In the world of material handling systems, the belt conveyor pulley is an indispensable component that has continuously evolved to meet increasing industrial demands. These robust pieces of engineering not only facilitate the seamless movement of materials across different points but also significantly influence the efficiency, safety, and longevity of conveyor systems. My insights today stem from over two decades of experience working with diverse industries reliant on conveyor technology.
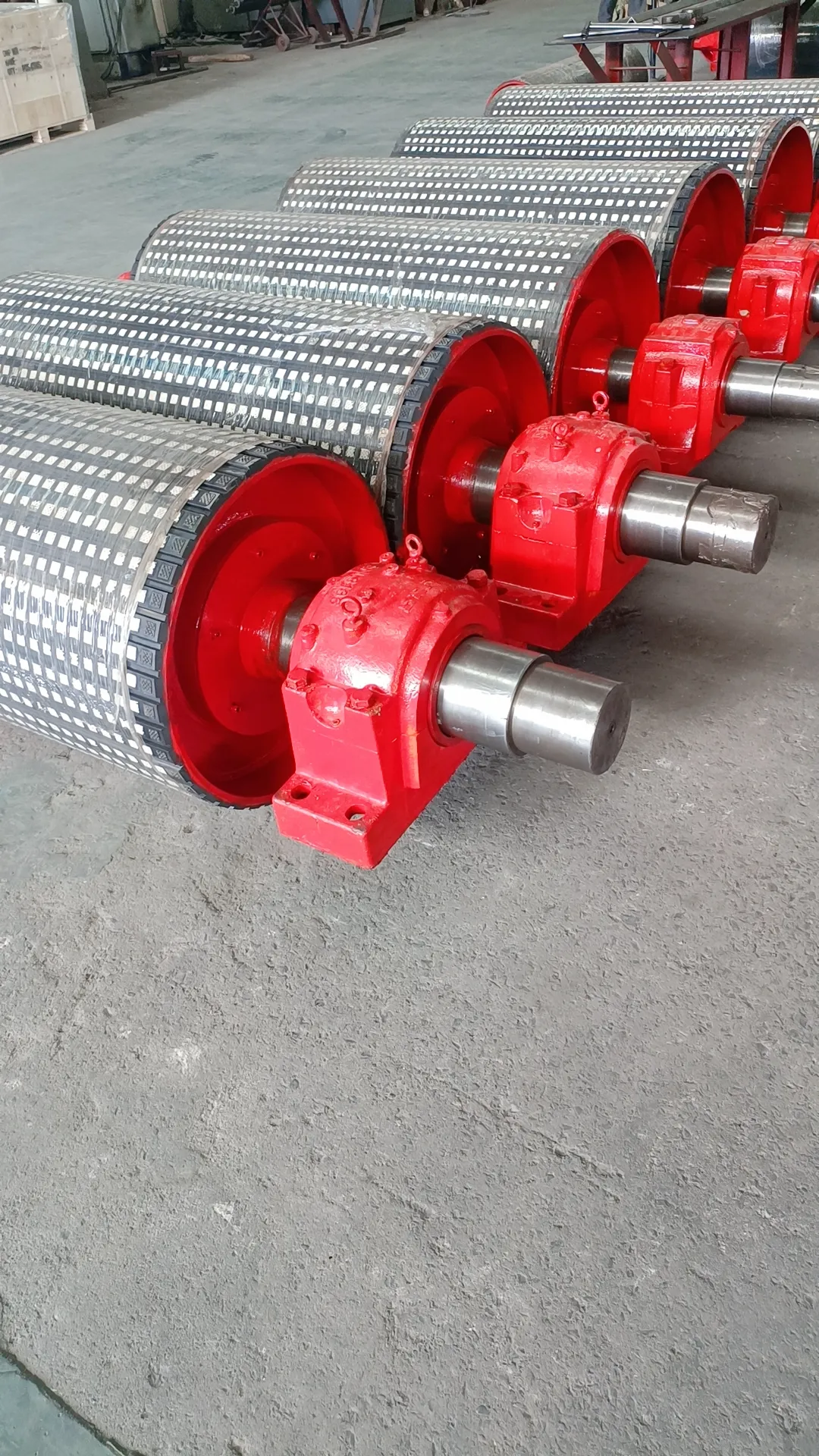
A belt conveyor pulley typically comprises the drum shell, end discs, and a hub. When constructing a pulley setup correctly, it's vital to account for material type, load capacity, and operational environment. These factors ensure that the configuration can withstand the mechanical stresses it encounters. My involvement in various specialized industries—ranging from mining to food manufacturing—affirms that customizing these variables can drastically impact performance outcomes.
Professional expertise in the selection and maintenance of belt conveyor pulleys is non-negotiable. Misjudgments can lead to premature pulley failure or conveyance inefficiencies, complicating workflow and inflating maintenance costs. Experienced professionals recommend precision-engineered pulleys with advanced features such as ceramic lagging or dynamic balancing. These enhance traction, diminish slippage, and reduce wear—efficiently extending the service life of the conveyor system.
