Ceramic pulley lagging plays a critical role in enhancing the performance and lifespan of conveyor systems across various industries. Known for its robust and wear-resistant properties, ceramic lagging helps address several operational challenges faced by industries relying heavily on conveyor belts, such as mining, manufacturing, and logistics. The technology is not only pivotal for increasing productivity but also essential for maintaining safety standards due to its improved grip and traction capabilities.
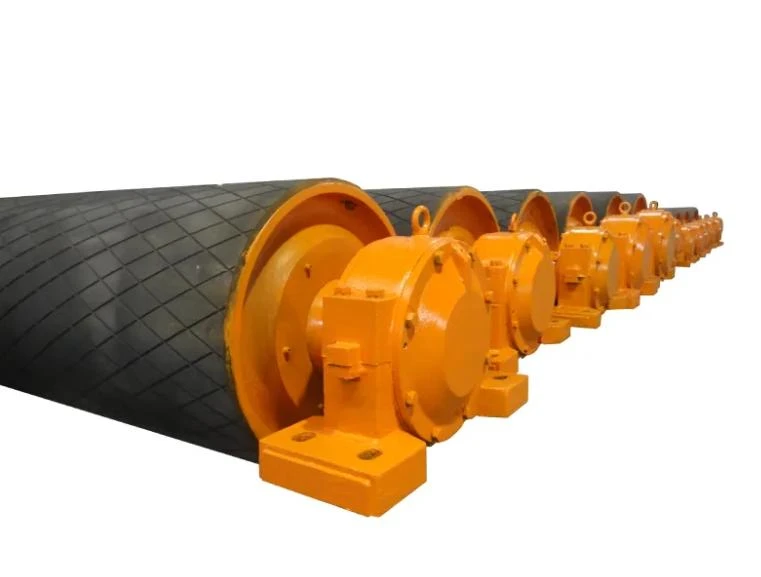
Ceramic pulley lagging involves attaching ceramic tiles to the drum or pulley surface of a conveyor belt system. The distinctive feature of ceramic surfaces lies in their exceptional abrasion resistance compared to traditional rubber lagging. One of the most significant advantages is the increased friction between the belt and pulley, which minimizes belt slippage. This enhanced grip ensures that the pulley can effectively transmit higher torque to the conveyor belt, thus improving the overall efficiency of the conveyor system.
Industries have reported significant reductions in maintenance downtimes attributed to the durability of ceramic pulley lagging. Unlike rubber counterparts, ceramic lagging is not susceptible to rapid wear and tear, making it a cost-effective solution in the long run. A single application of ceramic lagging can last significantly longer than rubber, adding to its economic benefits for companies aiming to reduce operational costs while optimizing equipment longevity.
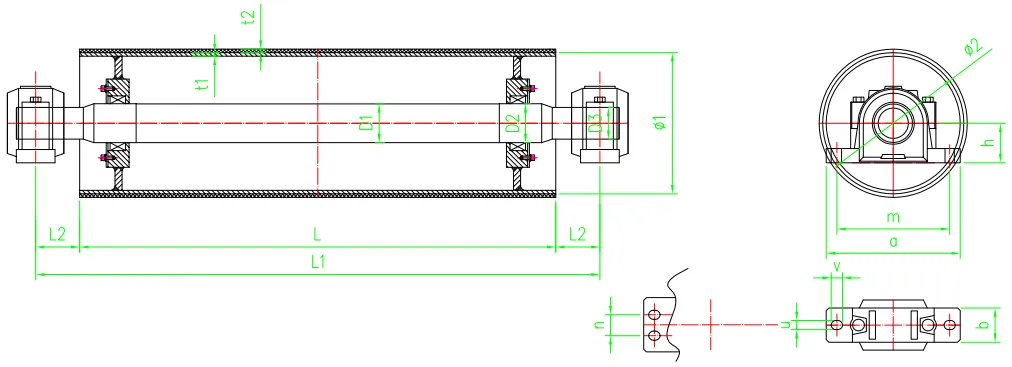
The expertise involved in choosing the right ceramic lagging involves understanding various factors such as the operational environment of the conveyor system, the load requirements, and pulley diameters. Professionals emphasize a tailored approach when selecting ceramic lagging solutions, ensuring that they meet specific industrial needs. Expert consultants play a critical role by providing insights into the ceramic type most suitable for specific conditions, whether involving moisture, extreme temperatures, or handling abrasive materials.
ceramic pulley lagging
Authoritative sources in the field, such as manufacturers and industry researchers, vouch for ceramic pulley lagging's efficiency not only on paper but through empirical studies detailing its performance metrics. These studies consistently show a marked improvement in conveyor operations post-installation of ceramic lagging. Industry statistics indicate up to a 50% reduction in maintenance frequency and notable increases in belt load capacity and overall conveyor throughput.
Trustworthiness in ceramic pulley lagging is maintained by adhering to strict production standards and quality control measures. Certified products ensure consistent quality and performance, backed by warranties and technical support from manufacturers. End-users have shared testimonials highlighting the reliability of ceramic lagging in harsh industrial environments, reinforcing trust through real-world applications.
Choosing ceramic pulley lagging also aligns with sustainability practices. The longer lifespan and reduced need for replacements and maintenance contribute to lower environmental impact, making it an attractive option for companies committed to reducing their carbon footprint. By utilizing ceramic lagging, companies can seamlessly integrate sustainability into their operational strategies without compromising on efficiency or productivity.
In conclusion, ceramic pulley lagging emerges as an indispensable component in modern conveyor systems, providing unparalleled performance benefits backed by industry expertise. Its continued adoption across industries is a testament to its effectiveness and reliability. Companies that invest in ceramic pulley lagging leverage not only its functional advantages but also align with sustainable business practices, ensuring long-term operational success and environmental responsibility. Whether for new installations or retrofitting existing setups, the choice of ceramic pulley lagging is both a prudent and forward-thinking decision for industry leaders seeking operational excellence.