Belt and pulley drive systems have cemented their place as a quintessential component across various industries due to their efficiency and reliability. From manufacturing plants to home garage workshops, these systems provide a seamless method for transmitting power between shafts. As someone who has witnessed the evolution and application of these systems firsthand, I am keen to share comprehensive insights to guide your understanding and optimize your utilization of belt and pulley drives.
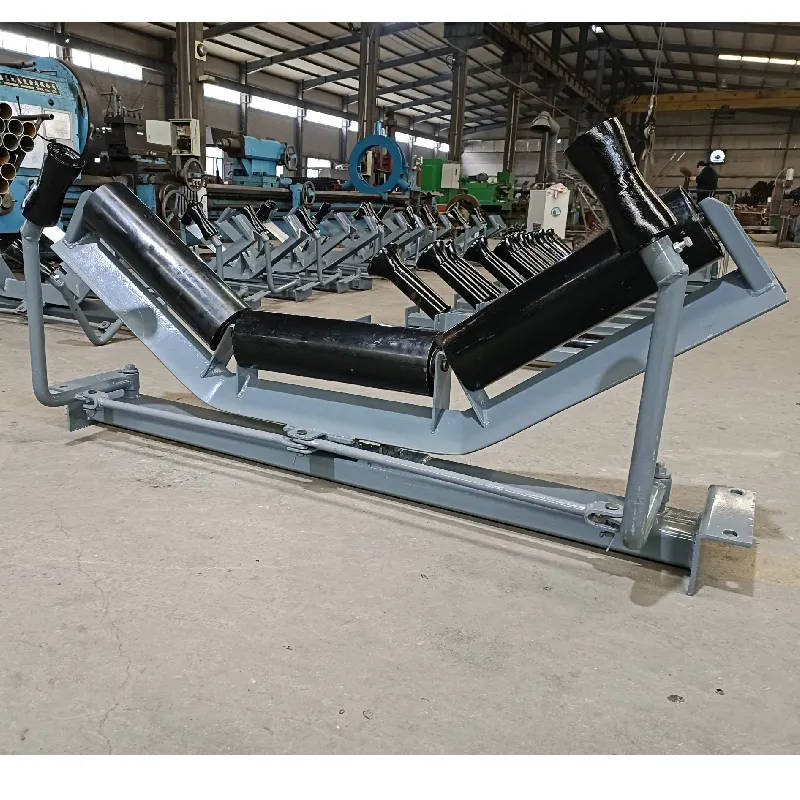
The fundamental advantage of belt and pulley systems lies in their simplicity. Unlike more complex mechanical systems, belt drives offer straightforward installation and maintenance, minimizing downtime and operational hiccups. In practice, this translates to a more efficient production line or a smoothly running home project, as these systems inherently reduce the risk of technical disruptions.
Due to their adaptable nature, belt and pulley systems excel in a variety of applications. Whether you are dealing with a simple setup in a woodworking shop or a complex assembly line in a major production facility, these systems provide unparalleled versatility. The ability to cater to varying loads and speeds without compromising on effectiveness establishes these systems as a flexible solution for many power transmission needs.
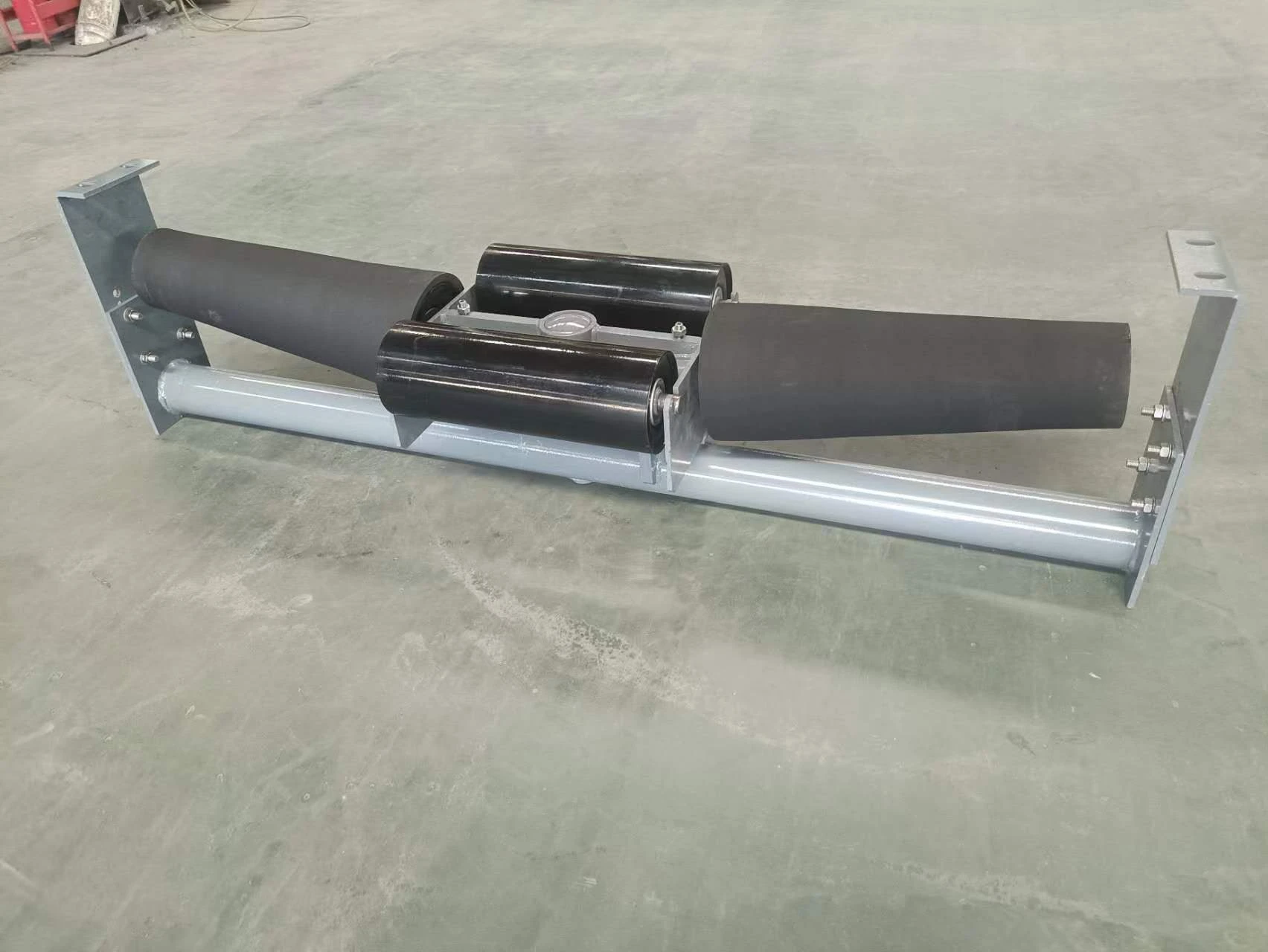
Precision is another key feature of belt and pulley drives. Leveraging the right type of belt and pulley can lead to significant improvements in alignment accuracy and efficiency. For example, synchronous belts—also known as timing belts—offer greater precision as they maintain consistent speed without slippage, crucial for high-stakes industries like automotive manufacturing where timing is everything.
The material choice for belts and pulleys is not just a matter of preference; it's a decisive factor in the performance and longevity of the drive system. For heavy-duty applications, using belts made from reinforced rubber or polyurethane can make a substantial difference. Similarly, pulleys made of durable materials like steel or cast iron ensure that the system withstands rigorous operational demands without succumbing to wear and tear.
