pivotal roles in idler selection. Materials susceptible to corrosion or those used in outdoor operations may require idlers with specific coatings or made from corrosion-resistant materials like galvanized steel or plastic. In extremely high or low temperature environments, choosing idler systems that can withstand these conditions without deformation or reduced performance is crucial.
Moreover, noise levels are an often-overlooked aspect of idler specifications. Noise reduction can be essential in industries sensitive to sound pollution. Selecting idlers with precision bearings and appropriate materials helps curtail operational noise, creating more pleasant and safer work environments.
To ensure these systems remain reliable, periodic inspection and maintenance are necessary. Regularly checking for signs of wear, such as unusual noise or wobbling in the idlers, can preempt costly downtime. Implementing these maintenance routines is part of good practice in managing conveyor systems effectively.
In summary, understanding conveyor idler specifications requires a comprehensive consideration of several interrelated factors from an expert perspective. Each aspect, from size and bearing type to material compatibility and environmental condition, is a complex decision that impacts the operational efficiency and longevity of a conveyor system. Professionals tasked with selecting these components should leverage their expertise to make informed decisions, ensuring each specification aligns with the operational demands and enhances the overall system's performance. Prioritizing quality and precision during selection not only maximizes efficiency but also reinforces trust in your operation’s reliability.