Rubber coated conveyor drive rollers play a pivotal role in numerous industrial applications. These components enhance conveyor systems, offering improved traction and durability, which ultimately leads to increased efficiency and reduced costs. Understanding their advantages and applications not only helps in selecting the right product but also optimizes overall production processes.
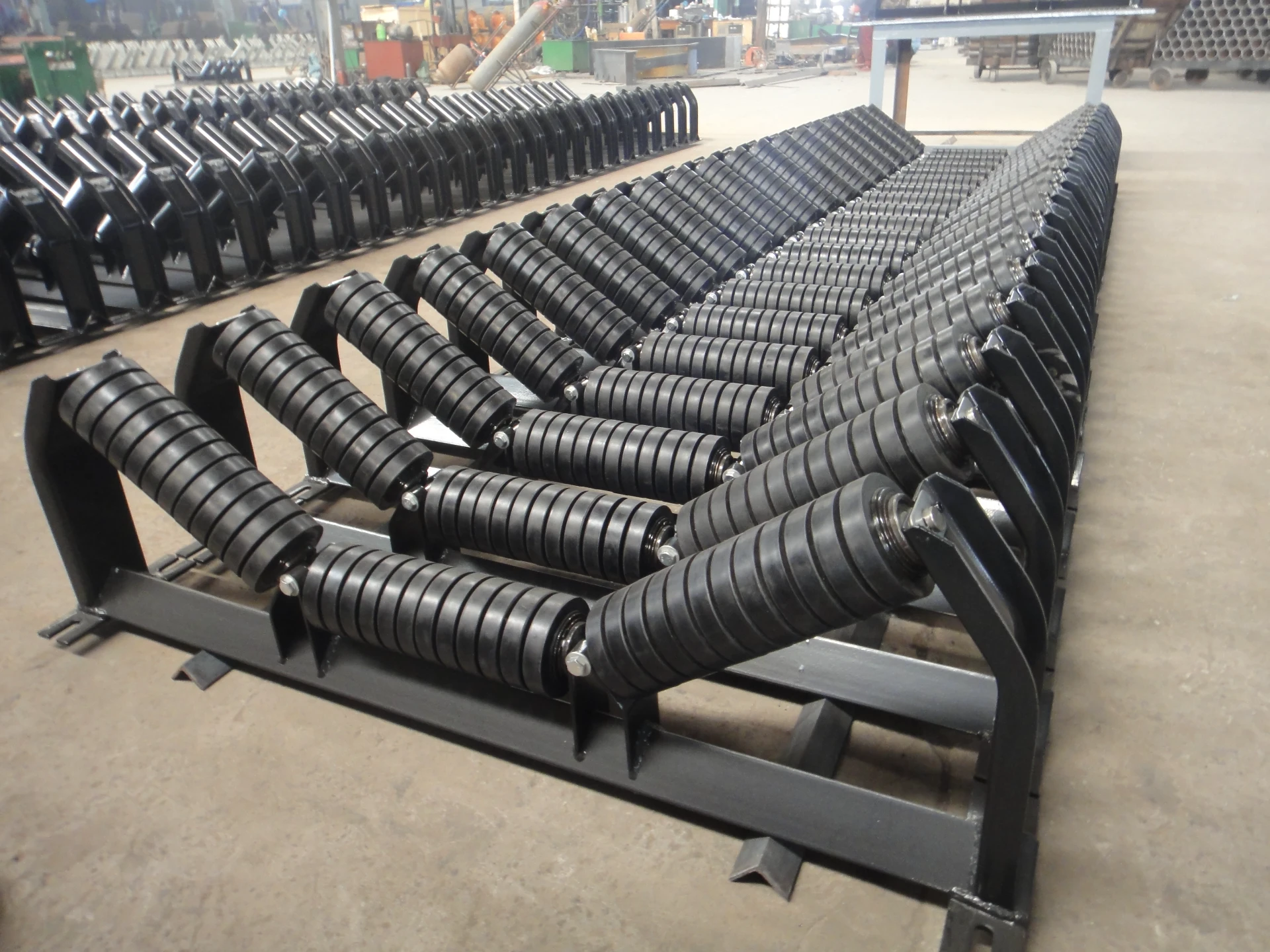
One of the most notable benefits of rubber coated drive rollers is their superior grip. The rubber surface provides enhanced traction compared to bare metal or plastic rollers, allowing for better control over the movement of materials. This improved grip is particularly beneficial in environments where moisture or dust could potentially affect the performance of the conveyor system. Industries dealing with textiles, packaging, and agriculture often require such reliability to maintain smooth operation in challenging conditions.
