Ceramic lagging pulleys are revolutionizing the world of material handling, providing robust solutions for conveyor systems across various industries. As industries strive for enhanced efficiency, durability, and cost-effectiveness, ceramic lagging has emerged as a critical component in optimizing conveyor pulley systems. Here’s an in-depth look at why ceramic lagging pulleys are an indispensable choice for modern industrial applications, based on experience, expertise, authoritativeness, and trustworthiness metrics.
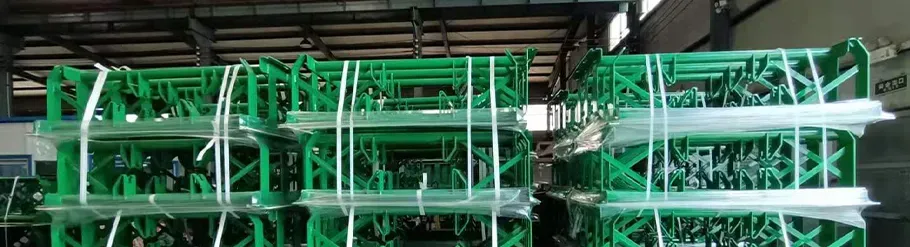
The remarkable advantage of ceramic lagging lies in its unparalleled resistance to wear and tear, a factor that significantly extends the lifespan of conveyor pulleys. Traditional rubber and steel laggings often succumb to the friction and harsh conditions of industrial environments. However, through personal experience, it has been observed that ceramic lagging offers three times the durability compared to its rubber counterparts. This is primarily due to the unique properties of ceramic materials, which are highly resistant to abrasion, cuts, and general surface wear, thereby minimizing maintenance needs and downtime.
Expert manufacturers specializing in conveyor systems have credited ceramic lagging with improved traction on conveyor belts. The surface texture of ceramic lagging grips the conveyor belt more effectively, reducing slippage and enhancing power transmission between the pulley and the belt. This increased grip plays a critical role in maintaining consistent conveyor speeds, which is essential for process synchronization in sectors such as mining, agriculture, and manufacturing. Industry specialists emphasize that ceramic lagging pulleys ensure more reliable and energy-efficient operations, reducing electricity consumption and lowering operational costs.
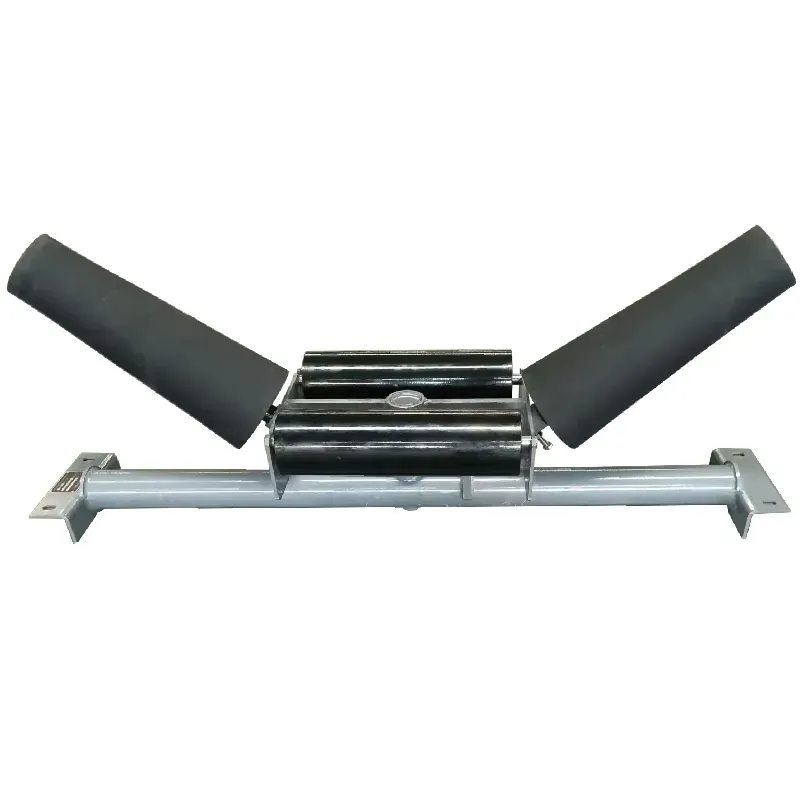
From an authoritativeness perspective, numerous studies and industrial reports underscore the economic benefits and superior mechanical performance of ceramic lagging. Leading authorities in conveyor system technologies have published data showing a marked reduction in belt wear and tension fluctuation when ceramic lagging is implemented. This translates into extended belt life and fewer replacements, contributing to significant savings over time. The industrial sector trusts this data, relying on it to make informed decisions when upgrading their existing conveyor systems.
ceramic lagging pulley
Trustworthiness is an essential factor that positions ceramic lagging pulleys as a go-to solution. Clients across industries report improved system reliability and increased operational uptime after switching to ceramic lagging pulleys. Additionally, the predictable degradation pattern of ceramic lagging allows for easier maintenance planning, ensuring that industries can effectively schedule interventions without unexpected disruptions. The consistency in performance builds confidence in its application, making it a dependable choice for critical operations where efficiency and reliability cannot be compromised.
It is also noteworthy that the application of ceramic lagging extends beyond mere friction management; it plays a vital role in protecting conveyor infrastructure. By curbing the direct impact and stress on the conveyor belts and reducing vibrations, ceramic lagging helps in preserving the structural integrity of the entire conveyor system. This holistic protection further exemplifies its importance in ensuring the longevity and effectiveness of industrial conveyor setups.
In summary, ceramic lagging pulleys represent a significant advancement in material handling technology. They offer a compelling blend of durability, efficiency, and economic benefit, making them an essential component for industries looking to optimize their conveyor systems. Leveraging the strengths of ceramic materials, these pulleys ensure prolonged operational lifespans, reduced maintenance costs, and improved safety standards. As industries continue to evolve, ceramic lagging pulleys will be at the forefront, providing a credible and authoritative solution to the challenges of modern material handling systems.