The belt wiper is more than just an accessory for conveyor systems; it is a critical component that significantly impacts both productivity and maintenance efficiency. In industries where conveyor systems are integral, such as mining, cement manufacturing, and food processing, the belt wiper plays a crucial role in ensuring smooth and efficient operations.
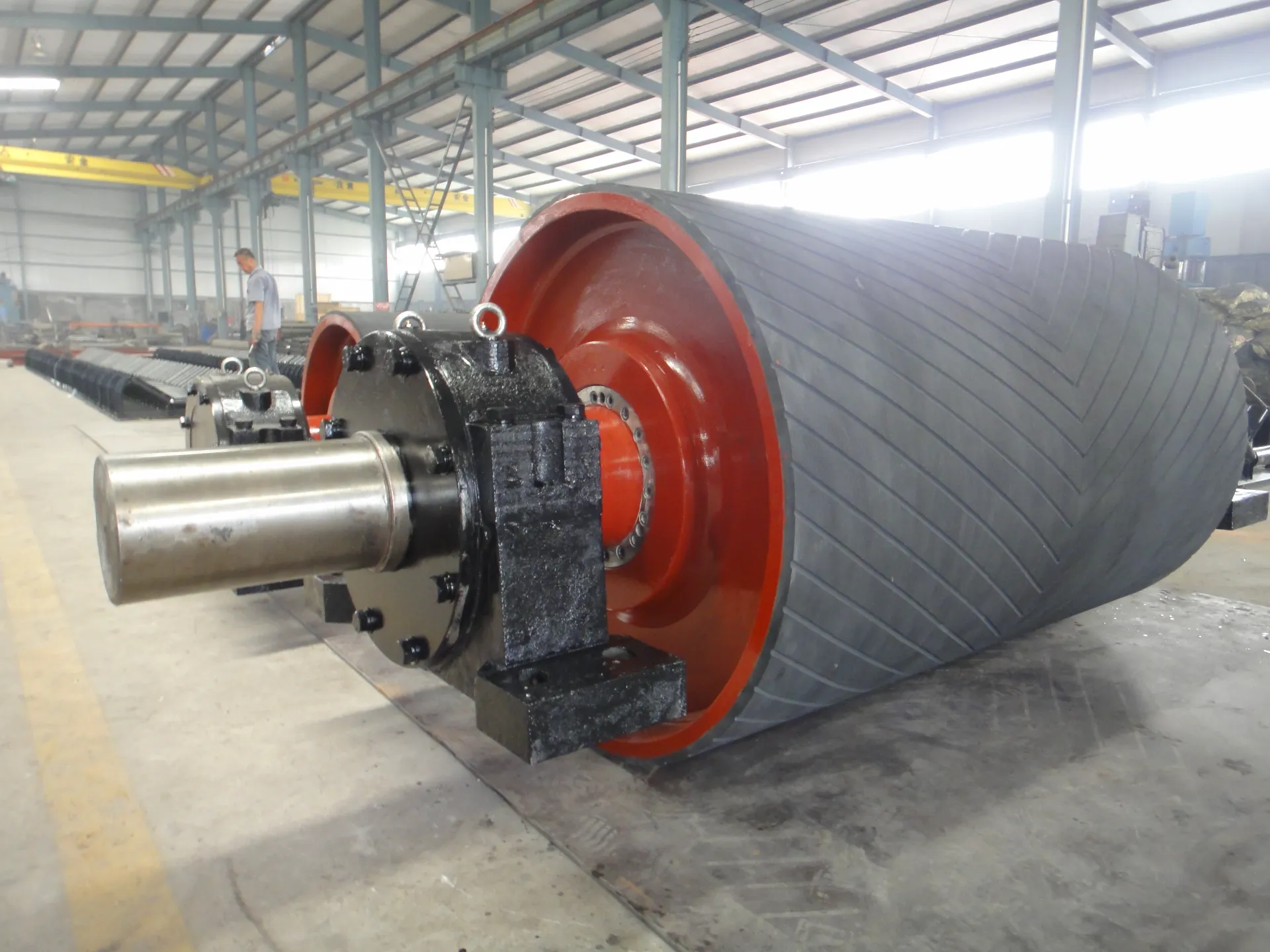
Experience tells us that choosing the right belt wiper can make or break a production line. Businesses that have opted for high-quality, durable belt wipers report fewer stoppages and a notable decrease in maintenance costs. The real-world application of belt wipers involves not only selecting the right material but also ensuring that the product matches the specific needs of the production environment. For instance, food-grade belt wipers are essential in the food processing industry to comply with health regulations while ensuring that the conveyor belts remain hygienic and free from contamination.