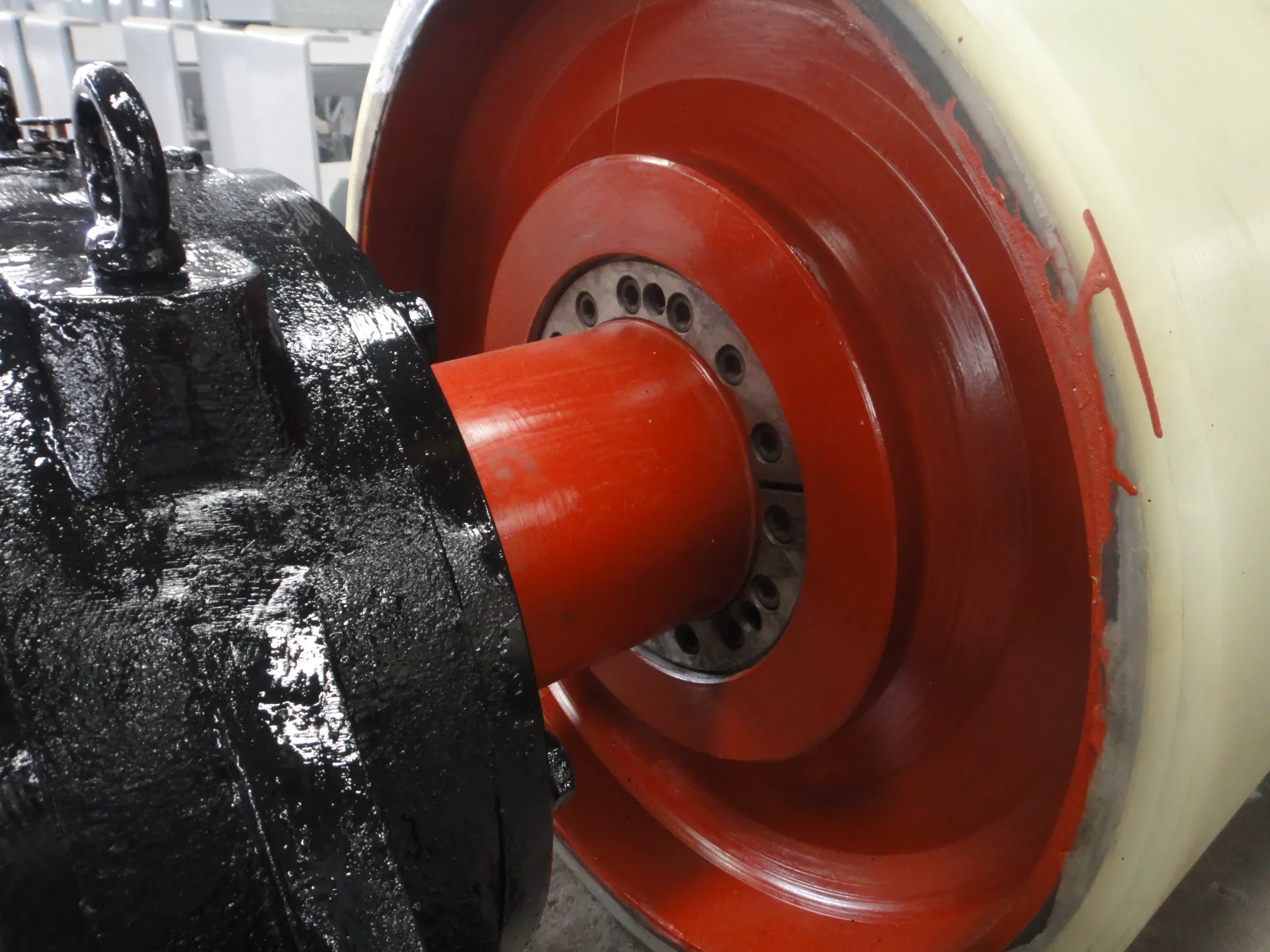
Industry authority is also concerned with ensuring that pulley installations adhere to international standards, such as those set out by ISO (International Organization for Standardization) and CEMA (Conveyor Equipment Manufacturers Association). Adhering to these standards guarantees that pulleys are fabricated and installed to accommodate high-stress conditions. It further underscores the need for regular audits and inspections to quantify alignment and wear over time.
belt conveyor pulley
In my role as a consultant,
I've advocated for incorporating technology into pulley oversight. By integrating IoT (Internet of Things) solutions, operators can remotely monitor pulley conditions in real time. This advancement assures stakeholders of trustworthiness through predictive maintenance analytics that flag potential issues before they become critical. For instance, an IoT-enabled sensor could detect irregular vibrations, indicating wear, which a team can address proactively.
For companies considering upgrading their belt conveyor systems, collaborating with reputable manufacturers is crucial. Trusted manufacturers offer comprehensive support—from initial design strategies tailored to operational needs to detailed on-site assessments. For instance, one of my recent projects involved deploying bespoke pulleys made from corrosion-resistant materials that excelled in harsh outdoor environments, enhancing the client’s operational efficiency sustainably.
Ultimately, understanding the full scope of a belt conveyor pulley's role allows businesses to make informed decisions that boost productivity while minimizing downtime. Whether you’re orchestrating logistics for large-scale mining operations or managing the intricacies of an automated packaging line, selecting the right pulley design can spell the difference between operational excellence and mechanical failure. Investing in trusted expertise and authoritative sources ensures that your material handling systems are robust, reliable, and ready to meet the challenges of modern industry demands.