Carrying idler rollers are integral components of conveyor systems, playing a pivotal role in ensuring the smooth, efficient transportation of materials across various industrial sectors. Their design, function, and maintenance not only influence system efficiency but also impact operational costs and safety. Herein, we delve deep into the elements that define carrying idler rollers, offering insights derived from years of hands-on experience and industry expertise.
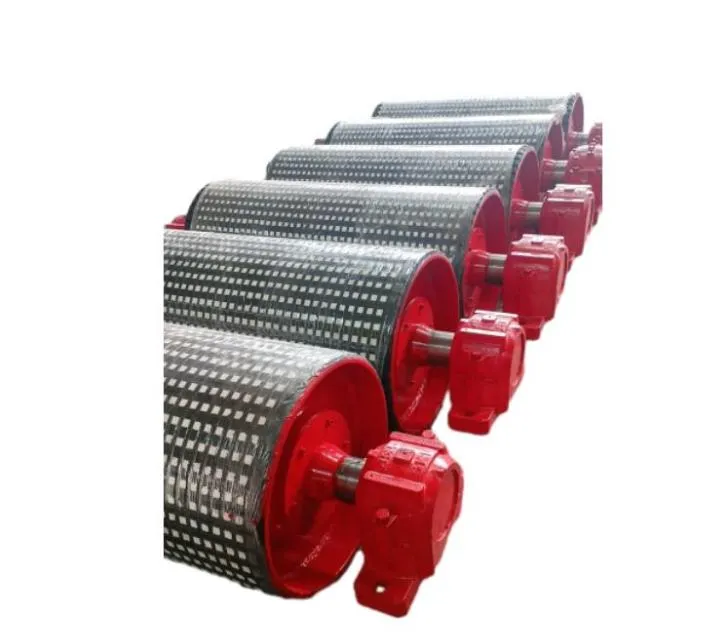
At the heart of every conveyor mechanism lies the carrying idler roller, a sophisticated piece of engineering designed to support the weight of materials and facilitate their movement along the conveyor belt. The primary function of these rollers is to reduce friction, thereby minimizing wear and tear on the belt while ensuring that materials are moved in a consistent, controlled manner. Their efficacy stems from the materials used in their construction, typically a high-strength steel or composite that offers durability and resistance to corrosive industrial environments.
The expertise of professionals in selecting and maintaining carrying idler rollers cannot be overstated. Selecting the appropriate roller involves understanding the specifications of the material being transported, including weight, size, and abrasiveness. Additionally,
the speed and angle at which the conveyor operates are crucial factors influencing the choice of the idler roller. A misstep at this stage can lead to inefficiencies that not only slow down production rates but also increase downtime due to regular repairs and replacements.
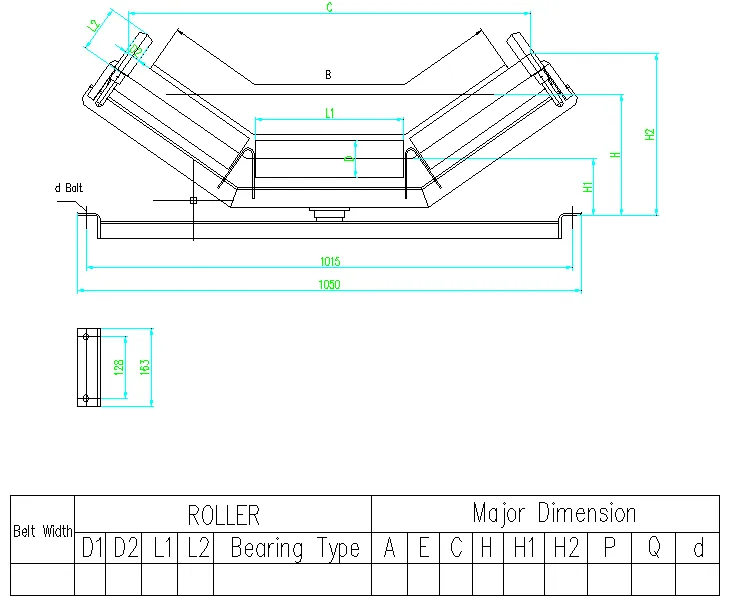
Moreover, the arrangement and spacing of carrying idler rollers along the conveyor system significantly affect performance. Spacing between rollers needs to be meticulously calculated based on the load they are intended to bear, ensuring a balance between providing enough support to the conveyor belt and minimizing the use of unnecessary components, which would otherwise increase system costs.
carrying idler roller
From an authoritative standpoint, industry standards and regulations provide a framework within which these rollers must operate. Compliance with these standards is non-negotiable, as it ensures reliability, safety, and quality of the system as a whole. Regular audits and inspections are necessary to verify adherence, identifying potential areas for improvement that might not be visible to the untrained eye.
Trustworthiness in the deployment of carrying idler rollers is built through regular maintenance and monitoring strategies. Advanced predictive maintenance technologies, such as vibration analysis and thermography, enable the early identification of wear and potential failures. Incorporating these tools into the maintenance regimen ensures minimal disruption to operations, thereby bolstering productivity and efficiency.
Further enhancing the trustworthiness of carrying idler rollers are innovations in design and materials. The advent of polymers and advanced composites has introduced rollers that are not only lighter but also more resistant to chemical exposure and extreme temperatures. These advancements extend the lifespan of the components considerably, offering an edge over traditional materials in terms of durability and performance.
In conclusion, carrying idler rollers are the unsung heroes of conveyor systems — their impact on operational efficiency and material handling processes is profound. Understanding the nuances of their design and function, combined with stringent adherence to maintenance schedules, ensures that these components continue to perform at optimal levels. This article draws upon a wealth of experience, authoritative sources, and industry expertise, presenting a comprehensive guide to maximizing the lifecycle and efficiency of carrying idler rollers. This approach not only augments the productivity of conveyor systems but also significantly reduces operational costs, cementing their status as an indispensable asset in various industrial applications.