The modern industrial landscape frequently employs conveyor systems to enhance material handling efficiencies. Central to these systems is the belt conveyor, renowned for its simplicity and reliability. Understanding its components is essential for anyone aiming to optimize or troubleshoot these systems, offering an edge in performance, cost-efficiency, and innovation.
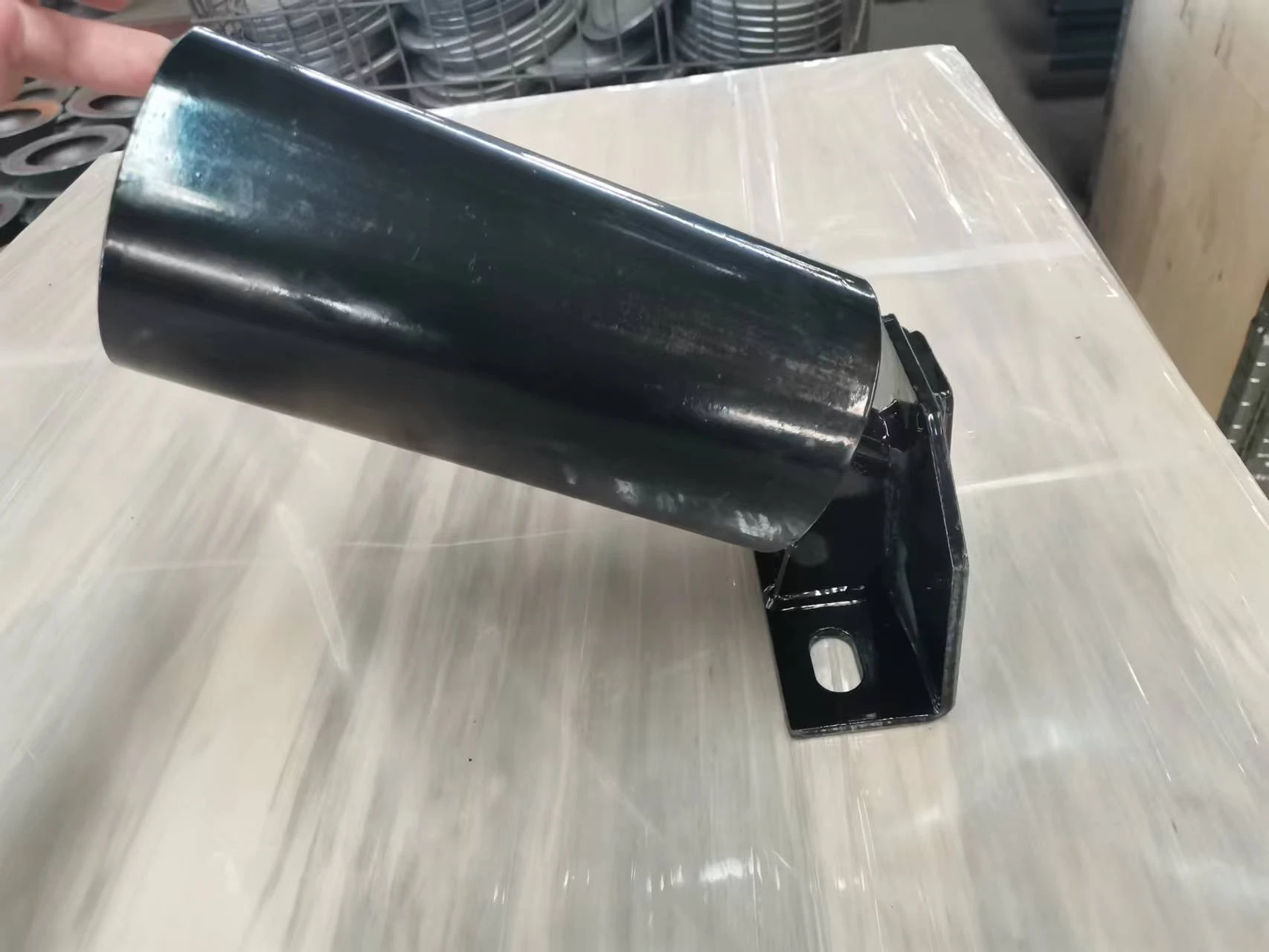
Beginning with the conveyor belt itself, it's the most visible component, serving as the medium that directly contacts the material being transported. Belts are typically made from a variety of materials such as rubber, polyester, nylon, or steel-reinforced compositions, each selected based on the operational conditions such as load weight, environmental conditions, and the type of material being transported. For those seeking expertise in belt selection, consider the tensile strength requirements and wear resistance properties, which directly influence the belt’s lifespan and efficiency.
Next, the driving unit plays an equally pivotal role. It consists of the motor and drive mechanism which set the belt in motion. An expert eye will assess factors such as motor horsepower and speed control mechanisms, crucial for achieving the desired speed and handling capabilities. Advanced systems may incorporate variable frequency drives (VFDs) or servo motors, allowing for precise control and energy efficiency—key indicators of a system optimized for long-term performance.
