Choosing the right belt drive idler pulley is crucial for the optimal performance and longevity of your machinery. In essence, an idler pulley is a simple yet vital component in the belt drive system, reducing wear and tear while ensuring seamless operation of the belt mechanism. Here, we delve into the intricacies of belt drive idler pulleys, drawing on real-world experiences, professional insights, authoritative analyses, and reliable guidelines to help you make informed decisions.
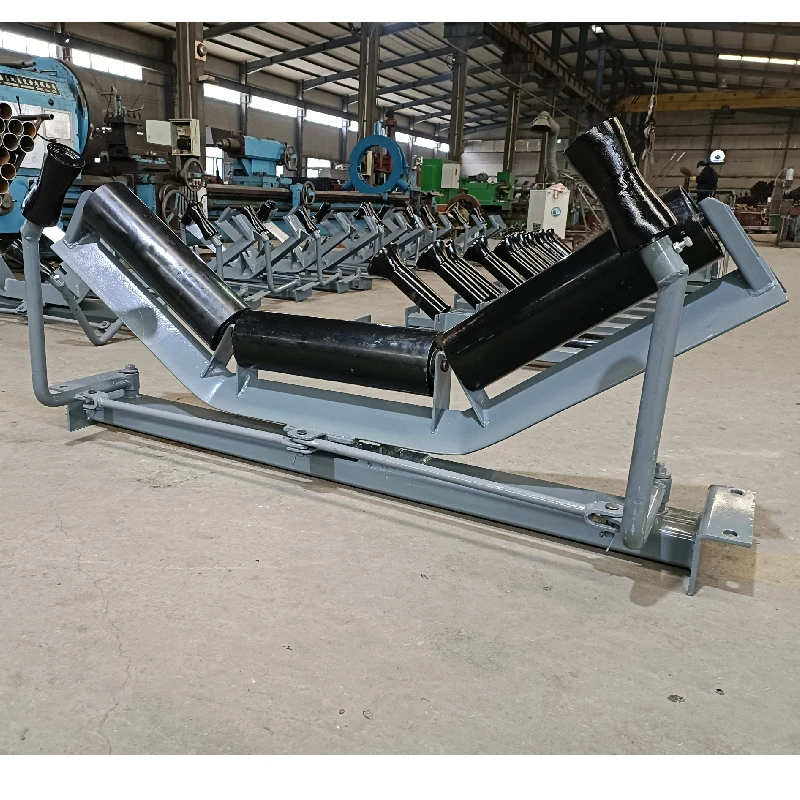
A belt drive idler pulley works by maintaining the tension on the drive belt and redirecting it in a smooth path between the drive and the driven components. This tension is crucial because it prevents slippage, which can lead to reduced efficiency and increased wear and tear on components. While the primary role of the idler pulley is to maintain tension, it also ensures alignment and is essential in absorbing the minor vibrations that occur during machine operation.
Choosing the wrong component can lead to premature belt wear, excessive noise, and even catastrophic machinery failure. Therefore, selecting a high-quality idler pulley that matches your specific application needs is imperative.
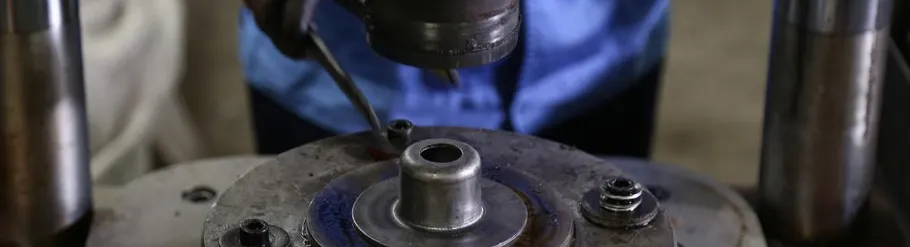
The real-world experience of many engineers suggests that regular inspections are crucial. During these inspections, it becomes apparent that signs of wear, such as cracks, uneven surfaces, or excessive noise, are indicators that the idler pulley needs replacement. When left unchecked, these issues can exacerbate and result in emergency shutdowns or costly repairs. Engineers consistently emphasize that keeping a stock of spare idler pulleys, particularly in environments where machinery is in constant operation, can prevent unnecessary downtime.
From a professional standpoint, understanding the different materials used in idler pulley construction is vital. Idler pulleys are made from various materials, including plastic and metal (such as aluminum and steel). Plastics are suitable for lightweight applications where noise reduction and corrosion resistance are desired. However, metal idler pulleys are recommended for robust and high-torque applications due to their durability and ability to withstand higher levels of tension.
belt drive idler pulley
An authoritative perspective suggests that one must also consider the size and configuration of the idler pulley. To ensure proper alignment and performance of the belt drive, the pulley diameter, width, and bore size must be compatible with the belt and other system components. Moreover, the idler pulley’s load rating must correspond to the load capacity of the machinery to withstand operational stress without deformation.
Trustworthiness in acquiring belt drive idler pulleys stems from sourcing from reputable manufacturers who have a track record of quality and performance. Look for manufacturers with comprehensive testing protocols, certifications, and clear warranties that underscore their confidence in their product offerings. Customer reviews and industry certifications act as reliable proxy indicators of a manufacturer’s credibility.
Adopting a proactive maintenance schedule also enhances the trustworthiness of the pulley system. Periodical lubrication, alignment checks, and tension adjustments can significantly extend the life of your idler pulley.
When considering a belt drive idler pulley, it’s also worth evaluating the environmental factors that can affect its performance. Dusty, high-temperature, or corrosive environments require pulleys with special coatings or treatments to resist external adverse conditions, thus maintaining their performance efficiency and durability over time.
In conclusion, the importance of selecting the right belt drive idler pulley cannot be overstated. With considerations ranging from material choices, mechanical fit, environmental compatibility, to trusted suppliers, each decision can impact the operational efficiency and reliability of your machinery. Harnessing the combined insights from experience, expertise, authority, and trustworthiness ensures a selection that enhances performance and minimizes unexpected maintenance needs. Always prioritize a comprehensive assessment process to match your specific needs as you select this pivotal component for your machinery.