The efficiency of a conveyor system is significantly enhanced by the implementation of a high-quality belt cleaner. For professionals working in industries reliant on such systems, the importance of maintaining optimal functionality through effective belt cleaning cannot be understated. In this article, we delve deep into the nuances of belt cleaner systems, offering insights from seasoned experts and sharing years of accrued industry knowledge.
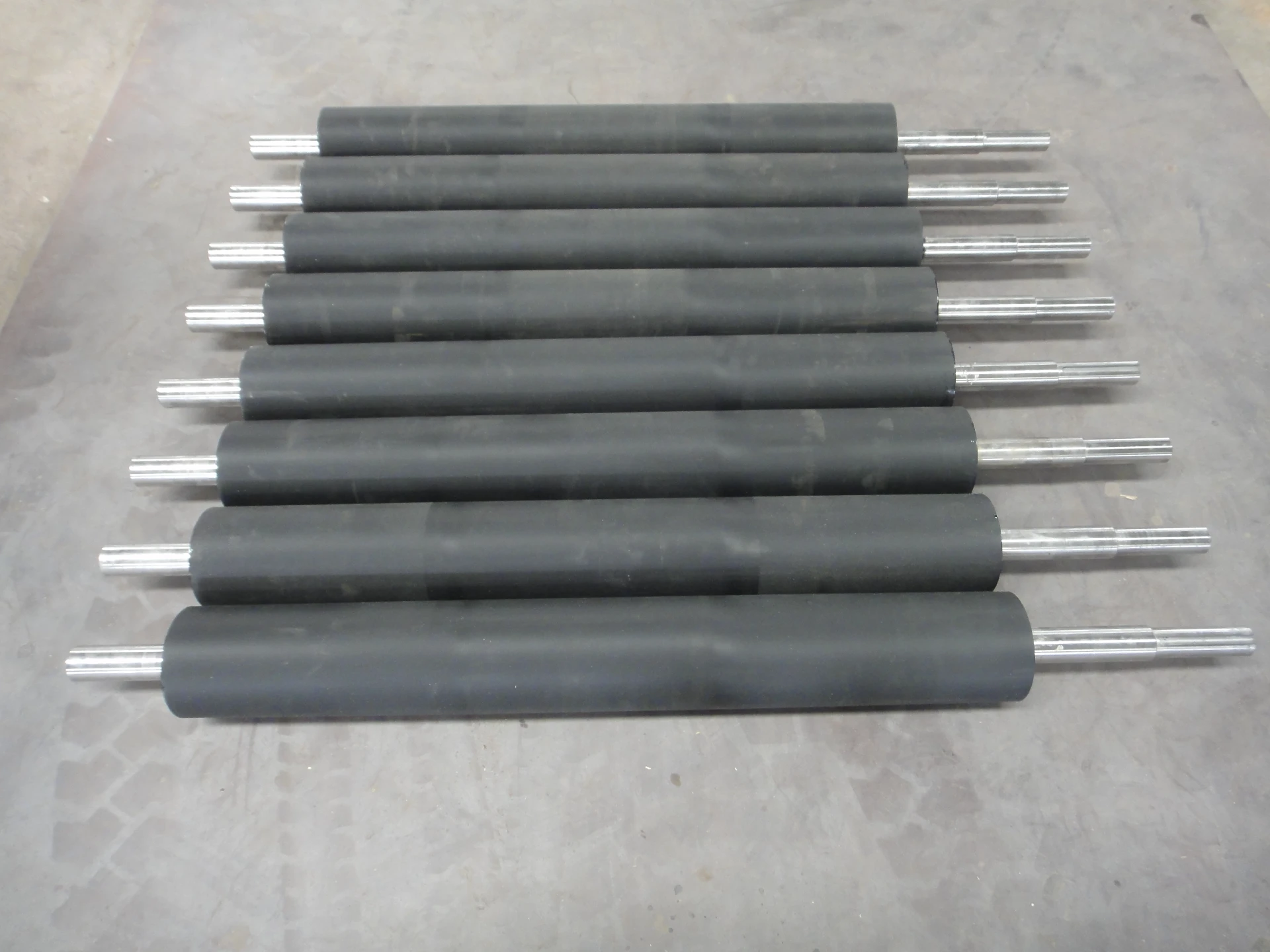
Having worked alongside numerous industry leaders, we've consistently observed that a meticulously maintained conveyor contributes to increased productivity, minimizes downtime, and reduces the risk of costly repairs. A well-engineered belt cleaner ensures that material carryback is significantly minimized. Carryback, if not addressed, leads to material buildup on the conveyor system's various components, threatening its operational efficiency.