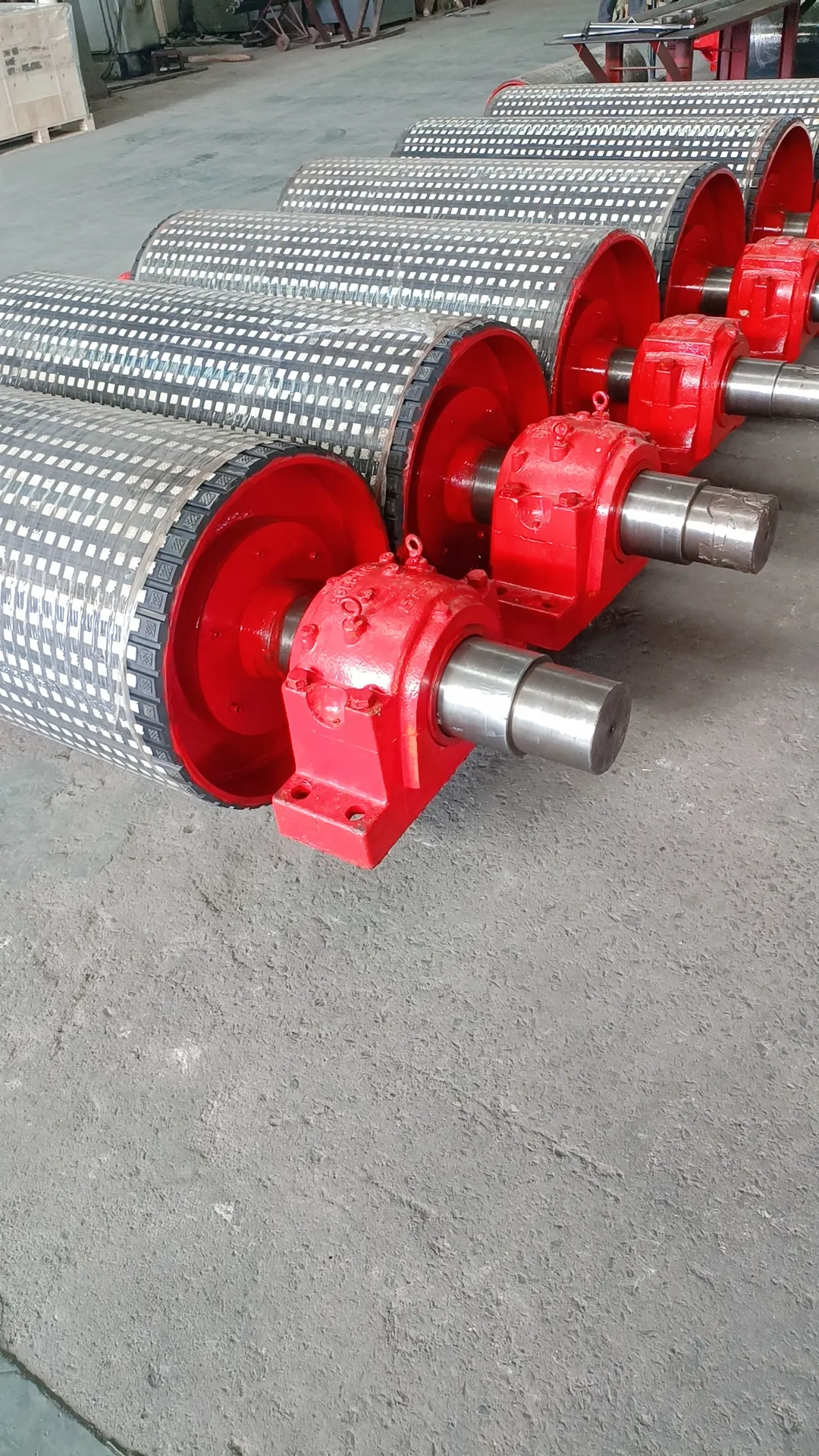
The idlers, often overlooked, are another critical component. These cylindrical rollers are positioned along the conveyor to support the belt and ensure smooth motion with minimal friction. Different types of idlers, such as troughing, return, or impact idlers, are selected based on their placement within the system and the type of load they will bear. Mastering the balance between spacing and idler type can significantly reduce energy consumption and wear on the belt—an area ripe for innovation and savings.
Pulleys are integral as well; they guide the conveyor belt and regulate its tension. Drive pulleys and tail pulleys must be precision-engineered to prevent slippage and ensure operational reliability. The selection of pulley diameters and surface finishes (such as rubber-lagged, ceramic-coated, or bare steel) demands an understanding of both mechanical physics and material science, given their direct impact on traction efficiency and maintenance frequency.
components of belt conveyor system
Furthermore, the conveyor frame, often customized, supports all the components and ensures alignment and stability. Fabrication material and design directly impact the structure’s ability to withstand the operational environment. Stainless steel is commonly used for its durability and resistance to corrosion, especially in industries dealing with harsh climates or materials. Expertise here is demonstrated in balancing structural strength with cost-output ratios to ensure a return on investment.
Safety mechanisms cannot be ignored. Emergency stop systems, protective guards, and automated shutdown sensors are essential, not only from a regulatory compliance standpoint but also to build trust with operators and stakeholders by prioritizing human safety. Experience in installing and maintaining these systems showcases a commitment to ethical operations and operational continuity.
In addition to the mechanical components, the control systems integrating modern technology such as IoT devices lend themselves to smarter operations. Sensors and automation interfaces allow for real-time data monitoring and predictive maintenance—areas where experience turns insights into cost savings and efficiency enhancements.
Overall,
the complexity of belt conveyor systems is balanced by their modular simplicity. Each component's interdependence means that expertise in one area frequently translates to evaluative insights across the system’s entirety. Professionals in this field cultivate trust by recognizing and communicating these interdependencies, offering innovative solutions that meld theoretical expertise with practical applications.
For those dedicated to advancing their knowledge or operational proficiency, exploring new materials, custom designs, and monitoring technologies presents substantial opportunities for differentiation and leadership in industrial applications.