In manufacturing and industrial contexts, the belt conveyor roller often plays an unsung role critical to the efficiency of any material handling process. When we talk about conveyor systems, the conversation often circles around the more visible belts, motors, and frames. However, without the right rollers, the system's heart and soul, even the priciest belts can falter. The core strength of a belt conveyor lies in its expertly engineered rollers, which demand a deeper understanding of their attributes and functionality.
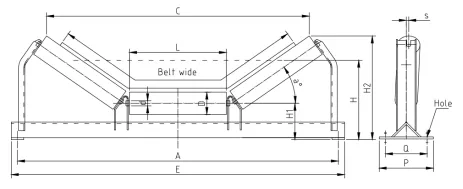
To begin with,
conveyor rollers are pivotal in ensuring the smooth operation of the conveyor system. They come in different forms and materials—this versatility allows them to cater to diverse industrial needs, be they heavy-load applications or chemical exposure. Each roller supports the belt, guiding it in an endless loop that is paramount for the transportation of goods. It is of utmost importance that these rollers are designed with precision, to minimize wear and resistance, which prolongs their lifespan and maintains the system's throughput.
The first consideration in making an informed decision about belt conveyor rollers is understanding the types available. Gravity rollers rely on gravity for movement, ideal for light to medium loads. Motorized rollers, on the other hand, incorporate a motor within the roller itself, allowing for direct power control that simplifies complex conveyor systems. These are frequently used in more sophisticated plants, providing precise control over the conveyor’s movement.
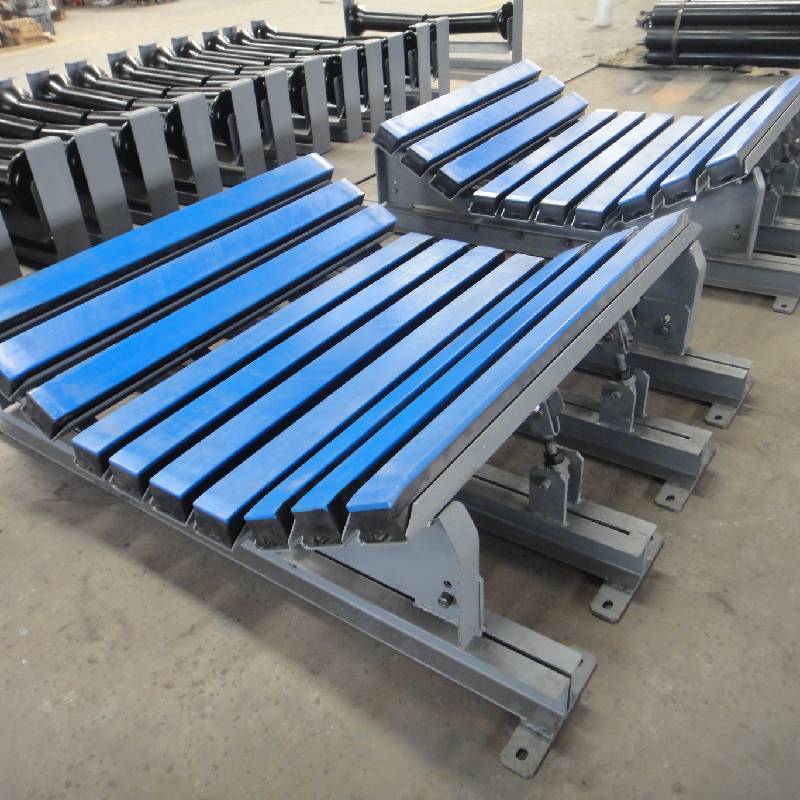
Materials used in roller manufacturing speak volumes about their durability and specific applications. Steel rollers, for instance, offer excellent strength and are a staple in heavy-duty conveyor systems found in mining and construction. These environments require robust rollers to manage abrasive elements and substantial weight. Conversely, plastic rollers are utilized where lightweight and corrosion resistance are prioritized, often seen in food manufacturing and chemical processing industries, where hygiene and chemical inertness can't be compromised.
From the perspective of expertise, choosing the right roller material and type is a decision that affects every other component linked to the conveyor system. A mismatch between the conveyor application and roller selection can lead to increased maintenance costs, downtime, and decreased operational efficiency. For instance, using steel rollers in a corrosive environment not only leads to operational inefficiencies but also propels maintenance expenses skyward.
When deliberating on roller selection, the focus should also encompass load-bearing capacity, surface coating, and seal design. A roller’s load capacity will determine the maximum weight it can sustain, a factor crucial in preventing system overstrain and failure.
belt conveyor roller
Surface coating extends a roller's life by protecting it against wear and environmental factors. Chrome plating and polymer coatings are popular choices for enhancing durability and corrosion resistance. The seal design is another often overlooked element but underscores the roller's capacity to operate seamlessly in dusty or wet environments. Here expertise in choosing a robust seal design can significantly mitigate maintenance demands and prolong the life of not only the rollers but the entire conveyor.
Expertise in maintenance and installation plays another critical role in extending the belt conveyor system's life and efficiency. Industry best practices suggest regular inspection for signs of wear or misalignment, immediate replacement of compromised parts, and periodic lubrication of rollers to ensure silent operation and friction reduction. Proper installation practices ensure optimal alignment and tension, pivotal factors in enhancing both belt and roller longevity.
Real-life experiences have repeatedly shown that injecting technology with regular innovation—such as smart sensors for predictive maintenance—can radically enhance a roller’s operational reliability. By embedding IoT technology within rollers, operators can predict potential failures before they result in downtime, streamlining repair schedules and reducing unexpected costs.
Authoritativeness in the field involves leveraging insights from industry leaders and aligning with accredited manufacturers known for their innovation and reliability in conveyor technology. Establishing partnerships with recognized entities not only ensures machinery aligns with the latest safety and efficiency standards but also taps into extensive research and development reserves.
Conveyor systems embody a dynamic play of forces, and at the heart of this play are the belt conveyor rollers. Trustworthiness in the context of a conveyor roller comes not just from technical specifications, but from the consistent application of strategic expertise, real-life experience, and leveraging trusted, leading-edge industry practices. Choosing the right conveyor roller is a multifaceted decision, with the potential to significantly enhance productivity and reduce operational dilemmas when approached with knowledge and forward-thinking strategy.