Expertise in the field underscores the significance of selecting the right belt cleaner. Pioneers in conveyor system management advocate for cleaners tailored specifically to the materials and conditions of operation. A comprehensive understanding of the belt’s environment — including temperature variations, material abrasiveness, and moisture levels — is essential. This expertise translates directly into choosing between primary, secondary, and tertiary belt cleaners, with each variant offering distinctive benefits.
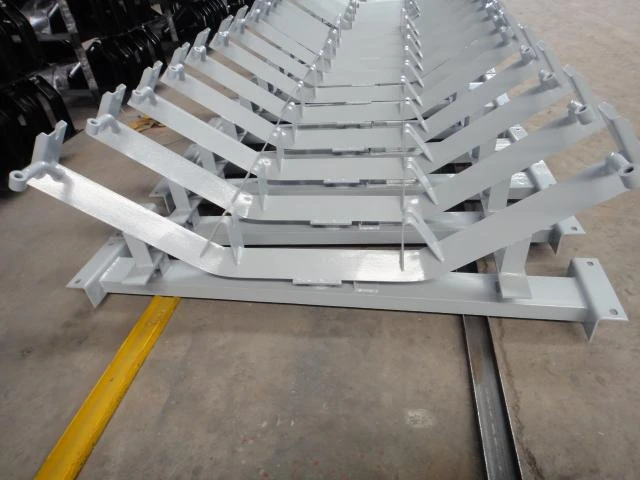
Primary belt cleaners, typically placed at the head pulley, are adept at removing the bulk of the carryback, dealing efficiently with larger material pieces. In contrast, secondary cleaners provide a finer touch, adeptly eliminating residual particles that primary cleaners might leave behind. For operations faced with particularly challenging cleaning scenarios, tertiary systems can be employed to offer an additional layer of assurance in cleanliness.
Authority in the area of belt cleaners also involves a comprehensive understanding of the materials used in their production. The selection of durable yet adaptable materials like high-grade polyurethane, tungsten carbide, or stainless steel blade tips ensures longevity and resistance against wear and tear — a primary cause of reduced efficiency in poorly maintained systems. These material choices underscore the blend of technological innovation and practical expertise that drive the industry forward.
Trustworthiness of information provided to users is paramount, particularly when discussing solutions impacting production efficacy. Belt cleaner manufacturers with a track record of reliability and positive user testimonials tend to rank higher in trust. It is crucial to examine reviews, case studies, and third-party endorsements when considering an addition to your conveyor system.
belt cleaner
Case studies highlight the tangible benefits of investing in reputable belt cleaners. For instance, a mining operation in Australia reported a remarkable 30% reduction in maintenance costs post the installation of high-efficiency belt cleaners. This real-world success story, among others, emphasizes the critical role these systems play in operational efficacy and cost management.
An often-overlooked aspect of belt cleaning systems is their maintenance and adjustment. Even the best belt cleaner requires regular checks to maintain its effectiveness. Engaging in routine inspections and adjustments as part of a preventive maintenance program can significantly prolong the lifespan of the belt cleaner and the conveyor belt itself. This practice not only prevents unexpected disruptions but also optimizes future resource allocation.
Furthermore, industry leaders advocate for training programs that enhance the skill sets of personnel responsible for conveyor maintenance. Staff knowledgeable in the intricacies of belt cleaning systems are assets to any operation. They ensure quick identification of issues, facilitate swift corrective actions, and sustain seamless operational flow. This investment in human capital is just as crucial as investing in technological upgrades.
As sustainable operations gain focus, premium belt cleaners contribute positively to environmental goals by reducing materials waste and energy consumption. By efficiently managing the carryback, these systems limit the volume of material that ends up in waste channels, reflecting a responsible approach to both business and environmental stewardship.
In conclusion, belt cleaners play a pivotal role in the productivity of conveyor-dependent industries. From the selection of materials and configurations to maintenance and personnel training, every aspect must be carefully considered to optimize performance and extend the service life of conveyor systems. As the industry advances, the integration of sophisticated technologies and methodologies promises to further elevate the efficacy and reliability of belt cleaning solutions.