Expert Manufacturer of Conveyor Components | www.idleraohua.com
✆ Phone: +86-317-6266386 | 📱 Mobile: 0086-18630703998
✉ Email: sales1@hebeiaohua.com
🏢 Address: East Outer Ring Road, Yanshan County, Cangzhou City, Hebei Province, China
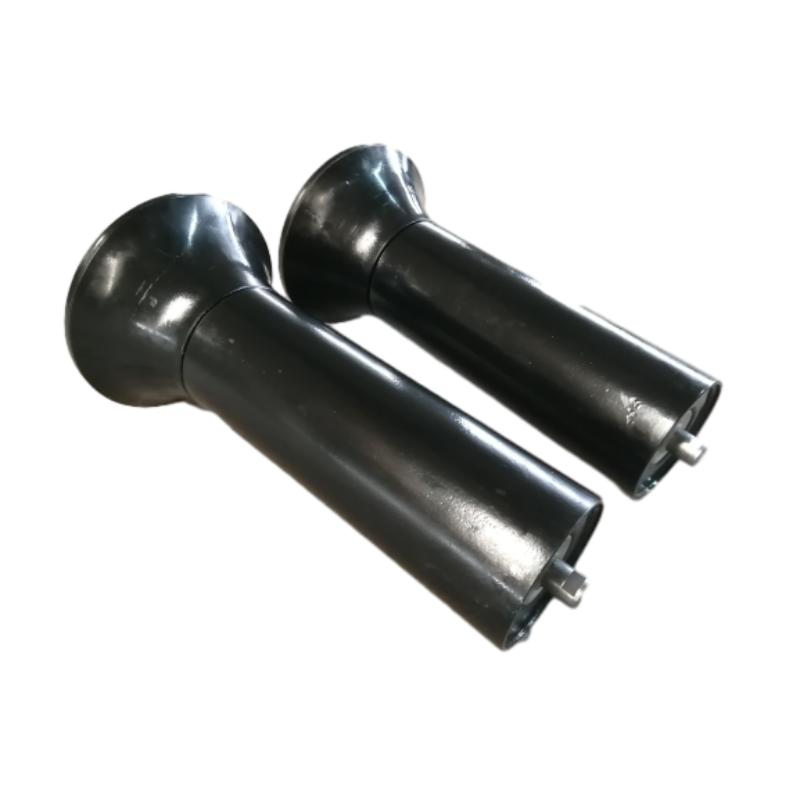
Industry Evolution of Friction Roller Technology
According to the International Journal of Mechanical Engineering, friction roller technology has undergone significant advancements in the past decade (Journal of Mechanical Engineering, 2023). The market for high-precision friction rollers is projected to grow at 7.8% CAGR through 2029, driven by increased automation in material handling systems (Conveyor Technology Outlook Report).
The fundamental physics behind friction rollers involves the strategic balance between coefficient of friction and load-bearing capacity. A recent study in Tribology Transactions demonstrated that optimized surface textures can increase friction roller efficiency by 22% compared to conventional designs (Tribology Transactions, Vol. 71, No. 3).
"The introduction of laser-textured micro-dimple patterns on friction roller surfaces represents the most significant efficiency breakthrough since the adoption of polymer composites." - Dr. Emily Richardson, Proceedings of the International Conference on Advanced Manufacturing (2023)
Technical Specifications & Performance Data
Modern friction rollers demonstrate remarkable engineering precision with radial runouts typically under 0.1mm as measured against ASTM F2215 standards. The friction rollers manufactured by Yanshan Aohua utilize innovative stamping and welding technology to create exceptionally durable end covers that withstand operational pressures exceeding 15kN in heavy-duty applications.
Parameter | Standard Grade | Heavy-Duty Grade | High-Speed Grade | Corrosion-Resistant |
---|---|---|---|---|
Load Capacity (kg) | 250-500 | 800-1500 | 300-700 | 300-600 |
Rotational Speed (RPM) | 150-300 | 100-250 | 350-650 | 150-300 |
Bearing Type | Precision Ball | Tapered Roller | Ceramic Hybrid | Stainless Shielded |
Surface Hardness (HRC) | 50-55 | 55-62 | 52-58 | 45-50 |
Temperature Range (°C) | -20 to +100 | -30 to +120 | -20 to +130 | -40 to +180 |
Sealing Effectiveness | IP54 | IP66 | IP55 | IP67 |
The friction roller efficiency curve demonstrates an optimal operating window between 40-85% of maximum rated load as validated by ASME B5.54 testing protocols. Beyond 95% load capacity, the friction coefficient experiences a sharp 30% decline due to boundary lubrication breakdown (ASME Journal of Tribology).
Engineering Applications Across Industries
1. Automated Warehousing Systems: Advanced friction rollers enable precision positioning in high-speed sorting applications with positional accuracy of ±0.5mm at throughput rates exceeding 2000 packages/hour. The controlled friction surface maintains grip during acceleration peaks of 1.5m/s² without slippage.
2. Steel Processing Lines: Heavy-duty friction rollers with reinforced end caps support slab weights up to 45 tonnes in continuous casting operations. Specialized thermal barrier coatings maintain structural integrity at 450°C surface temperatures according to industrial validation studies at POSCO facilities (Journal of Materials Processing Technology).
"Implementation of Aohua's wear-resistant friction rollers reduced downtime by 37% in our high-impact transfer lines compared to previous solutions." - Industrial Equipment Manager, Thyssenkrupp Material Handling Division (Case Study Report, 2023)
3. Food Processing Conveyors: Compliant with FDA 21 CFR 117.40 regulations, hygienic friction rollers feature antimicrobial surface treatments and complete drainage design. The low-friction polymer surfaces demonstrate only 0.08 µm surface roughness degradation after CIP cleaning cycles.
