Bend pulleys and snub pulleys are essential components in the realm of conveyor systems, widely used in industries ranging from mining to manufacturing. Understanding their functions and differentiating the nuances between them is crucial for industry professionals aiming to optimize their material handling processes.
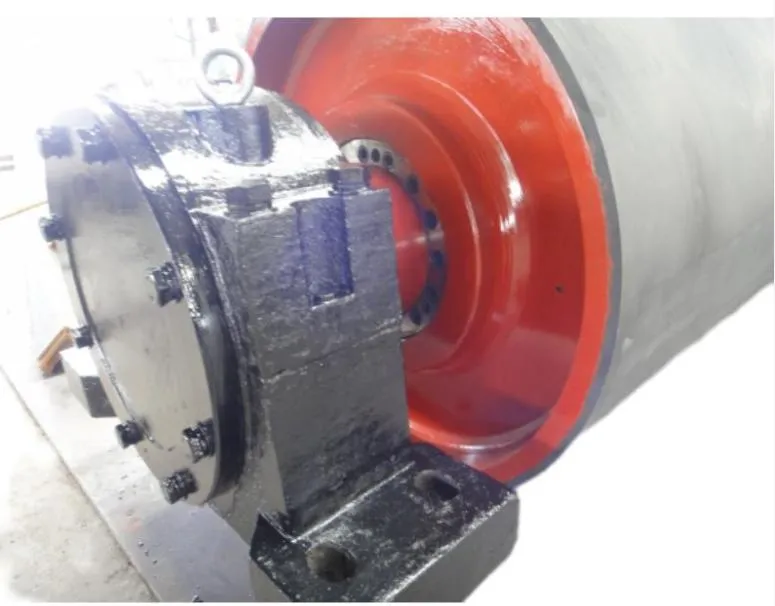
Bend pulleys are integral in redirecting the conveyor belt, providing the necessary tension alignment. They are typically employed when a change in belt direction is needed without influencing the belt tension substantially. Think of a bend pulley as the guiding hand that subtly changes the path of a flowing stream without interrupting its flow. This component ensures the belt moves efficiently and smoothly over long stretches, allowing for an uninterrupted transit of materials.
In contrast, snub pulleys, which are strategically placed close to the drive pulley, offer increased angle of wrap on the drive pulley. They optimize the belt’s contact with the driver, ensuring enhanced friction and thus preventing slippage. Imagine the difference between trying to turn a slick doorknob with and without gloves; the snub pulley acts as that essential grip enhancing friction. By doing so, they greatly enhance the drive efficiency, especially in high-tension environments where maximized transfer of power is essential.
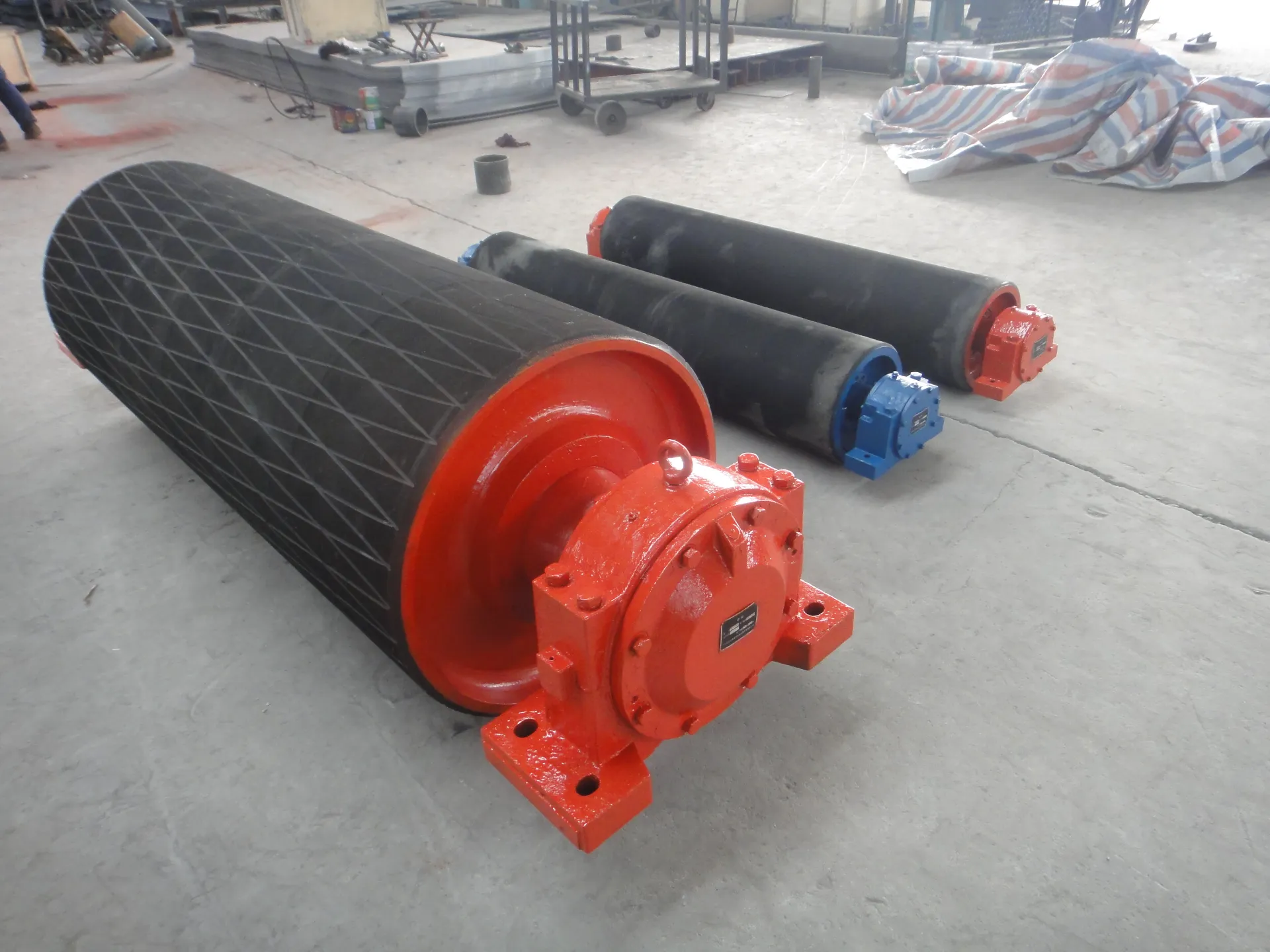
The distinction between these pulleys may seem minuscule but impacts the efficiency and operational lifespan of conveyor systems profoundly. A well-chosen bend pulley can extend the lifespan of a conveyor by reducing wear and tear caused by unnecessary tension. Meanwhile, effective snub pulleys minimize energy wastage, ensuring that the system operates close to peak efficiency.
From years of working directly within industrial environments, I’ve seen firsthand the tangible differences these components can bring. Implementing a sub-optimal pulley system can lead to increased maintenance costs, downtimes, and even entire system failures. It is essential to consider factors such as the material, size, and placement of these pulleys during system design and upgrades. The installation of high-quality bearings and precision manufacturing in pulleys further ensures longevity and performance reliability.