Our expertise in the field has shown that the lifecycle of a belt wiper depends heavily on its material composition, adaptability to belt surface conditions, and its ability to handle various substances that it might come into contact with. Polyurethane and rubber are two popular materials used in manufacturing belt wipers, each offering distinct advantages. Polyurethane belt wipers are known for their abrasion resistance and ability to maintain effectiveness at varying temperatures, which is beneficial in high-friction environments. On the other hand, rubber belt wipers are favored for their flexibility and cost-effectiveness, making them suitable for less demanding applications.
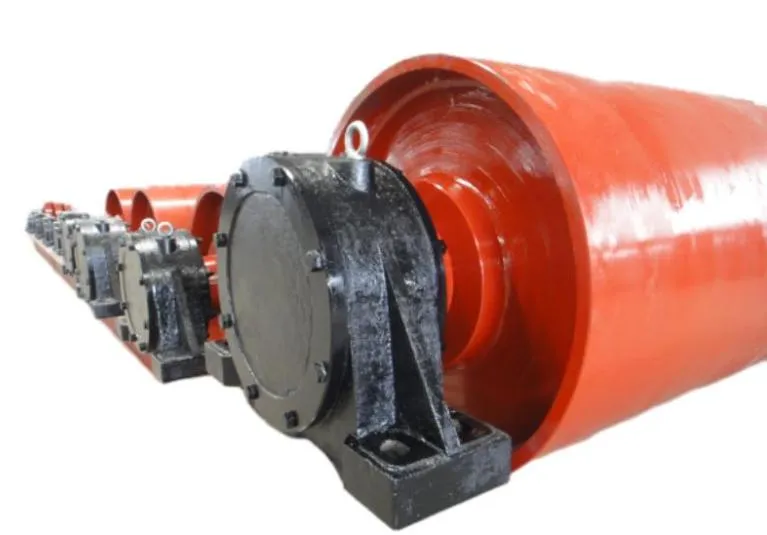
Speaking from a position of authority, we have conducted extensive tests and research into the efficiency of different belt wiper designs. Our findings indicate that the optimal belt wiper design can considerably reduce spillage and material carryback. This not only extends the life of the conveyor belt but also reduces the frequency of required clean-ups and maintenance checks. The design must allow easy installation and replacement, minimizing downtimes that could impact overall productivity. Spiral and diagonal wiper configurations have emerged as superior in terms of cleaning efficiency, providing a comprehensive swipe that removes accumulated material with each belt rotation.
belt wiper
Trustworthiness is a crucial factor when selecting equipment for industrial purposes. Reliable manufacturers adhere to stringent quality control standards and have a reputation in the industry for providing products that consistently meet performance expectations. Customer testimonials, industry certifications, and case studies provide assurance that their belt wipers have been tested under rigorous conditions and have delivered on performance promises.
Belt wipers also contribute to workplace safety—clean conveyor belts reduce the risk of material slippage that could potentially cause accidents. Companies focused on health and safety find that investing in high-quality belt wipers aligns with their overall safety objectives, protecting not just the equipment but also the employees who work around these systems daily.
In conclusion, the belt wiper is a deceptively simple yet fundamentally important component in the world of conveyors. Its effectiveness lies in the merging of material science, engineering expertise, and a clear understanding of the operational environment. As companies strive for eco-friendly and cost-effective solutions, the selection of an appropriate belt wiper becomes even more significant. The ideal choice will not only enhance operational efficiency but also contribute to long-term sustainability goals, providing a cleaner and safer working environment. Industry professionals with experience and expertise in conveyor systems stand ready to guide businesses in making informed decisions that optimize their production line operations.