Selecting the right type of belt conveyor roller is crucial for optimizing efficiency and longevity in industrial material handling systems. The success of these systems depends highly on the functionality and reliability of the rollers, which act as the backbone, maintaining smooth and consistent motion. Understanding the various types of rollers and their specific applications can significantly enhance operational effectiveness while reducing maintenance costs.
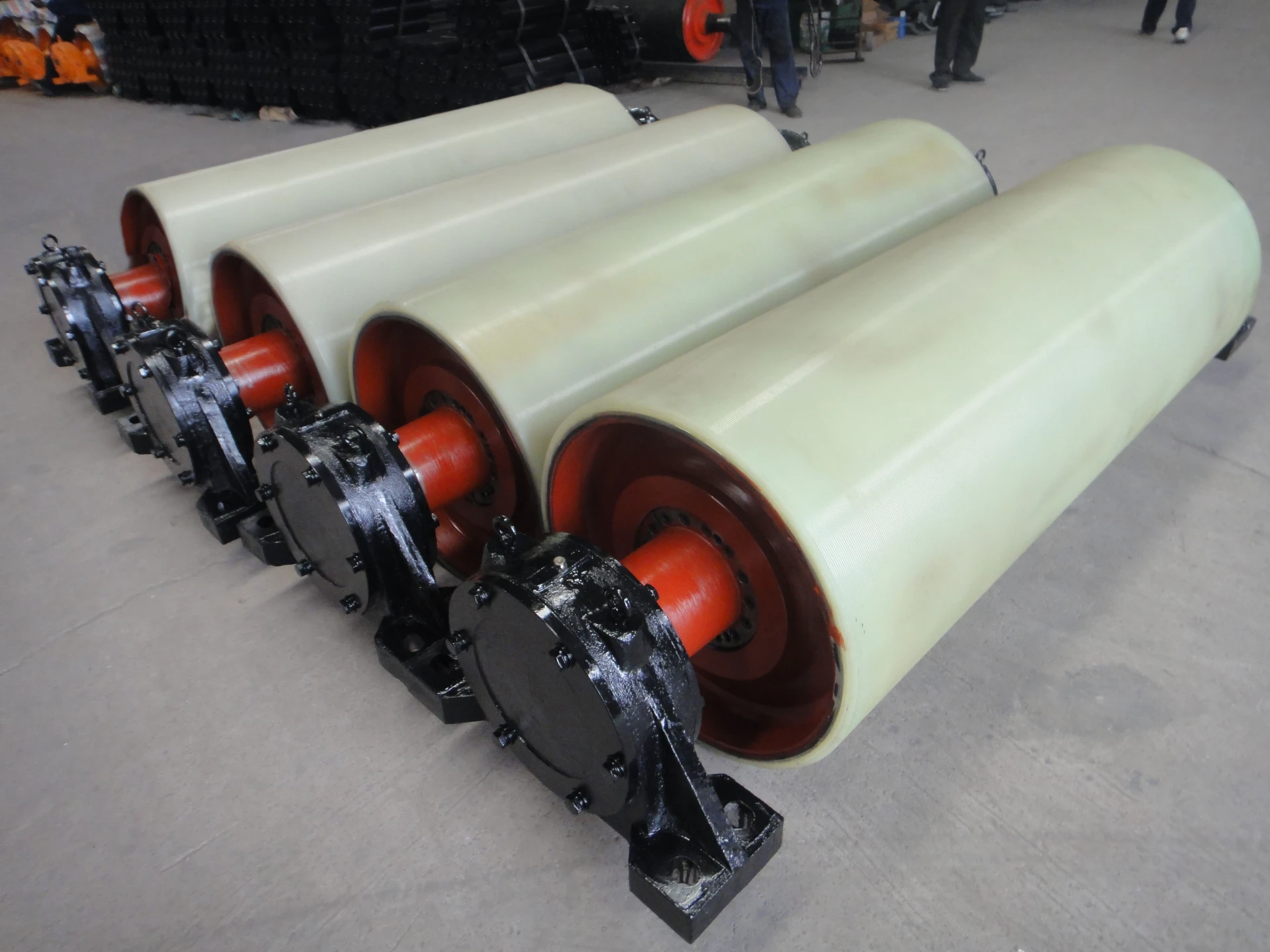
One of the primary types of belt conveyor rollers is the return roller, designed to support the returning conveyor belt under the system. These rollers ensure that the belt runs straight and true without excessive wear or deviation. They are particularly important in minimizing belt sagging, which can lead to premature wear and increased energy consumption. More advanced designs include self-cleaning return rollers, which prevent material buildup, thus maintaining belt alignment and reducing maintenance downtime.
