Beater rollers are a pivotal component in various industrial and manufacturing processes. Known for their ability to handle intense operations, these robust devices are indispensable in sectors ranging from textiles to paper manufacturing. Understanding the mechanics, applications, and maintenance of beater rollers can significantly enhance operational efficiency and product quality.
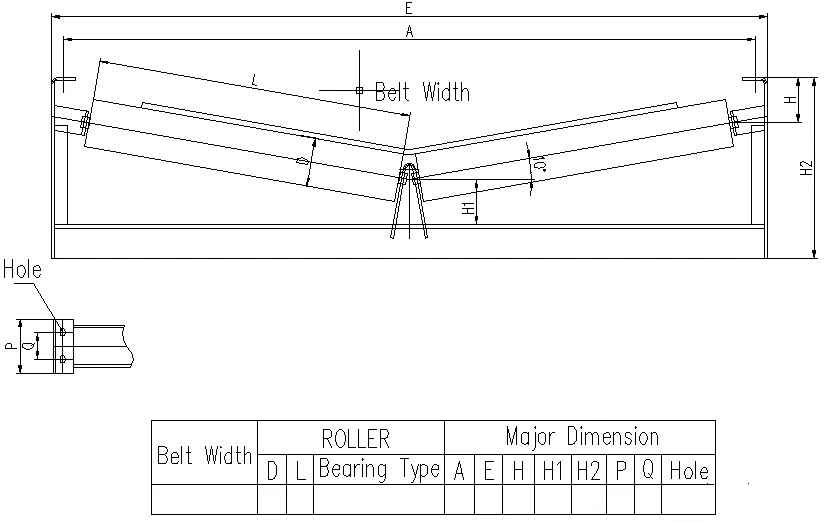
The construction and design of beater rollers reflect their critical role in industries. Typically made from durable materials such as stainless steel or high-grade polymers, they must withstand high pressure and wear. Expertise in material science is essential when selecting the appropriate beater roller for a given application. A properly chosen roller can optimize performance and longevity, crucial factors when downtime incurs significant costs.
Industrially, beater rollers are employed in processes that require uniformity and consistency. In the textile industry, for example, they play a crucial role in carding, a process that disentangles, cleans, and intermixes fibers to produce a continuous web of fibers. The evenness and precision brought about by beater rollers ensure that the final fabric maintains its integrity and quality. Similarly, in paper manufacturing, beater rollers aid in the proper pulping and refining of wood fibers, ensuring a uniform texture and thickness in the paper produced.
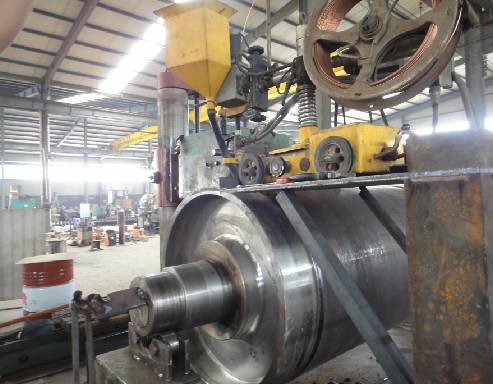
Authoritative understanding of beater roller performance can differentiate successful operations from faltering ones. Advanced knowledge in mechanical engineering and dynamics is often exercised to optimize roller settings. Factors such as rotational speed, pressure application, and temperature settings must be meticulously calibrated. This calibration demands precision and expertise because even minor deviations can lead to material inconsistencies or mechanical failures.
beater roller
Maintaining beater rollers involves routine inspections and proactive servicing. In practice, regular lubrication, alignment checks, and surface inspections are vital to uphold operational standards. Expertise in these maintenance routines not only extends the lifespan of the rollers but also ensures uninterrupted production cycles. Innovative sensors and software are increasingly being integrated into beater roller systems for real-time condition monitoring, heralding an era of predictive maintenance that further enhances operational reliability.
Trustworthiness in discussions of beater rollers is anchored in a thorough understanding and clear communication of their capacities and limitations. Manufacturers often provide detailed specifications and operational guides to ensure correct usage. Industry authority in this regard is backed by documented outcomes and user testimonials that reinforce the effectiveness of these guidelines. Moreover, trusted brands and models often come recommended by industry leaders, further affirming their reliability and performance under demanding conditions.
In conclusion, the significance of beater rollers in industrial processes is complemented by an ongoing evolution in their technology and application. Their contribution to product quality and operational efficiency underscores a compelling need for expertise in their use. As industries continue to advance, the precision offered by expertly managed beater rollers will remain crucial, demonstrating a seamless blend of engineering prowess and practical applicability that aligns with the modern demands of production and manufacturing frameworks.