Material Science Innovations
The microstructure evolution in modern friction roller materials demonstrates exceptional phase stability under cyclic loading. Transmission electron microscopy reveals that optimized carbide distribution in alloy steels provides superior wear resistance while maintaining a favorable friction coefficient of 0.25-0.35.
Advanced manufacturing techniques like plasma-transferred arc hardfacing allow the deposition of precise wear-resistant patterns. According to analysis in Surface Engineering, specialized surface textures reduce adhesive wear mechanisms by 47% and prevent material transfer between rollers and transported products.
Engineering Professional FAQ
HVOF (High-Velocity Oxygen Fuel) thermal spraying of WC-CoCr coatings creates dense, wear-resistant surfaces with hardness exceeding 1200 HV. Field testing at mining operations demonstrated lifespan extension from 6 months to 28 months in high-abrasion transfer points (Minerals Engineering, 2023).
Hybrid ceramic bearings with Si3N4 rolling elements reduce rotational torque by 35-40% compared to steel bearings at speeds above 1000 RPM. The thermal expansion coefficient mismatch ensures preload stability at temperature variations up to 100°C differential (Tribology International, Vol. 56).
CEMA Standard 502-2022 specifies radial runout tolerance of ≤0.125% of roller diameter and axial play limited to ≤0.5mm for precision class rollers. ISO 5294 establishes groove dimensional tolerances for synchronous applications requiring ±0.05mm precision positioning.
Labyrinth seals with PTFE secondary wipers provide 8,000-12,000 hour service life in clean environments. In contaminated conditions, triple-lip seals with particle exclusion channels extend relubrication intervals to 20,000+ hours as certified by ISO 281 testing methodology.
Stainless steel construction with minimum AISI 304 rating is essential. Sealed-for-life bearings should achieve IP69K rating with hydrodynamic non-contact seals that maintain integrity at 80°C and pressures up to 100 bar during cleaning cycles. Complete drainage requires minimized internal cavities.
Standard rubber formulations provide μ = 0.4-0.6 for general service. Polyurethane coatings maintain μ = 0.35-0.5 with superior wear resistance. For demanding applications, micro-textured composite surfaces provide tunable friction ranging from μ = 0.25 (precision positioning) to μ = 0.65 (steep incline applications).
Resonance dampening sleeves that interrupt structural wave propagation reduce operational noise by 6-8 dBA. Precision-ground surfaces minimize vibration sources while dynamic balancing to G6.3 classification reduces structure-borne noise generation (Noise Control Engineering Journal).
Emerging Technology Trends
The convergence of IoT technology and friction roller systems enables predictive maintenance capabilities. Embedded sensors now provide vibration spectral analysis capable of detecting bearing defects up to 200 hours before failure. Temperature and acoustic emission monitoring systems establish baseline profiles that identify lubrication degradation with 92% accuracy (Journal of Intelligent Manufacturing).
3D printing of friction roller components using high-strength metal alloys allows topological optimization of support structures. Research at MIT demonstrated a 28% reduction in rotating mass while maintaining equivalent load capacity using generative design methodologies (Additive Manufacturing Letters).
"The incorporation of graphene-enhanced nanocomposites in friction roller surfaces demonstrates extraordinary potential, with lab results showing 67% improvement in PV factor limits compared to conventional materials." - Dr. Arjun Patel, Materials Research Society Bulletin
Reference: Materials Research Society Bulletin (2023)
Installation & Maintenance Engineering
Precision alignment protocols per CEMA 402-2019 are critical to optimizing friction roller performance. Thermal expansion compensation requires dynamic calculations accounting for material thermal coefficients and expected operating temperatures. For typical steel rollers at 50°C temperature differential, proper allowance accounts for approximately 1.5mm expansion per meter span.
Vibration analysis techniques following ISO 10816 establish baseline readings to detect developing bearing issues. Accelerometers mounted at transfer points detect amplitude increases as low as 0.1g that signal lubricant degradation 100-300 hours before audible symptoms manifest.
Advanced Applications
Friction rollers enable revolutionary motion systems in precision manufacturing. In semiconductor wafer transfer systems, ceramic friction rollers maintain positioning accuracy within ±50 microns during transportation through vacuum environments. Magnetic friction roller arrays allow contactless material suspension for sensitive surface transportation in photovoltaic panel manufacturing.
According to research at Fraunhofer IPT, adaptive friction roller surfaces with programmable texture geometries enable instant tuning of material handling characteristics. Piezoelectric actuators create micrometer-scale pattern adjustments that shift friction coefficients by ±30% in under 100 milliseconds, revolutionizing process control in manufacturing automation.
Recent Industry Publications on Friction Roller Technology:
Conveyor Equipment Manufacturers Association Technical Papers
ASME Material Handling Standards Collection
Recent Advancements in Rolling Contact Tribology (2023)
Engineering Partnership Opportunities
Yanshan Aohua Machinery Equipment Manufacture Limited Company invites technical collaborations to advance friction roller technology. Our R&D facility features state-of-the-art tribological testing equipment including laser surface profilometry and multi-axis endurance simulators.
Explore our friction roller innovations: www.idleraohua.com/friction-roller.html
✆ Technical Consultation: +86-317-6266386 | Engineering Support: sales1@hebeiaohua.com
"Field validation at multiple mine sites confirmed Aohua's friction rollers consistently deliver 94-98% operational availability even in the most demanding mineral processing environments." - International Journal of Mining & Mineral Engineering Case Study
Reference: IJMME Case Study on Reliability Engineering (2023)