Impact rollers, typically found at loading points, are designed to absorb the energy of falling materials. Constructed with rubber rings or discs, they provide a cushioning effect that mitigates damage to the belt and reduces noise levels. Their durability and shock-absorbing capabilities safeguard both the belt and the conveyed material, making them indispensable in high-impact zones.
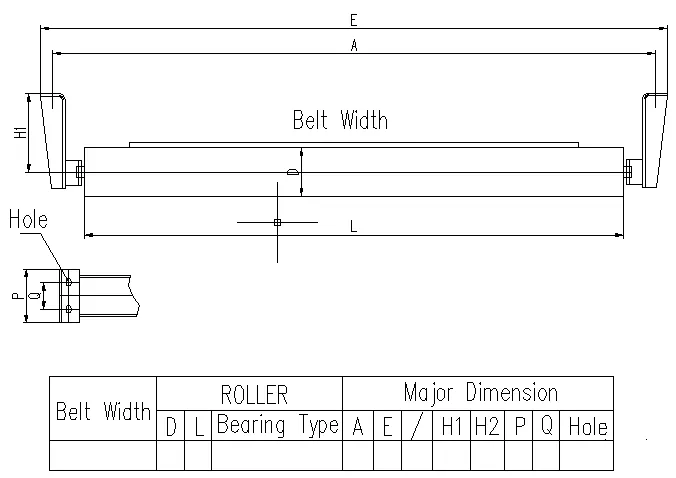
Guide rollers are another crucial type, instrumental in maintaining belt alignment. These rollers are essential in applications requiring precise belt positioning, ensuring the belt remains on course and preventing potential spillage. Properly aligned guide rollers minimize the risk of belt damage, reduce operational disruption, and extend the belts’ lifespan, offering a reliable solution for systems with frequent directional changes.
Troughing rollers, characterized by their angled arrangement, support the belt and the conveyed material in a trough shape. This design significantly improves the belt's ability to carry larger volumes of material with enhanced stability. They are commonly used in bulk material handling applications, where they contribute to maximizing capacity without compromising belt performance or safety.
belt conveyor roller types
In corrosive or chemically aggressive environments, selecting rollers made from specific materials, such as stainless steel or high-density polyethylene (HDPE), is imperative. These materials offer superior resistance to chemical exposure and corrosion, ensuring that the rollers maintain their structural integrity and performance over extended periods. HDPE rollers, in particular, are favored for their lightweight nature and ability to reduce energy consumption while offering excellent wear resistance.
Furthermore, to meet the demands of cutting-edge operational environments, incorporating rollers with advanced technological features, like embedded sensors, can provide real-time data monitoring. These smart rollers enable predictive maintenance, identifying potential issues before they escalate into costly failures. By integrating IoT solutions, operators gain insights into operational efficiency, allowing for proactive management and optimization of the conveyor system's performance.
When optimizing belt conveyor systems, it is imperative to collaborate with industry professionals possessing in-depth expertise in conveyor technology. Trustworthy suppliers provide guidance on selecting the appropriate roller type based on specific operational needs, focusing on performance, durability, and overall cost-effectiveness. A well-informed decision-making process results in seamless material handling operations, promoting sustainability and reliability.
As advancements in material technology and digital integration continue to evolve, the future of belt conveyor rollers will witness further innovations. From energy-efficient designs to smart rollers that communicate with central systems, the role of these components will continue to expand, enhancing the efficiency and responsiveness of modern conveyor systems. Therefore, staying informed and adaptable to these developments is crucial for maintaining a competitive edge in industrial material handling applications.
In conclusion,
selecting the right belt conveyor roller involves a comprehensive understanding of various types and their applications. Emphasizing the importance of experience, expertise, authoritativeness, and trustworthiness in decision-making processes ensures that conveyor systems deliver optimal performance and reliability. Properly chosen and maintained rollers are key to achieving efficient, cost-effective, and sustainable material handling solutions.