Understanding the various components of a conveyor system is integral to optimizing its functionality and efficiency in industrial settings. The design and integration of these components require a blend of technical expertise, industry experience, and a keen understanding of material handling complexities.
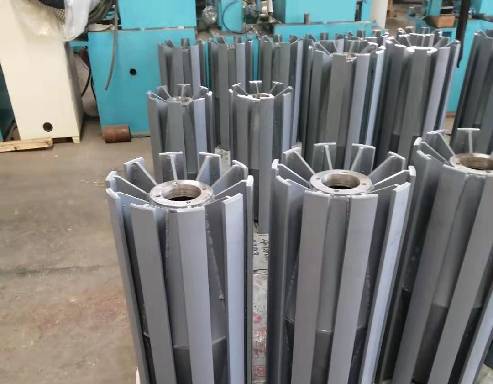
A conveyor system primarily consists of belts, rollers, pulleys, and motors. Each part plays a pivotal role in material transportation, demanding precise engineering to maximize efficiency and longevity. An insightful overview of these components can empower facility managers and engineers to make informed decisions when configuring their systems.
The conveyor belt is a critical component that determines the type and volume of material that can be transported. Depending on the application, belts can be made of rubber, metal, or synthetic materials. Selecting the right belt material is crucial as it directly affects wear resistance, load capacity, and overall system durability. Expertise in belt specifications allows for tailored solutions that meet specific operational demands, enhancing system reliability.
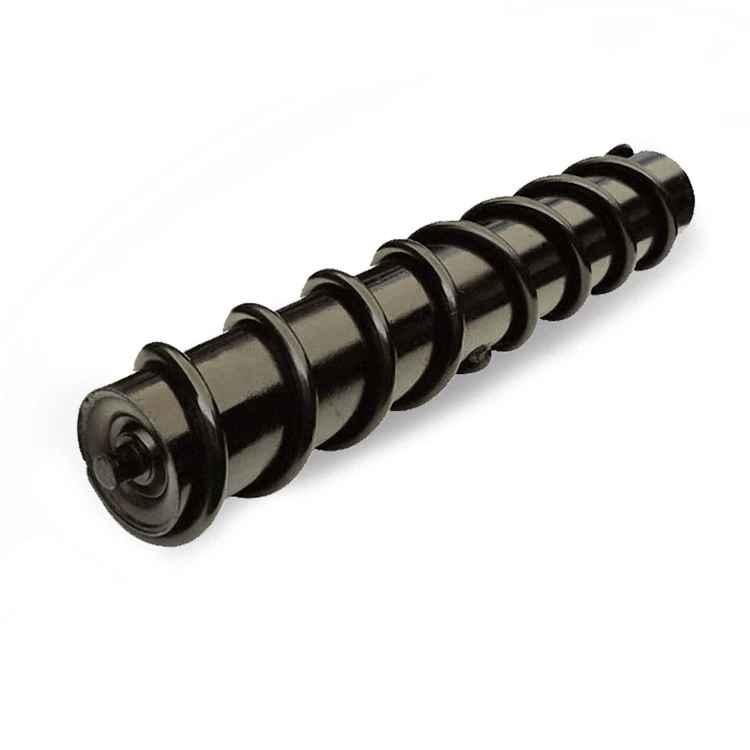
Rollers support and guide the conveyor belt, and their design can significantly impact the system’s performance. Typically crafted from durable materials like steel or aluminum, rollers must be chosen based on load requirements and environmental conditions such as temperature and humidity. Knowledge of roller types and configurations adds an additional layer of customization, ensuring smooth and efficient material flow.
Pulleys drive the belt and provide the tension necessary to keep it moving smoothly. Proper pulley design and alignment are paramount, as misaligned or poorly crafted pulleys can lead to belt slippage or breakage. Industry expertise in pulley systems contributes to optimal tension management and reduces maintenance downtime, fostering a more productive operational environment.
components of a conveyor system
Motors are the powerhouse of conveyor systems, providing the energy needed to move the belt. Selecting the appropriate motor involves understanding the operational dynamics such as speed requirements, load weights, and power consumption. By matching motor specifications to system needs, facility managers can significantly enhance energy efficiency and reduce operational costs.
A sophisticated understanding of control systems further enhances a conveyor system’s efficiency. Modern conveyors often utilize automated controls and sensors that monitor and adjust system operations in real time. This not only minimizes human intervention but also increases safety, significantly reducing the risk of accidents and ensuring compliance with safety regulations.
Customization and integration play a vital role in contemporary conveyor system design. Tailoring systems to fit specific industrial processes helps in maximizing productivity. Experience shows that a well-integrated system can lead to substantial improvements in throughput and material handling accuracy.
Moreover, maintaining these systems requires a sound understanding of each component’s functionality and maintenance needs. Regular inspections and timely repairs are indispensable to prolonging the lifespan of the components and ensuring uninterrupted operation. Trustworthy maintenance protocols and reliable supplier relationships are invaluable assets in this regard.
In conclusion, the components of a conveyor system are intricate and multifaceted, necessitating a comprehensive understanding of their individual and collective roles. A commitment to ongoing learning and adaptation, backed by technical expertise and industry experience, equips professionals to enhance system performance and efficiency. This strategic approach not only positions a business at the forefront of material handling innovation but also fosters a trustworthy partnership with stakeholders across the industrial spectrum.