Conveyor belt rollers are a crucial component in material handling systems, and understanding their types can vastly improve the efficiency and safety of industrial applications. Though seemingly simple, the wrong selection can lead to increased wear, frequent downtime, and inflated operational costs.
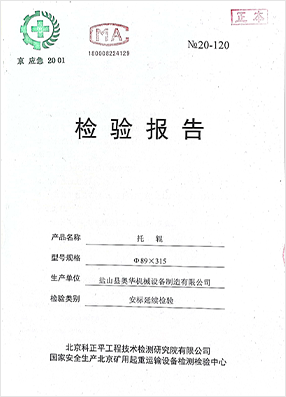
The primary types of conveyor belt rollers fall into several key categories drive, return, impact, carrier, and guide rollers, each having distinct roles and features.
Drive rollers, or head pulleys, are the power source of conveyor belt systems. Made from durable materials such as steel or rubber, they supply the friction and propulsion required to move the belt forward. A deep understanding of speed, torque, and power transfer principles is essential for optimizing these rollers in high-performance industrial settings.
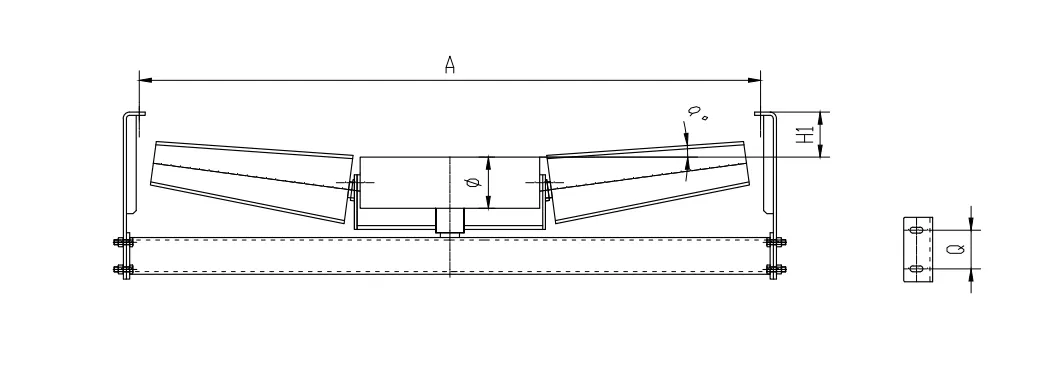
Return rollers, located on the underside of the belt, provide support for the return path of the conveyor. Given their position and function, they endure different stress points compared to the load-bearing segments of the system. High-quality return rollers reduce belt sagging and unnecessary tension, preventing premature belt wear.
Impact rollers, typically positioned near loading zones, are designed to absorb shocks and reduce damage to the belt from heavy or abrasive materials. They are often lined with rubber rings or other resilient materials. Proper assessment of material weight and drop height is vital, as these parameters influence the choice and spacing of impact rollers to enhance system durability and reliability.
conveyor belt roller types
Carrier rollers, the lifeline for the transport phase of materials, can differ based on the belt type. For example, trough-type carriers are used for bulk materials, adjusting to the conveyor's troughing angle. Flat-belt systems, conversely, employ flat carriers, necessitating knowledge in load distribution for maximizing conveyor efficiency and minimizing energy consumption.
Guide rollers ensure the tracking of the conveyor belt stays true, preventing slippage and ensuring the belt aligns within the intended path. Poor tracking can lead to misalignment, affecting productivity and potentially causing untimely system failures. Guide roller adjustment is a nuanced task, demanding expertise in alignment techniques and regular system audits to maintain optimal function.
Advanced material options and designs have evolved in response to specific industry needs, such as mining, automotive, and food processing. For instance, corrosion-resistant stainless steel rollers are favored in environments exposed to moisture, while self-cleaning rollers are indispensable in dusty, sticky materials handling scenarios.
Investing in quality roller materials and innovative engineering solutions is non-negotiable for industrial environments where downtime equals significant financial loss. Partnering with roller manufacturers who demonstrate expertise in engineering and who can provide tailored solutions based on thorough system audits ensures both accuracy and trustworthiness in selection.
The role of conveyor belt rollers extends beyond basic material transport; they are integral to a system’s safety, energy efficiency, and operational cost-effectiveness. An expert approach to roller selection and maintenance equips businesses with the tools needed for superior operational control, ultimately bolstering productivity while reducing energy consumption and maintenance costs. Prioritizing comprehensive strategies that encompass industry-specific analyses, advanced materials engineering, and a clear understanding of load dynamics ensures conveyor systems remain robust, efficient, and aligned with the complex demands of modern material handling.