belt and pulley drive
Routine maintenance is paramount if you aim to maintain peak performance of your belt and pulley setups. Through empirical evidence gathered over years in the field, I can attest that regular inspections for wear, proper tension adjustments, and alignment checks can significantly extend the system's lifespan. Neglecting these routines invariably leads to inefficiencies like slippage or, in worst cases, total system failure.
From an energy efficiency standpoint, belt and pulley systems are environmentally favorable. The low friction between the belt and pulleys reduces energy loss, translating into cost savings and a lower carbon footprint. This energy efficiency is particularly beneficial in large-scale industrial applications where even minor efficiency improvements can lead to substantial savings.
In terms of safety, belt and pulley systems are considered superior to chain drive systems due to their inherent design that reduces the risk of injuries. The absence of sharp edges and reduced vibration levels contribute to a safer working environment, an essential factor to consider, especially in workplaces with stringent safety regulations.
In summary, the belt and pulley drive system stands out as a paragon of industrial engineering. Its combination of efficiency, versatility, precision, and safety makes it the preferred choice across varied applications. Whether you are implementing these systems in large-scale industrial environments or smaller workshops, the key to optimizing their performance lies in selecting the appropriate components, maintaining meticulous upkeep, and understanding their operational parameters deeply. By adhering to these practices, professionals can harness the full potential of belt and pulley drives, ensuring both productivity and sustainability in their applications.