Moreover, rubber coated rollers contribute significantly to noise reduction in industrial settings. Conveyor systems can be notoriously loud, especially in large-scale operations. The cushioning effect of the rubber not only dampens sound but also absorbs vibrations, leading to a quieter working environment. This reduction in noise pollution not only benefits the workforce by providing a more comfortable workspace but also complies with occupational health regulations, which are becoming increasingly stringent.
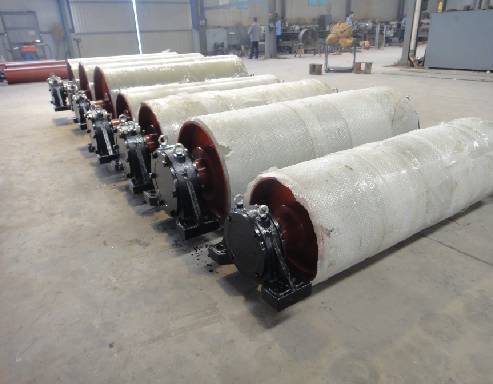
Durability is another key feature of rubber coated conveyor drive rollers. The rubber coating acts as a protective layer against wear and tear, which is crucial for extending the longevity of the rollers. This protective layer guards against the effects of abrasion and the impact of dropped or conveyed materials. Additionally, many rubber coatings are specially formulated to resist chemicals, oils, and UV radiation, ensuring that these rollers maintain their integrity in harsh industrial environments. These characteristics make them an ideal choice for industries such as mining, automotive, and food processing, where equipment is often exposed to tough conditions.
rubber coated conveyor drive rollers
From an expertise standpoint, selecting the appropriate rubber coating for a roller involves understanding the specific needs of your operation. Materials such as nitrile, neoprene, or urethane each offer unique properties. Nitrile rubber is perfect for applications requiring resistance to oils and fuels, neoprene provides good chemical stability in different temperatures, and urethane offers excellent abrasion resistance and elasticity. Consulting with a knowledgeable supplier can ensure that the chosen roller not only meets industry standards but also excels in its application, thereby improving efficiency and reducing downtime.
The authoritative positioning of a business can be significantly enhanced by integrating high-quality rubber coated conveyor drive rollers. By investing in components that promise reliability and efficiency, businesses demonstrate a commitment to maintaining high operational standards while also showcasing an understanding of their industry's demands. Products that offer proven performance create trust among clients and stakeholders, fostering a reputation for reliability and excellence.
Trustworthiness is further established when businesses share real-world experiences and customer testimonials that highlight the success stories associated with their conveyor systems. Case studies documenting how specific industries benefited from implementing these rollers provide new customers with confidence in their purchasing decisions. Whether through enhanced operational efficiency, lower maintenance costs, or improved safety, these firsthand accounts are invaluable in building credibility.
In conclusion, rubber coated conveyor drive rollers are indispensable for maximizing the efficacy of conveyor systems across a multitude of industries. By offering enhanced grip, noise reduction, and durability, they meet the challenging demands of today's industrial environments. Selecting the right roller with the help of an expert ensures optimal performance tailored to specific needs, reinforcing a company's reputation for quality and reliability. With their proven track record and adaptable nature, these rollers remain a cornerstone in advancing industrial productivity and innovation.