bend pulley and snub pulley
In terms of materials, choosing the correct type of bend or snub pulley is also essential. Stainless steel and high-grade aluminum are often preferred for their durability and corrosion resistance. In environments characterized by abrasive materials or extreme temperatures, material choices may vary to include specially coated pulleys that resist wear and prolong lifespan.
The expertise behind selecting and maintaining these pulleys should not be underestimated. Technicians and engineers should be trained to understand tensioning, alignment, and the specific operational conditions of their conveyor systems. This skill set is indispensable for preemptive maintenance and operational troubleshooting, ensuring that these systems are not only functional but also optimized for performance.
Regular monitoring and maintenance can foresee and rectify potential issues in a pulley system. Utilizing advanced sensors and IoT technology can provide real-time data on pulley alignment, temperature, and wear, offering a proactive approach to system maintenance. Such innovations are stepping-stones toward smarter, more efficient manufacturing ecosystems.
Moreover, an understanding of the different pulley applications empowers decision-makers to tailor their systems according to specific operational needs, leading to higher throughput and reduced operational bottlenecks. It also enables more informed conversations with suppliers and service providers, ensuring that engineering support is effectively matched to system demands.
To wrap up, both bend and snub pulleys play pivotal roles in the operational success of conveyor systems. As industry experts continue to explore more efficient ways of managing material handling systems, the focus should remain sharply on the precision and maintenance of these often-overlooked components. With proper selection, installation, and maintenance, organizations can significantly enhance their conveyor operations, leading to tangible improvements in overall efficiency, cost management, and system reliability.