Belt idler rollers are critical components in bulk material handling systems and conveyor belt designs. Widely used in industries such as mining, quarrying, and manufacturing, these rollers contribute significantly to the smooth operation of conveyor belts by maintaining belt tension and aligning the system to prevent spillage and belt drift. This article provides a comprehensive exploration of belt idler rollers, offering expert insights and experiences to guide industry professionals and purchasers in making informed decisions.
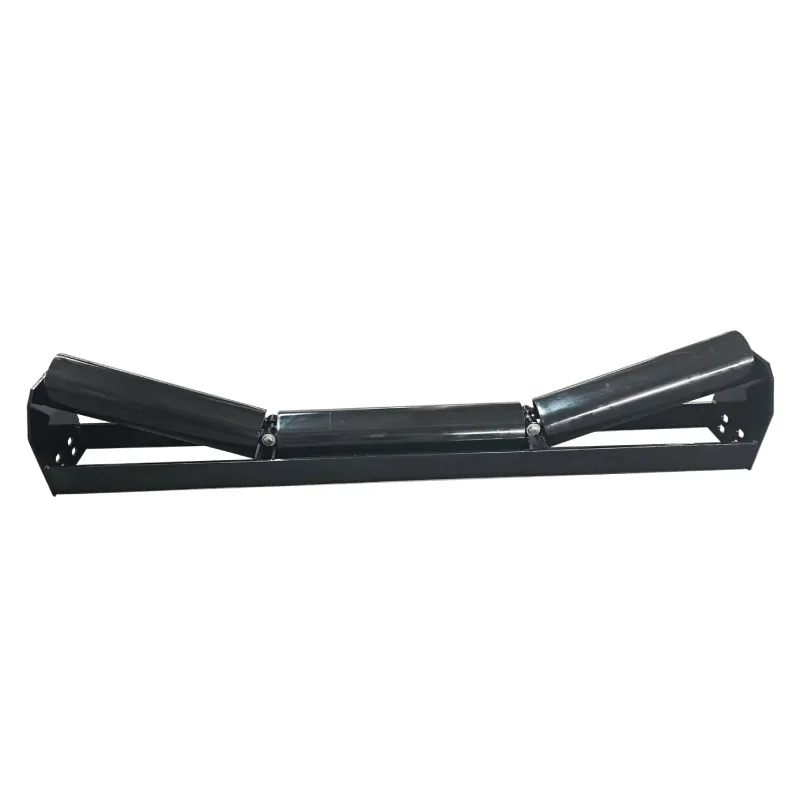
The operation of belt idler rollers essentially involves supporting the conveyor belt and the load conveyed. Typically crafted from high-grade materials like steel or plastic, these rollers are designed to withstand substantial loads and harsh environmental conditions. Selecting the right material is crucial, as it affects the roller's durability and service life. Steel idler rollers, for instance, provide superior strength and are preferred in heavy-duty applications, whereas plastic rollers are more appropriate for lightweight conveyor systems prone to static charge issues.
From a technical standpoint, the design features of belt idler rollers, such as their diameter, length, and bearing configurations, profoundly impact their performance. A larger diameter roller often results in reduced rotational speed, prolonging the lifespan of the bearings. Furthermore, effective bearing seals are paramount in safeguarding the rollers from contaminants like dust, water, and chemicals, thus preventing premature failure.
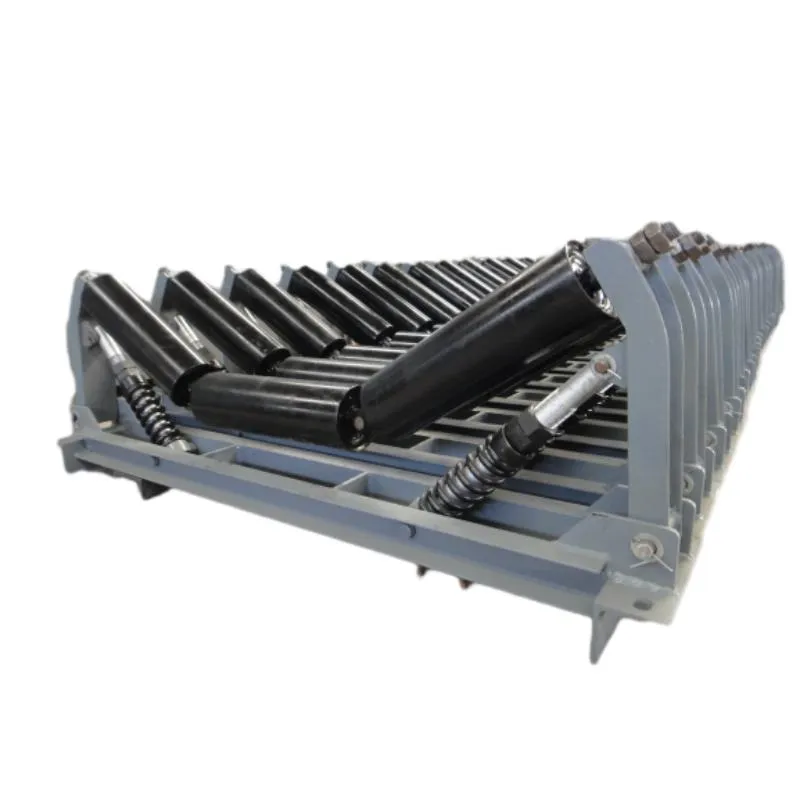
The placement and configuration of idler rollers within a conveyor system are also determinant factors of their effectiveness. Troughing idlers, commonly composed of three rollers arranged in a 'V' shape, are used to shape the belt into a trough, increasing the load capacity. Return idlers, on the other hand, are positioned on the underside of the conveyor to support the returning belt. Proper alignment and spacing of these rollers help mitigate belt stress and minimize maintenance issues.
belt idler roller
Real-world experience underscores the importance of regular maintenance and timely replacement of belt idler rollers to maintain optimal conveyor performance and prevent unexpected downtime. Routine inspections focusing on wear and tear, bearing conditions, and alignment issues can vastly extend the lifespan of the rollers. Moreover, using advanced tools such as vibration analysis and infrared thermography to monitor roller conditions non-invasively has proven to be effective in many industrial settings.
When acquiring belt idler rollers, the credibility and authority of the manufacturer cannot be overstated. Reputable manufacturers often invest in research and development, incorporating the latest technological advancements to enhance the reliability and efficiency of their products. Consequently, seeking testimonials, industry certifications, and case studies can provide assurance of quality and performance. Furthermore, ISO certification from the manufacturer establishes confidence in their production processes and commitment to quality management standards.
Trustworthiness in belt idler rollers is also bolstered by the availability of after-sales service and support from manufacturers and suppliers. Comprehensive services such as installation guidance, technical support, and maintenance training reflect the manufacturer's dedication to ensuring their products deliver promised performance and reliability.
In conclusion, belt idler rollers may be relatively simple components in the broader scope of conveyor systems, but their contribution is indispensable. Industry professionals and procurement specialists should prioritize quality, design suitability, maintenance regimes, and manufacturer reputation when choosing idler rollers. By doing so, businesses stand to gain improved efficiency, reduced operational costs, and a sustained workflow, ultimately enhancing productivity and profitability in their respective operations.